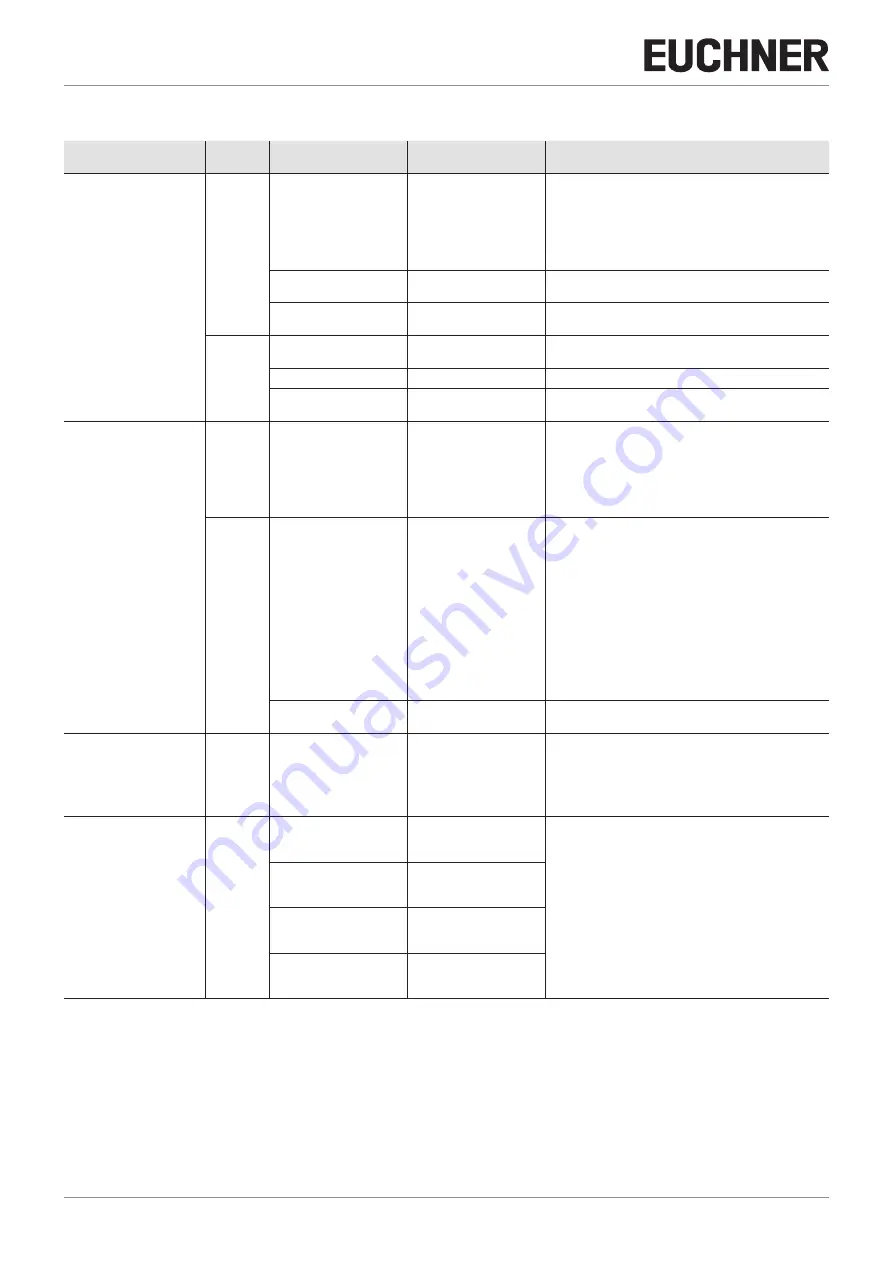
Operating Instructions Bus Module
MBM-PN-..-MLI-… (PROFINET)
30
(translation of the original operating instructions) MAN20001572-01-07/22
11.8.2. List of the parameters that can be set per module/submodule
Module/submodule
PROFINET,
PROFIsafe Parameter
Setting range / [factory
setting]
Description
Bus module MBM
PROFINET
Device name
Arbitrary designation
The device name can be assigned as required. Important: It
must match the name in the configuration software.
Tip: On replacing a faulty device, it is recommended to delete
the name in the device (factory setting). If there is no name in
the device, the existing name in the system for the previous
device is entered automatically on starting. Prerequisite: Your
PROFINET topology must be correctly configured.
IP address
If a dynamic IP address is not assigned by your control
system, a static IP address can be entered here.
Update time
250 µs … 512 ms
[automatic]
Interval until the inputs/outputs are updated.
PROFIsafe
F_dest_adr
1 … 1,022
Address of the PROFIsafe device. This address must match
the DIP switch setting on the device.
F_source_adr
1 … 65,534
Address of the control system connected to the device.
F_WD_Time
150 … 65,535 ms [600]
Time within which the device must react to a control system
request. Error if time exceeded.
Locking module MGB2
PROFIsafe
Solenoid control from the
safety program
Important:
Setting has an
effect on the safety function
(see the operating instruc-
tions of your locking module
for details)
Yes/No [Yes]
Parameter can be changed only for MGB2-L2 devices.
Im-
portant:
With the “No” setting, guard locking operates only
as process protection guard locking.
PROFINET
Solenoid control from the
standard program
Important:
Setting has an
effect on the safety function
(see the operating instruc-
tions of your locking module
for details)
Yes/No [No]
For MGB2-L1:
Here you can set manually whether the guard locking sole-
noid is also to be controlled using a non-safe bit.
For MGB2-L2:
Here you can set whether
a)
The guard locking solenoid is also to be controlled using a
non-safe bit. For this purpose, “Yes” is set
b)
The guard locking solenoid is to be controlled using only
a non-safe bit. For this purpose, “Yes” is set. The “Solenoid
control from the safety program” parameter must be set to
“No” for this purpose
c)
Guard locking is not to be used at all. For this purpose,
“No” is set. The “Solenoid control from the safety program”
parameter must also be set to “No” for this purpose
Escape release alarm
Yes/No [No]
Here you can set whether the actuation of the escape release
is to cause an error message.
Submodules
PROFINET
Submodule alignment
Do not check/top/bottom
[do not check]
For submodules on which installation rotated by 180° cannot
result in incorrect operation or functional problems, the align-
ment check can be disabled here. With “top” or “bottom” it is
checked whether the position marking for S1 is at the “top”
or “bottom” of the submodule (for marking, see data sheet
for the submodule).
Submodules with illuminated
control elements
or
submodules with indicators
or
stack light for expansion
module MCM
PROFINET
Flashing frequency H1
1 … 255
(corresponds to 0.1 …
25.5 Hz)
Here you can set the frequency at which the indicator is to
flash.
Prerequisite: corresponding output bit for the flashing func-
tion must be set.
Flashing frequency H2
1 … 255
(corresponds to 0.1 …
25.5 Hz)
Flashing frequency H3
1 … 255
(corresponds to 0.1 …
25.5 Hz)
Flashing frequency H4 (only
for stack light)
1 … 255
(corresponds to 0.1 …
25.5 Hz)