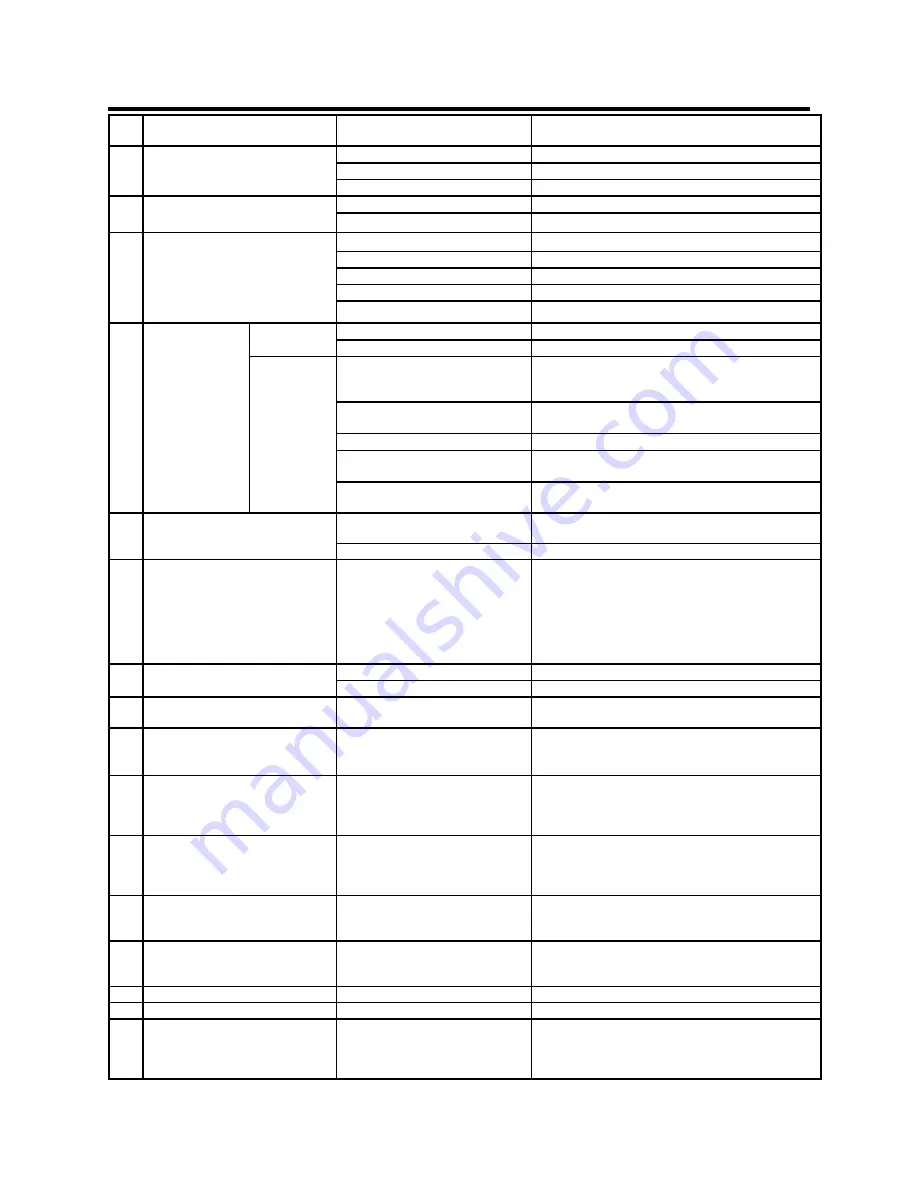
32
Section 3
Trouble Shooting
NO
.
Trouble
Possible Cause
Solution
1
Unit is switched on, but the power
light isn
’
t on
Switch damaged.
Replace.
Unit Fuse damaged.
Replace.
Power breaker tripped.
Reset.
2
After welding machine is over-
heating and the fan does not work
Fan damaged.
Check fan housing and fan. Replace if necessary.
Fan power connector is loose.
Tighten wires, check for dislodged connectors.
3
When torch switch is pressed, no
gas Flows
No gas in the gas cylinder.
Replace.
Gas pipe leaks gas.
Resolve .
Gas solenoid valve damaged.
Check and clean/replace.
Torch switch damaged.
Repair or Replace.
Control board damaged.
Inspect the circuit.
4
Wire
-
feeder does
not work
Wire reel
does not turn
Motor damaged/Fuse blown.
Check and Replace.
Control circuit damaged.
Check the board.
Wire reel
turns
The tensioner is loose or wire slips
on rollers. Wrong size drive roll.
Wire is not mated in drive groove.
Increase tension. Check for proper drive roll size/type.
Make sure wire is in groove not riding on top of the
drive roller shoulder.
The drive roller doesn
’
t fit the
diameter of weld wire.
Change roller or wire size to match.
Wire Spool is damaged.
Change out wire spool.
Gun liner is jammed.
Repair or change it, clear wire from liner/clean liner
with compressed air.
Contact Tip is jammed because of
slag or burn back.
Clean or replace. If with Aluminum, increase tip size to
next size.
5
No arc, or no output voltage
Work clamp engaged in wrong
connector.
Change polarity.
Control circuit damaged.
Check the circuit.
6
Welding stops and warning light is
on, Wire continues feeding but no
arc
Self
-
protection has engaged.
Check over
-
voltage, over
-
current, over
-
temperature,
lower
-
voltage and over
-
temperature. Allow unit to cool
if over heated. If an OC, use a shorter wire stick out or
smaller diameter wire or reduce power settings with
large diameter wires. Check power plug for problems.
If easily tripped the Resistor value too low. (Contact
Everlast if OC is tripping regularly with normal settings.)
7
Welding Voltage/Current is uncon-
trollable
Potentiometer damaged.
Repair or Replace it.
Control board damaged.
Check the circuit.
9
Intermittent Arc/ Wandering arc
Work Clamp is not secure or it is
damaged. Too windy/breezy.
Check and/or Work Clamp, change position of clamp
and attach direct to the work. Move out of wind.
10
Excessive spatter
Voltage too high too high arc force/
Too high wire speed. Too much
torch angle. Wrong size nozzle
Lower voltage or increase wire speed. Check torch
angle for less than 15° push or pull. Change arc force
settings to reduce spatter. Change nozzle size.
11
Weld sooty or oxidized looking
Poor metal prep, poor gas flow, too
much torch angle, wrong gas type,
windy or breezy. Plugged nozzle
Thoroughly clean metal, check gas flow and reposition
gun so gas flow is not creating turbulence. Move in-
doors if necessary. Reposition the welder so its fan will
not blow on the weld area. Clean nozzle.
12
Bird nesting of the wire around the
drive roll
Jammed gun liner, wire too soft
(aluminum), gun hose is kinked or
coiled too tightly. Too much ten-
sion / pressure on wire feeder .
Reduce wire feed tension so that drive will slip if it
encounters too much resistance Check Gun and liner
and replace if necessary. Straighten cable.
13
Wire feeds irregularly
Wrong drive roller or wrong size
drive roller, too little tension on
wire, wire in wrong groove.
Check and match wire size to groove size, increase
tension on drive rollers. Check to make sure the wire is
not riding on the shoulder of the drive roller.
14
Wire burns back and seizes in tip
Wrong contact Tip size or too much
burn back time set.
Match tip size for wire diameter. Reduce burn back
time. If using with aluminum, use tip designed for
aluminum or use one size larger tip than the wire.
15
Nozzle arcs to work piece welding
Nozzle plugged with spatter
Check/clean nozzle and use a nozzle dip.
16
In Stick mode will not arc
Cables not connected, inverter issue
Check connections.
17
In Stick mode, the rod sticks
Arc force control is set too low, arc
striking method is poor, wrong
polarity, too low of amperage. Wet
welding rods or wrong kind.
Check polarity. Increase arc force control. Change arc
striking method. Increase amperage. Use fresh welding
rods when possible.