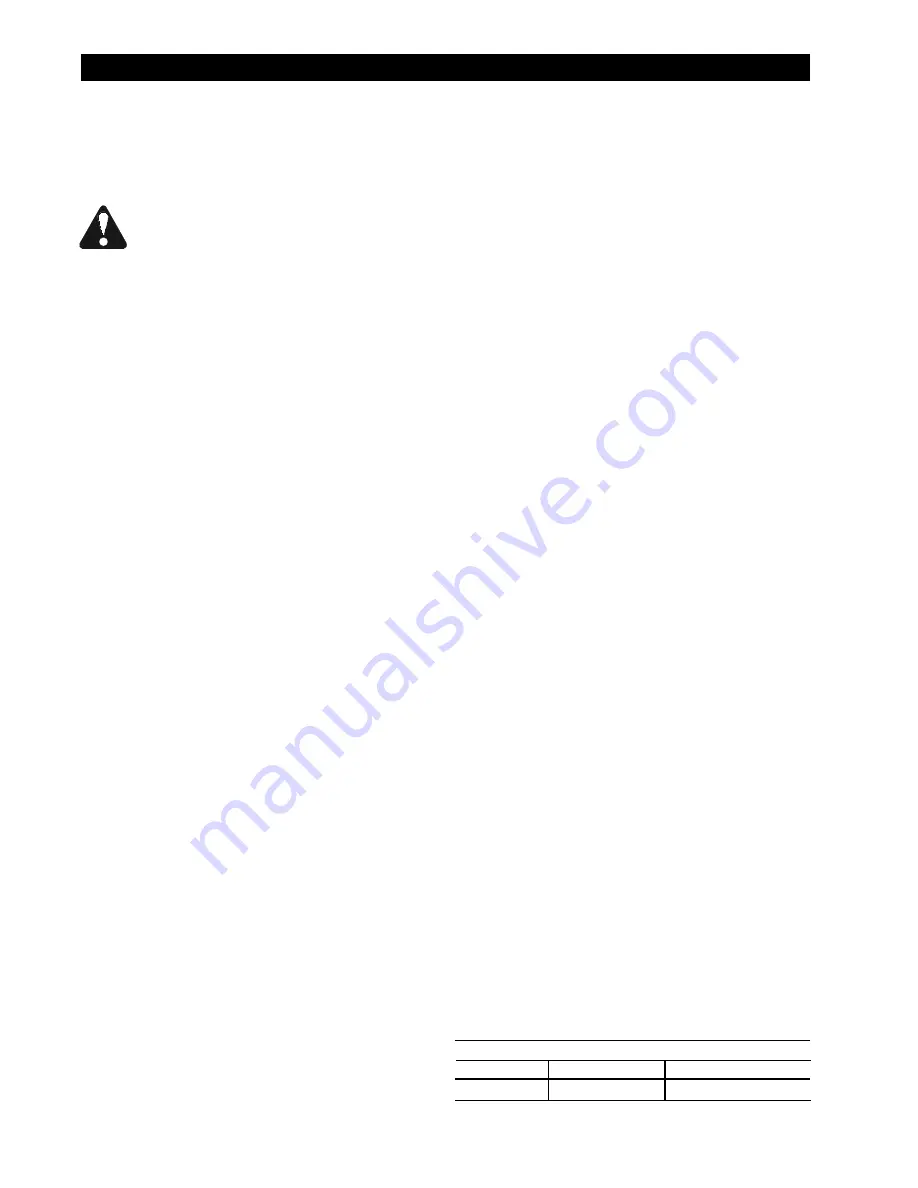
6
FAN WHEEL REMOVAL & INSTALLATION
The fan wheel is secured to the motor shaft by the use
of a taper-lock bushing, motor shaft key, and cap-
screws. The size, quantity, and torque of capscrews
required will depend on the model of the fan.
CAUTION: Although the taper-lock method of
retaining the wheel onto the motor shaft is very
simple and obvious, it is essential that the follow-
ing points be read carefully and fully understood, as
improper installation can result in serious or fatal injury
caused by a loose, fast flying wheel.
THREADED BUSHING HOLES: The threaded holes
within the bushing are provided for disassembly pur-
poses only. Do not attempt to use these holes for
reassembly, as they will not allow the parts to become
locked onto the shaft, thereby causing an extremely
hazardous operating condition.
CLEARANCE HOLES: When reassembling parts, the
capscrews must be installed through the UNTAPPED
CLEARANCE HOLES to cause the wheel to be pulled
forward onto the tapered bushing, thus locking the
parts securely onto the motor shaft. Refer to text for
assembly details.
REMOVAL
1. LOCK-OUT THE MAIN POWER SUPPLY and remove
the fan guard and inlet cone.
2. Remove the three capscrews from the clearance holes
in taper-lock bushing. Inspect for thread damage and
set aside for later reinstallation (do not use these bolts
for step 3, bushing removal).
3. Install two Grade 5 (or better) capscrews into the
THREADED HOLES in the bushing and turn them in by
hand until they bottom against the front surface of the
wheel. These capscrews should not be used for
reassembly, as some thread distortion could occur dur-
ing the removal operation. Grade 5 screws are marked
with three 120° spokes on the head and are more
durable than low strength unmarked bolts.
NOTE: DO NOT ATTEMPT TO USE LOW STRENGTH
(UNMARKED) BOLTS TO REMOVE THE BUSHING,
AS THE BOLTS MAY BREAK OFF.
4. Block wheel to prevent it from turning, and GRADUAL-
LY TURN IN THE CAPSCREWS (up to 1/4 turn at
time), until the wheel breaks loose from the bushing
and motor shaft. Carefully remove bushing and wheel.
With the wheel free from the bushing, a wheel puller
can be used to pull the bushing off of motor shaft, if
required. Reattach bushing onto wheel to prevent the
loss of parts and also to maintain the original alignment
of bushing to wheel. Inspect wheel and bushing at this
time, looking for any cracks, thread or bolt damage,
warpage, etc. Consult your dealer or the factory for
any questions concerning damage.
INSTALLATION
1. Carefully clean motor shaft, key, bushing and bore of
wheel. MAKE SURE MAIN POWER IS LOCKED OUT,
and that shaft and key are completely free of rust and
burrs. Do NOT lubricate the bushing or capscrews.
CHECK AND MAKE SURE ALL MOTOR MOUNT
BOLTS ARE PROPERLY TIGHTENED.
Before installing the wheel, check the following: (1) All
foreign material should be removed from the wheel. (2)
Carefully inspect the wheel weldment and hub casting
for damage, cracks, or other defects. Contact the fac-
tory if there is any question regarding the structural
integrity of the wheel.
2. Slide wheel over motor shaft and locate it against the
motor.
3. Align the keyway in the bushing with the key and SLIDE
bushing onto motor shaft. Do not attempt to drive the
bushing onto the shaft, as it may damage the motor
bearings.
4. Rotate the bushing and wheel so their key slots are in
line and loosely attach the wheel to the bushing.
MAKE SURE THE CAPSCREWS ARE INSERTED
INTO THE UNTHREADED CLEARANCE HOLES IN
THE BUSHING. Refer to previous CAUTION note.
Locate the bushing so it is approximately flush with the
end of motor shaft.
Make certain that the proper capscrews are used for
reassembly and no damage has occurred to these
screws during disassembly! Use only the special type
bolts supplied with the original wheel.
5. Install inlet cone, checking clearance between fan
wheel and inlet cone. Shift the location of inlet cone as
required to center it in relation to the fan wheel, provid-
ing equal clearance completely around the fan wheel.
Tighten inlet cone bolts.
6. Slide the wheel forward onto the taper-lock bushing
and turn the capscrews in by hand as far as possible.
NOTE: The bushing must be located far enough for-
ward so the distance from the inside of the backplate of
the wheel weldment to the closest edge of the inlet
cone is equal to the dimension shown as ‘A’ in the Fan
Dimension Chart. Add approximately 1/8” to this
dimension to allow the wheel to be pulled toward the
inlet during tightening.
7. Use an INCH-POUNDS torque wrench and GRADU-
ALLY TIGHTEN the three capscrews (1/4 turn at a
time) until the taper bushing becomes fully seated.
Refer to the following chart for recommended capscrew
tightening torques. DO NOT EXCESSIVELY OVER-
TIGHTEN THE BUSHING.
S E R V I C E
Browning Taper-Lock Bushing Bolt Tightening Torques
Bushing Size
Hex Bolt Size
Torque (Inch-Lbs.)
P
5/16-18x1-1/4
192