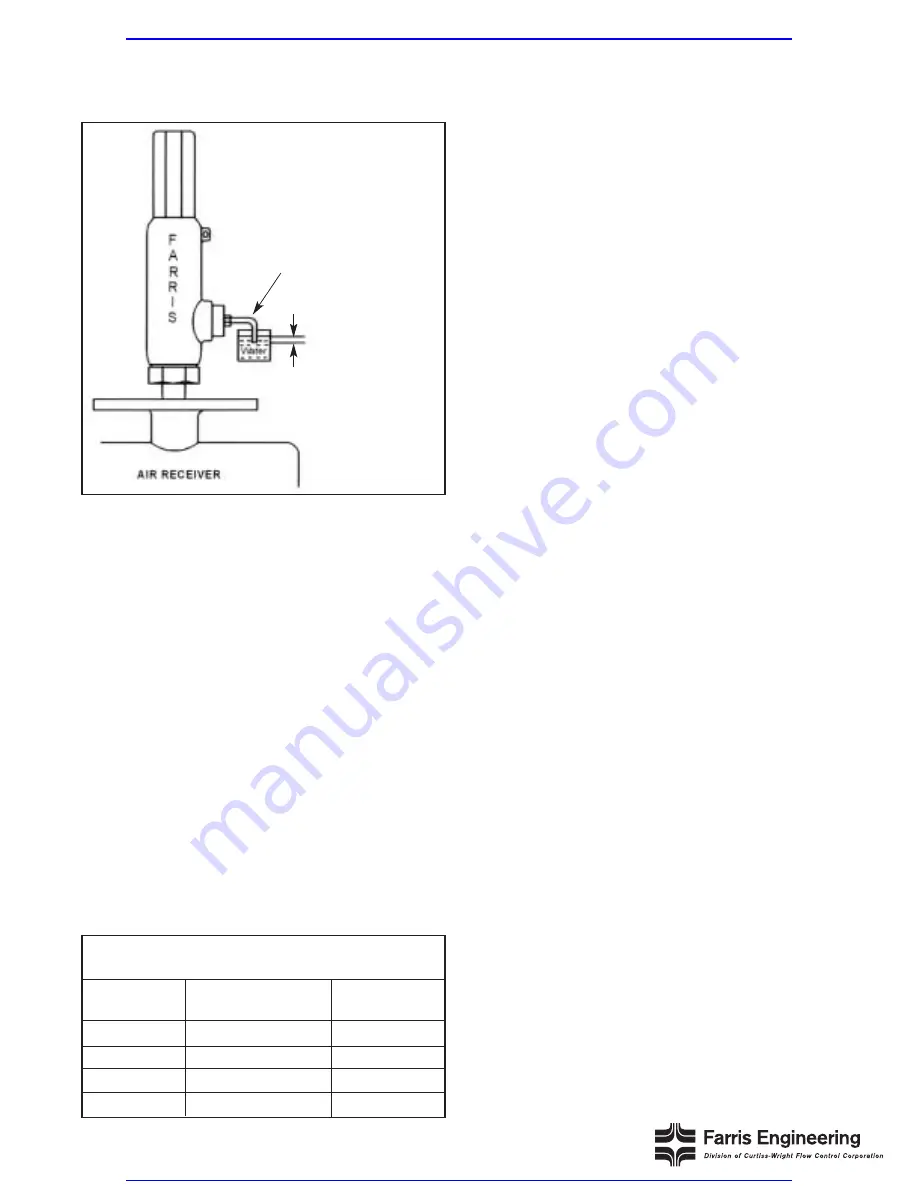
9
Seat Leakage Test
1. After the set pressure test, perform the seat leakage
test. With the valve mounted on the test stand,
attach a blind test fixture as shown in Figure 1.8
(air, gas & vapor service valves only). For steam
and water seat leakage testing, see #4-5.
2. For metal and soft seated valves, the pressure is
held at 90% of cold differential test pressure
(CDTP) when CDTP is greater than 50 psig. For
CDTP of 50 psig and below, the pressure should be
held 5 psig below CDTP.
3. Bring the pressure up and hold it for one minute for
valves up to 2” inlet size, two minutes for valves
from 2 1/2”-4” inlet size, and five minutes for valves
with inlet sizes 6” and larger. Count the number of
bubbles for one minute. See Table 3 for acceptance
criteria for metal seat valves. For O-ring and soft
seat valves, there should be no leakage (zero
bubbles per minute).
4. Steam: Apply test pressure as per #2 for three
minutes before seat tightness test. Observe the
valve for leakage for at least one minute. There
should be no audible or visible sign of leakage at
the valve outlet when viewed against a black
background.
Where the Code allows ASME Section VIII steam
valves to be tested on air, seat leakage may be
verified using the procedure for air, gas & vapor
service as listed in #1-3.
5. Water: Liquid valves are tested on water. Apply test
pressure as per #2 for two minutes. There should
be no visible sign of leakage.
Note: When performing the seat leakage test on
valves with open levers, a plain screwed test cap must
be used to prevent venting of the test pressure
through the top of the bonnet.
Backpressure Test
1. The backpressure test applies to all valves
designed to discharge to a closed system, including
valves with plain caps and packed lever assemblies.
Open lever valves and valves with exposed springs
(open bonnet) do not require this test.
2. Test the secondary pressure zone of all valves
exceeding 1” inlet size with air or other suitable gas
at a pressure of at least 30 psi. Use a suitable leak
detection solution to verify tightness of all gasket
joints and vent/drain plugs.
3. If leakage is detected at any location, rework the
valve to eliminate the leak path.
SEAT LEAKAGE RATES FOR AIR,
GAS & VAPOR SERVICE
Set Pressure
Leakage Rate Std. Cubic Feet
(psig)
Bubbles per Minute per 24 Hours
15-1000
40
0.60
1500
60
0.90
2000
80
1.20
6500
100
1.50
Figure 1.8
Tube 5/16” (7.9 Millimeters) OD x 0.035 Inch
(0.89 Millimeter) Wall
1/2” (12.7 Millimeters)
Note: Test fixture should contain a
suitable device to relieve body
pressure in the event the valve
accidentally opens.
Table 3
Visit www.boighill.com to request a quote.
Visit www.boighill.com to request a quote.