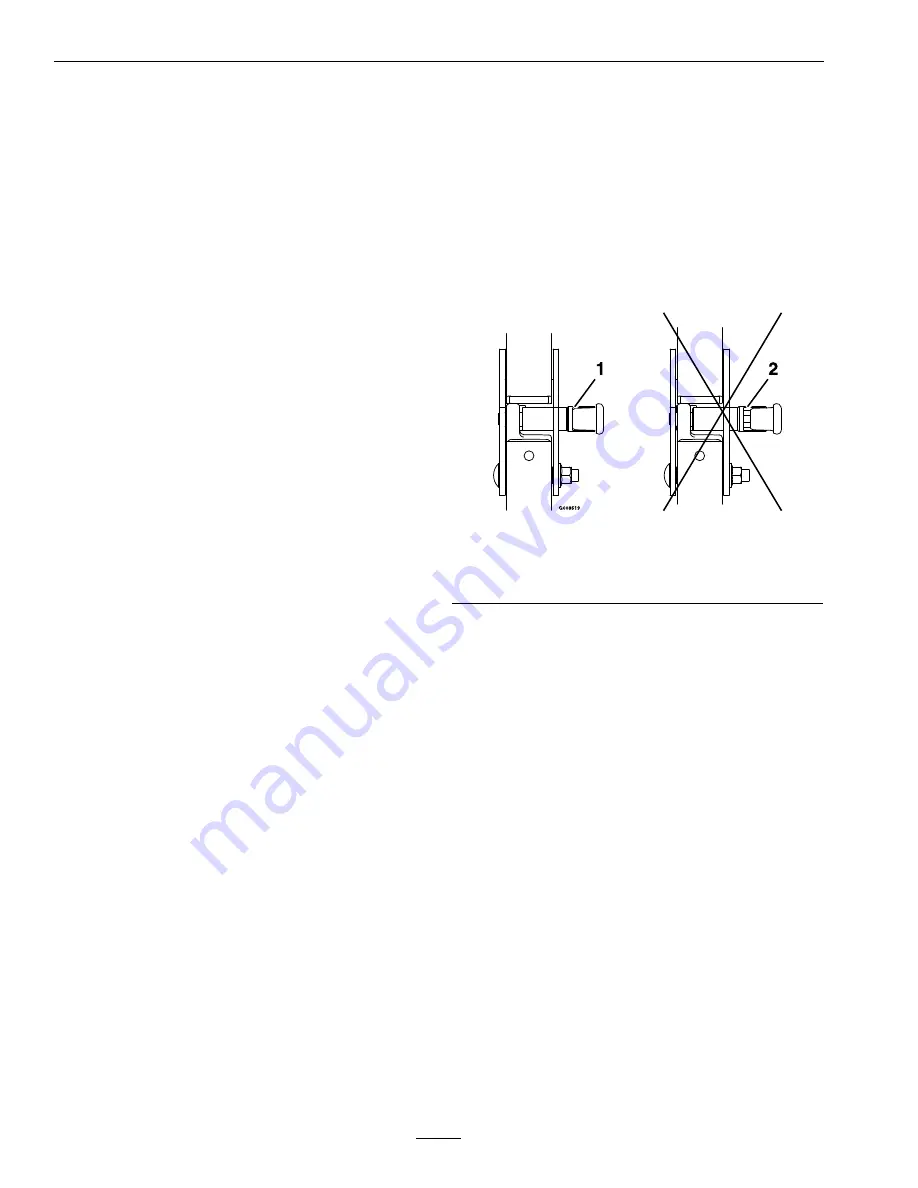
Maintenance
lock
position. The operator does not need to be
in the seat to start the engine.
Try to start with
operator in seat
, parking brake
disengaged, PTO disengaged and motion control
levers in the
neutral lock
position - starter
must
not crank
.
Try to start with
operator in seat
, parking brake
engaged, PTO
engaged
and motion control
levers in the
neutral lock
position - starter
must
not crank
.
Try to start with
operator in seat
, parking
brake
engaged
, PTO
disengaged
,
and the left
motion control lever in
, starter
must not crank
,
repeat again with the
right lever in
, then with
both levers in
- starter
must not crank
.
2. Check the kill circuits. Run engine at one-third
throttle,
disengage
parking brake and
raise off
of seat (but do not get off of machine) engine
must initiate shutdown
after approximately 1/2
second has elapsed (seat has time delay kill switch
to prevent cut-outs on rough terrain).
Run engine at one-third throttle,
engage PTO
and
raise off
of seat (but do not get off of
machine) engine
must initiate shutdown
after
one second has elapsed if the handles are in. The
delay will be 1/2 second if the handles are out.
Run engine at one-third throttle, with brake
disengaged, move levers in and raise off seat (but
do not get off of machine) engine must
initiate
shutdown
after 1/2 second has elapsed.
Again, run engine at one-third throttle, brake
engaged
, and move
left motion control lever
in
- engine
must initiate shutdown
after 1/2
second has elapsed.
Repeat again moving the
right lever in
, then
moving
both levers in
- engine
must initiate
shutdown
after 1/2 second has elapsed whether
operator is
on seat or not
.
Note:
If machine does not pass any of these tests,
do not operate. Contact your authorized
EXMARK
SERVICE DEALER.
Important:
It is essential that operator safety
mechanisms be connected and in proper
operating condition prior to use for mowing.
Check Rollover Protections
Systems (Roll Bar) Knobs
Service Interval: Before each use or daily
Check that both the mounting hardware and the
knobs are in good working condition. Make sure the
knobs are fully engaged with the ROPS in the raised
position. The upper hoop of the roll bar may need
to be pushed forward or pulled rearward to get both
knobs fully engaged.
Figure 22
1.
Engaged
2.
Partially engaged — Do
Not operate with ROPS
in this condition.
Check Seat Belt
Service Interval: Before each use or daily
Visually inspect seat belt for wear, cuts, and proper
operation of retractor and buckle. Replace before
operating if damaged.
Check for Loose Hardware
Service Interval: Before each use or daily
1. Stop engine, wait for all moving parts to stop, and
remove key. Engage parking brake.
2. Visually inspect machine for any loose hardware
or any other possible problem. Tighten hardware
or correct the problem before operating.
Service Air Cleaner
Service Interval: Every 200 hours—Service
the air cleaner. (May
need more often under
severe conditions. See
the Engine Owner’s
32
Содержание Advantage Series 4500-466
Страница 1: ...LAZER Z ADVANTAGE SERIES MODELS For Serial Nos 790 000 Higher Part No 4500 466 Rev B ...
Страница 11: ...Safety 107 2102 107 2112 109 3148 109 7232 1 Fast 3 Neutral 2 Slow 4 Reverse 109 7330 109 7929 11 ...
Страница 53: ...Schematics Hydraulic Diagram 53 ...
Страница 55: ...Notes 55 ...
Страница 56: ...Notes 56 ...
Страница 57: ...Service Record Date Description of Work Done Service Done By 57 ...
Страница 58: ...58 ...
Страница 59: ...59 ...