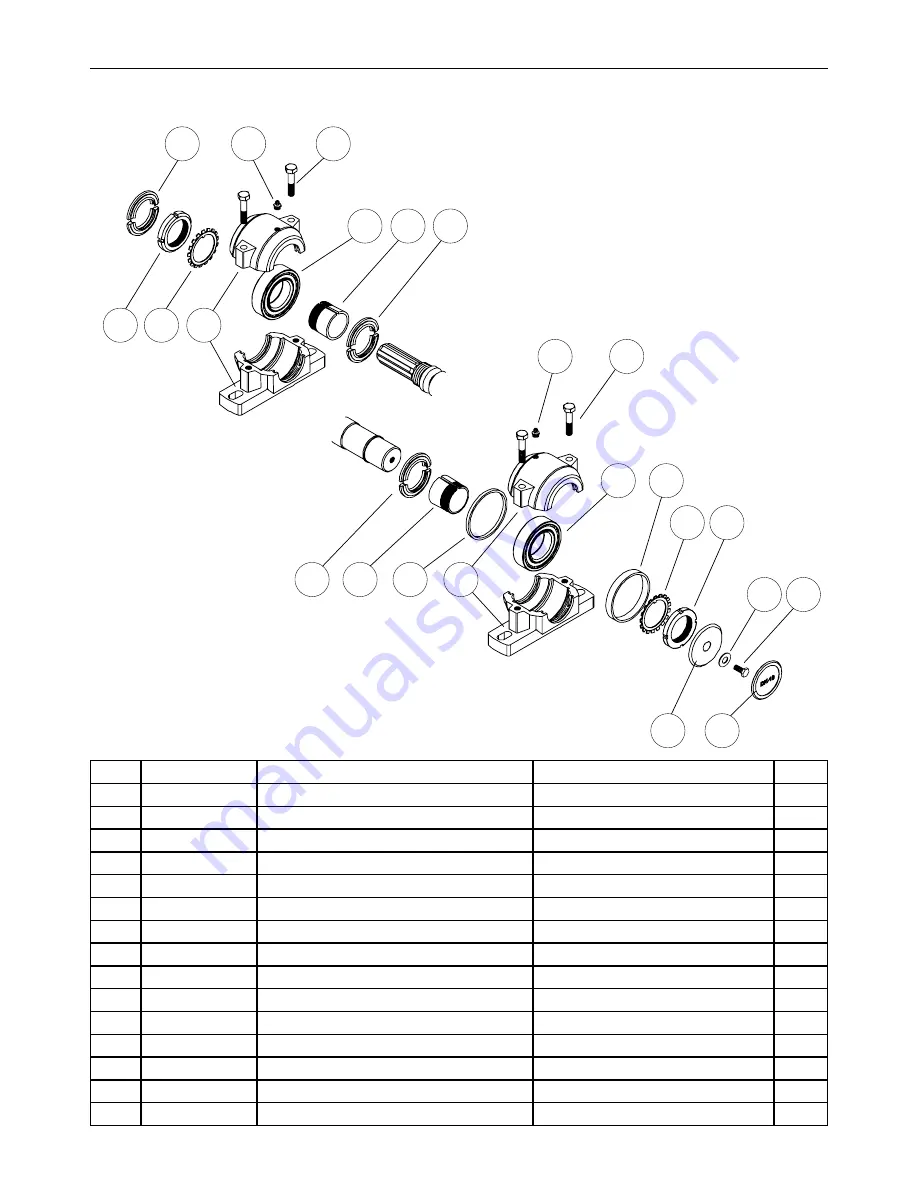
FARMI 100F
32
1
7
6
5
4
3
7
5
4
2.1
2.3
5.2
5.1
2.2
5.1
5.2
7
2.3
2.1
2.2
8
9 10
Part
Order no
Description
Remarks
Qty
1
54513569
Dust cover
1
2
54512371
Tightener sleeve
complete
2
2.1
-
Axle nut
1
2.2
-
Locking plate
1
2.3
-
Tightener sleeve
1
3
43513360
Spacer ring
D90/83X12.7
1
4
54512363
Tapered roller bearing
2
5
54513590
Bearing housing
2
5.1
52401015
Grease nipple
AR1/8
1
5.2
-
Screw
M10x50 DIN 931 10.9
2
6
43513350
Spacer ring
D90/83X5.4
1
7
52334232
Seal
1
8
43340934
End plate
1
9
52214251
Lock washer
M10 NORD-LOCK
1
10
52060928
Screw
M10X20 DIN933 88
1
FARMI 100 BEARING SYSTEM
Содержание 100F
Страница 28: ...FARMI 100F 28 FARMI 100 CHIPPER ...
Страница 35: ......