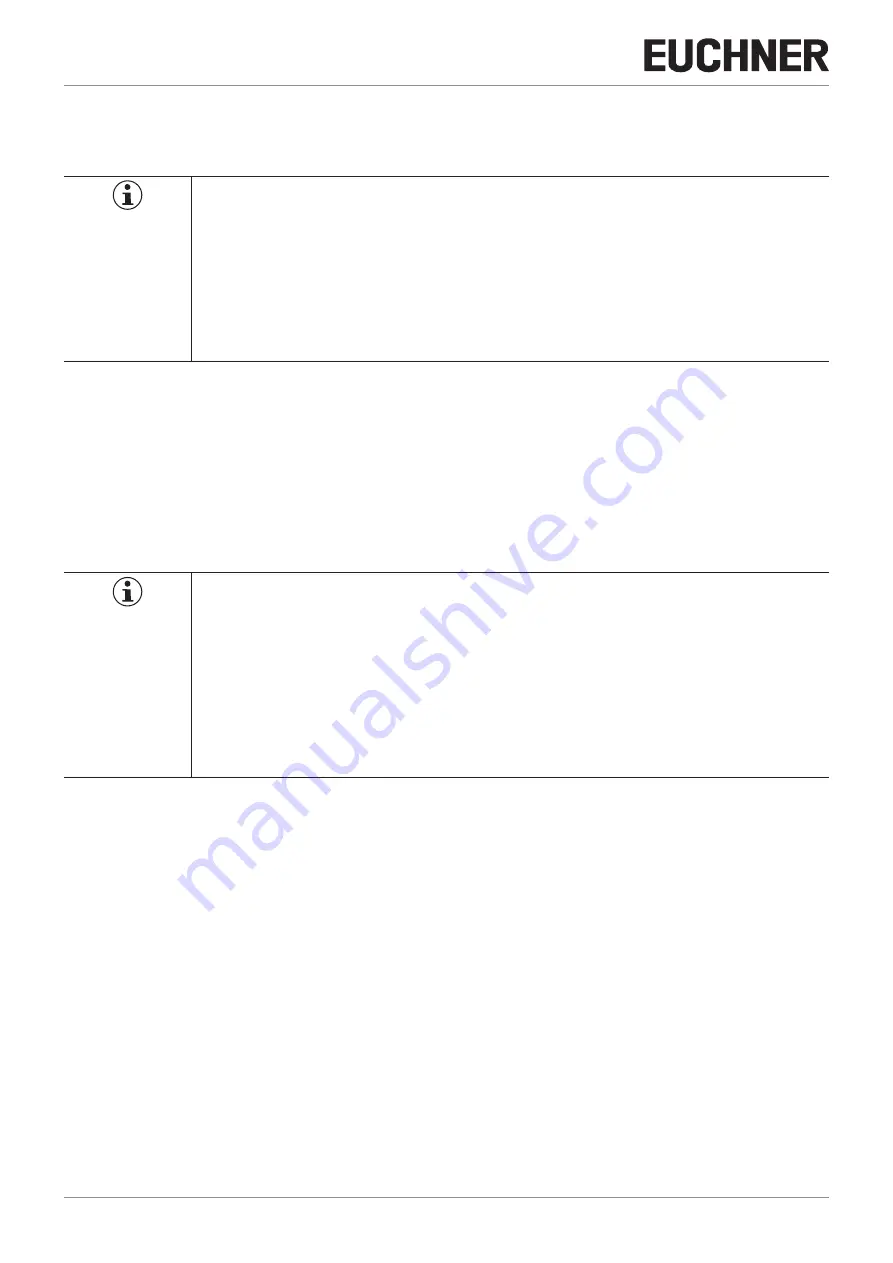
Operating Instructions Safety Systems
MGB-L..B-EI-… (Ethernet/IP) and With Data Structure Type A
24
(translation of the original operating instructions) 2126330-10-03/21
14. Setup
14.1. Integrating into Ethernet/IP and CIP Safety
®
NOTICE
Ì
The parameters
Request Packet Interval
and
Connection Reaction Time Limit
have a decisive influ-
ence on the reaction time of the safety function. The safety function could be lost if the reaction
times are too long.
Ì
With the setting SCID = 0, the function of the safety program must be safeguarded in the PLC.
Ì
It is recommended to assign to all safe networks and safe subnetworks an
SNN
that is unique
across the entire system.
Ì
Before the MGB can be integrated into a safe network, an IP address must be assigned.
Ì
The device can be operated on control systems from firmware version 20.011.
Detailed information about setup can be downloaded from www.euchner.com.
For this purpose enter application number AP000223 in the search box. An AOI is also available on the Internet. For this
purpose enter application number AP000224 in the search box.
When configuring, bear in mind that each MGB requires eight concurrent CIP connections.
14.2. Teach-in operation (only for MGB unicode)
The handle module must be assigned to the locking module using a teach-in function before the system comprising locking
module and handle module forms a functional unit.
The system is in a safe state (bits
FI.L
,
FI.B
,
FI.L
,
FI.SK
and
FI.UK
are not set) during a teach-in operation.
Important!
Ì
The locking module disables the code for the previous handle module if teach-in is carried out for
a new handle module. Teach-in is not possible again immediately for this device if a new teach-in
operation is carried out. The disabled code is deleted in the locking module only after a third code
has been taught-in.
Ì
The locking module can be operated only with the last handle module taught-in.
Ì
If, in the teach-in standby state, the locking module detects the handle module taught-in or a
disabled handle module, the teach-in standby state is ended immediately and the locking module
changes to normal operation.
Ì
If the bolt tongue is in the actuating range for less than 30 s, the handle module is not taught-in.
Teaching-in handle module
1. Fit handle module.
2. Close safety device. Check for correct alignment and distance using the marking on the locking module and re-adjust
if necessary.
3. Insert bolt tongue into the locking module.
4. Apply operating voltage to the locking module.
¨
Teach-in operation starts, green LED (State) flashes slowly (approx. 1 Hz). The teach-in standby state is active for 3 min-
utes after switch on. During the teach-in operation, the locking module checks whether the handle module is a disabled
handle module. Provided this is not the case, the teach-in operation is completed after approx. 30 seconds, and the
green LED (State) goes out. The new code has now been stored, and the old code is disabled.
5. Reset via bit
Q.PF
in the data block of the diagnostic function to activate the taught-in code of the handle module in the
locking module. Alternatively, the voltage to the device can be interrupted for a few seconds.
14.3. Mechanical function test
It must be possible to insert the bolt tongue easily into the locking module. To check, close guard several times and actuate
door handle.
If available, check function of the escape release. With active guard locking it must be possible to operate the escape release
from the inside without excessive effort (approx. 40 N).