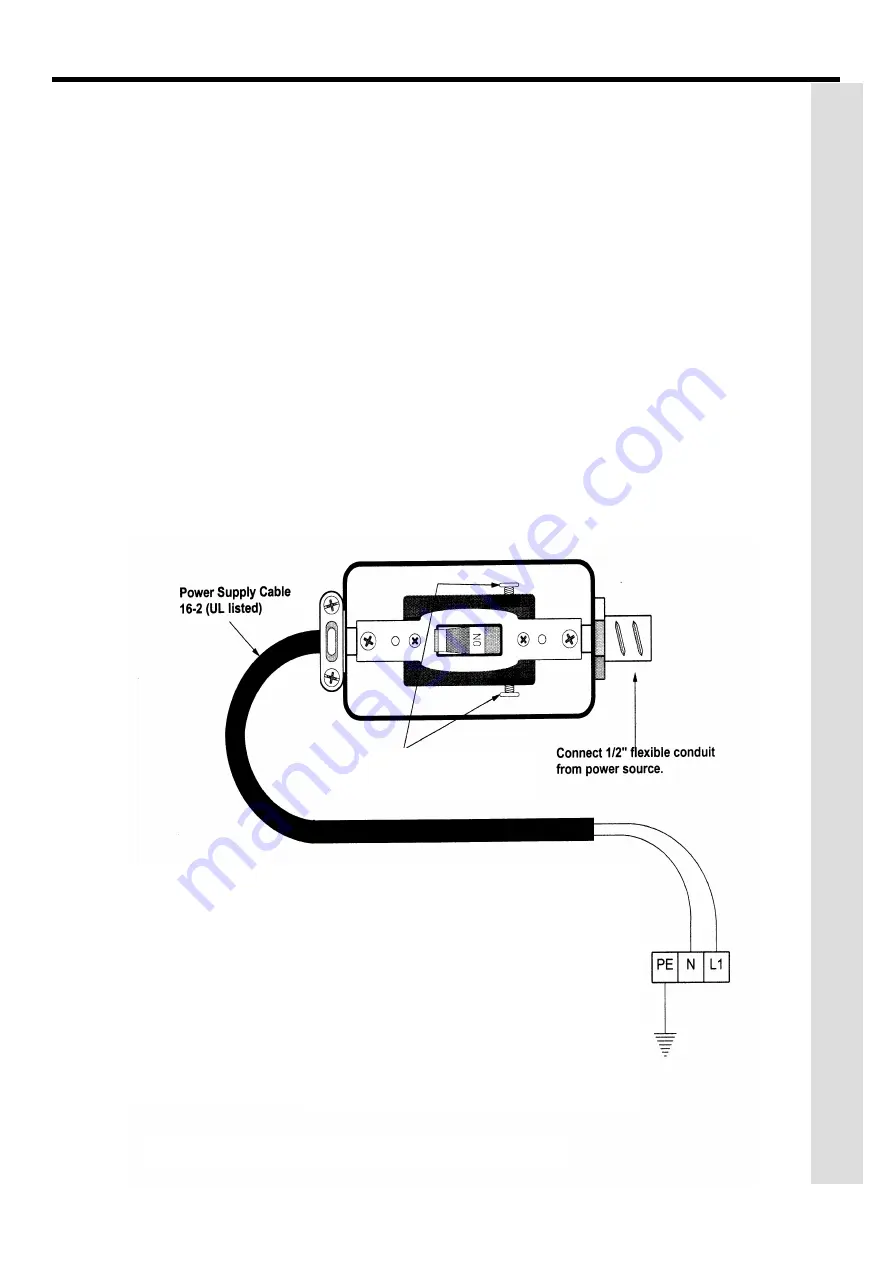
P ag e 2 5
January, 2007
620/640 Operator And
624BLD Control Panel Installation Manual
T
HE
624 BLD C
ONTROL
P
ANE
L
I
NS
T
A
LLA
T
ION
I
NS
TRUCTION
S
C
ONNECTING
THE
M
AIN
P
OWER
S
WITCH
The installer is responsible for providing a grounded
circuit protected by a 15 amp circuit breaker from the
main power source to the operator.
N
OTE
: Your standard 220VAC/115VAC power
source meets the specification for
230VAC/115VAC, +6 or -10%.
All wiring should conform to applicable electrical codes
and all wiring and fittings should be weather
proof
and/or suitable for burial.
To connect the main power source to the barrier,
remove the cover of the main power switch at the top
of the inside of the barrier cabinet. Then run the main
power wires from the base of the cabinet up through
flexible conduit that is on the cabinet door side of the
steel cross member. Run the wires and conduit through
the connector on the right side of the junction box for
the main power switch.
C
AUTION
: Do
not
run the main power conduit up
the metal channel in the right front of the cabinet.
The right front channel houses wiring for the limit
switches and is appropriate
only
for low-voltage
wiring.
Connect the main power ground wire to the ground
screw in the junction box. Connect the other wires to
the line side of the switch (see Figure 4C). The 624 BLD
control panel is already connected to the load side of
the main power switch.
C
AUTION
: U.L. listing
requires
the use of flexible
conduit around the main power wiring from the
base of the barrier cabinet to the flexible conduit
connector on the junction box of the main power
switch.
Figure 4C. Main power switch comes to you wired to
the control panel as shown here. The installer must
run wires to the empty side of the switch.
Connect 230VAC/115VAC
to this side of the switch.