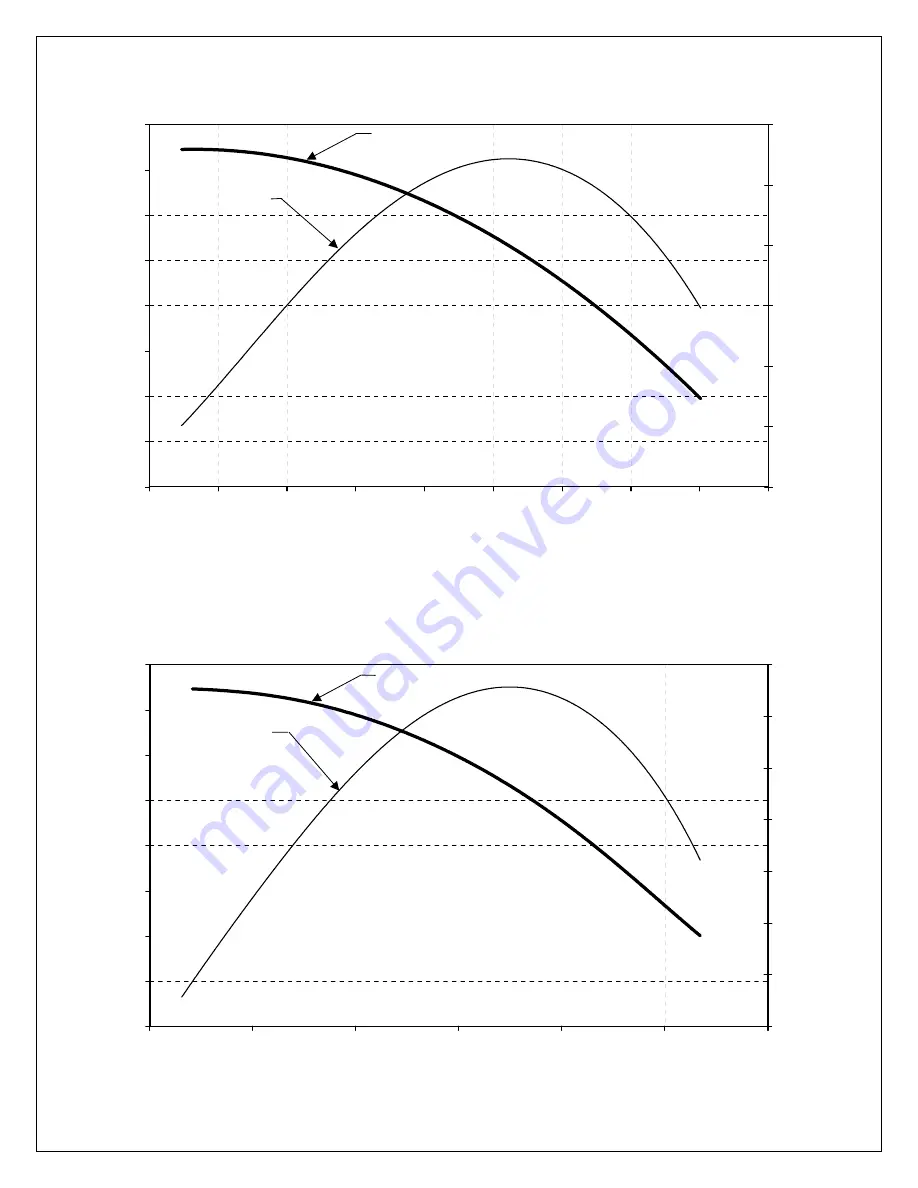
47
NYB 18PLR-6.0-60-9
0.0
2.0
4.0
6.0
8.0
10.0
12.0
14.0
16.0
3,000
3,500
4,000
4,500
5,000
5,500
6,000
6,500
7,000
7,500
FLOW RATE (cfm)
STATIC PRESSURE (in H
2
O)
11.0
11.5
12.0
12.5
13.0
13.5
14.0
BRAKE HORSEPOWER
STATIC PRESSURE
BRAKE
HORSEPOWER
Figure 400.7.6
6000 CFM, 9.1" H
2
O, 3500 RPM, 13.6 BHP
NYB 18PLR-8.0-60-9
0.0
2.0
4.0
6.0
8.0
10.0
12.0
14.0
16.0
4,000
5,000
6,000
7,000
8,000
9,000
10,000
FLOW RATE (cfm)
STATIC PRESSURE (in H
2
O)
15.0
15.5
16.0
16.5
17.0
17.5
18.0
18.5
BRAKE HORSEPOWER
STATIC PRESSURE
BRAKE
HORSEPOWER
Figure 400.7.7
8000 CFM, 9.1" H
2
O, 3500 RPM, 18.2 BHP