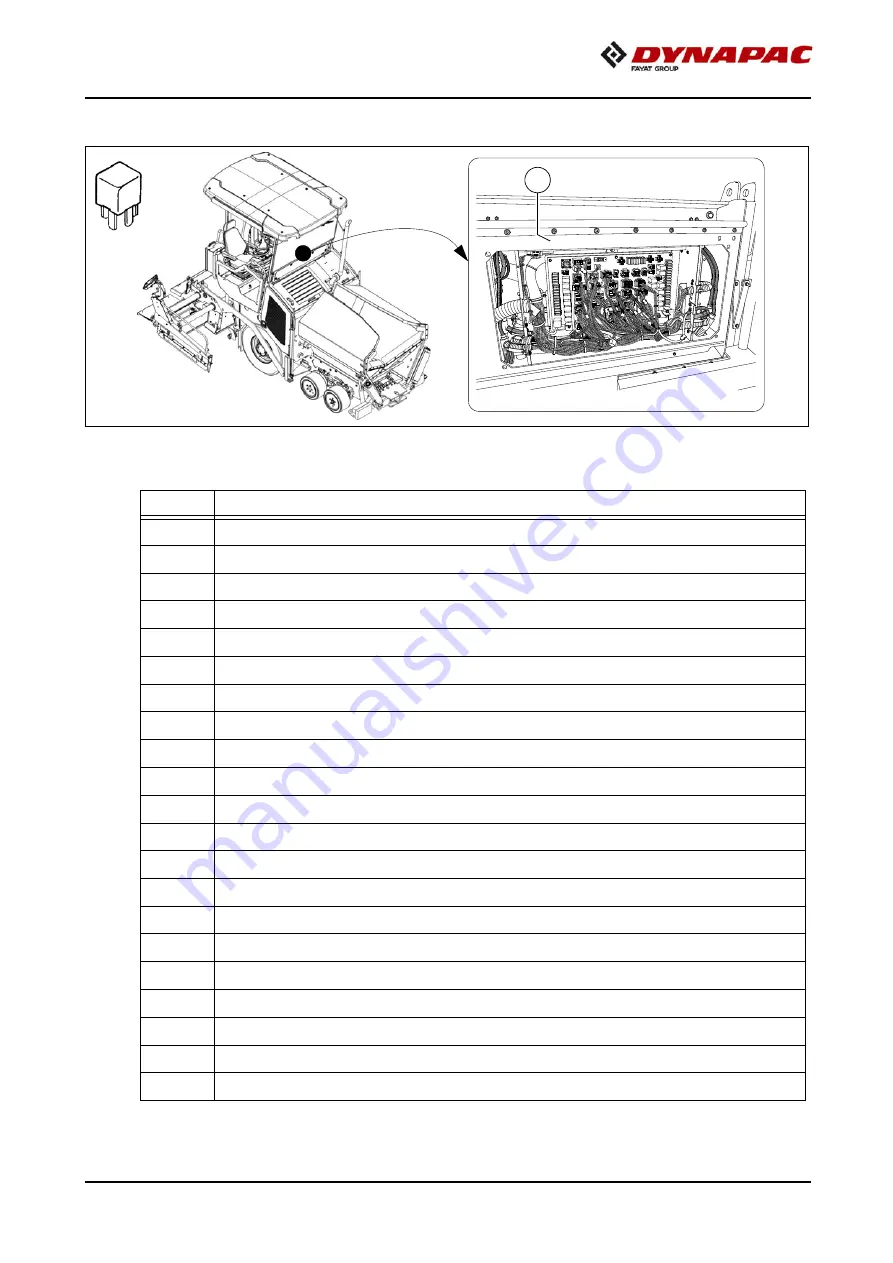
F 83.18 15
Relays in main terminal box
Relays (C)
K
K0
Engine start
K1
Switched positive
K2
Engine start / stop
K3
Control unit voltage
K4
Emergency stop
K5
Front working lights
K6
Rear working lights
K7
Auger working light
K8
Horn
K10
Right conveyor
K11
Left conveyor
K12
Left auger
K13
Right auger
K14
Levelling - left
K15
Levelling - right
K16
Rotary beacon
K20
Reverse buzzer
K21
Central lubrication
K22
Operating functions lock
K26
Fuel pump
K27
Engine pre-heating function
C
Содержание DYNAPAC F1800W
Страница 1: ...OPERATION MAINTENANCE Paver Finisher F1800W Type 912 02 0516 4812018415 ...
Страница 2: ...www dynapac com ...
Страница 10: ...8 ...
Страница 24: ...A 2 ...
Страница 32: ...B 8 4 Safety devices 10 7 2 11 4 5 6 7 2 1 9 12 3 10 8 ...
Страница 42: ...B 18 22 21 22 21 22 21 8 52 4 5 72 6 50 2 1 28 29 30 3 33 32 31 3 20 60 12 25 10 26 9 23 6 11 27 24 34 34 ...
Страница 43: ...B 19 71 70 40 41 42 xxxxxxxxxxxxxxxxx 51 53 73 ...
Страница 58: ...B 34 ...
Страница 86: ...D 12 18 4 10 15 16 19 18 20 17 14 11 12 10 ...
Страница 88: ...D 12 18 6 10 15 16 19 18 20 17 14 11 12 10 ...
Страница 90: ...D 12 18 8 10 15 16 19 18 20 17 14 11 12 10 ...
Страница 92: ...D 12 18 10 24 23 ...
Страница 94: ...D 12 18 12 26 25 ...
Страница 96: ...D 12 18 14 28 27 30 29 ...
Страница 98: ...D 12 18 16 28 27 30 29 ...
Страница 100: ...D 12 18 18 32 31 ...
Страница 102: ...D 12 18 20 34 33 ...
Страница 104: ...D 12 18 22 35 ...
Страница 106: ...D 12 18 24 37 36 ...
Страница 108: ...D 12 18 26 38 ...
Страница 110: ...D 12 18 28 39 ...
Страница 112: ...D 12 18 30 40 ...
Страница 114: ...D 12 18 32 41 ...
Страница 116: ...D 12 18 34 43 42 ...
Страница 118: ...D 12 18 36 44 45 46 47 ...
Страница 120: ...D 12 18 38 48 50 51 49 ...
Страница 122: ...D 12 18 40 48 50 51 49 ...
Страница 124: ...D 12 18 42 52 53 54 55 56 57 ...
Страница 126: ...D 12 18 44 60 64 63 65 67 62 61 66 68 69 ...
Страница 128: ...D 12 18 46 60 64 63 65 67 62 61 66 68 69 ...
Страница 132: ...D 12 18 50 90 91 92 95 94 96 93 97 97 ...
Страница 134: ...D 12 18 52 ...
Страница 139: ...D 30 18 5 Control platform telescoping seat consoles 10 B A B 11 6 4 5 2 8 A 9 7 12 ...
Страница 172: ...D 30 18 38 ...
Страница 177: ...D 42 18 5 1 3 10 2 8 6 6 4 5 7 9 ...
Страница 180: ...D 42 18 8 1 3 10 2 8 6 4 5 7 9 6 ...
Страница 183: ...D 42 18 11 2 3 4 1 ...
Страница 185: ...D 42 18 13 1 2 3 5 7 6 ...
Страница 187: ...D 42 18 15 2 3 1 6 5 4 ...
Страница 191: ...D 42 18 19 1 A 3 2 4 ...
Страница 193: ...D 42 18 21 1 2 5 6 7 4 11 10 3 8 12 9 ...
Страница 196: ...D 42 18 24 1 2 ...
Страница 198: ...D 42 18 26 1 3 14 16 2 9 7 6 4 13 15 5 8 4 11 5 10 12 ...
Страница 200: ...D 42 18 28 2 Malfunctions 2 1 Error code display and query for engine 3 1 2 ...
Страница 208: ...D 42 18 36 ...
Страница 223: ...F 21 18 1 F 21 18 Maintenance review 1 Maintenance review 83 18 90 100 50 18 60 18 40 18 71 18 30 18 ...
Страница 225: ...F 30 18 1 F 30 18 Maintenance conveyor 1 Maintenance conveyor ...
Страница 232: ...F 30 18 8 ...
Страница 233: ...F 40 18 1 F 40 18Maintenance auger assembly 1 Maintenance auger assembly ...
Страница 257: ...F 60 18 1 F 60 18 Maintenance hydraulic system 1 Maintenance hydraulic system ...
Страница 273: ...F 71 18 1 F 71 18 Maintenance travel drive steering 1 Maintenance travel drive steering ...
Страница 284: ...F 71 18 12 ...
Страница 285: ...F 83 18 1 F 83 18 Maintenance electrical system 1 Maintenance electrical system ...
Страница 300: ...F 83 18 16 ...
Страница 308: ...F 90 18 8 ...
Страница 309: ...F 100 1 F 100 Tests stopping 1 Tests checks cleaning stopping ...
Страница 320: ...F 100 12 ...
Страница 322: ...F 111 18 2 2 6 6 1 7 3 4 5 ...
Страница 328: ...F 111 18 8 ...
Страница 329: ......
Страница 330: ...www dynapac com ...