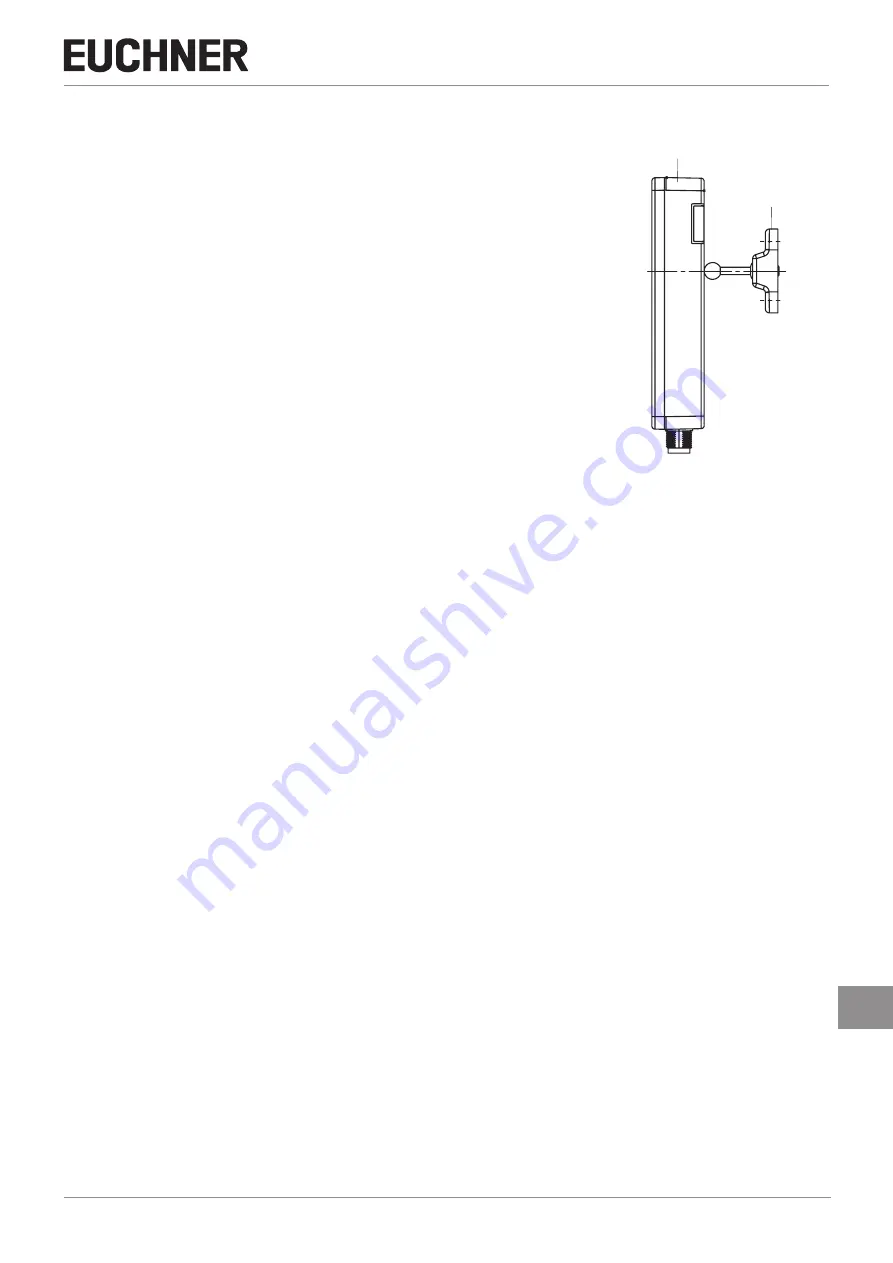
9
2525462-03-06/21 (translation of the original operating instructions)
Operating Instructions
Transponder-Coded Safety Switch CTM-LBI-BP/BR
EN
6. Function
The device permits the locking of movable guards.
The system consists of the following components: coded actuator (transponder) and switch.
Whether the device learns the complete actuator code (unicode) or not (multicode) depends
on the respective version.
Ì
Devices with unicode evaluation
: The actuator must be assigned to the safety switch
by a teach-in operation so that it is detected by the system. This unambiguous assign-
ment ensures a particularly high level of protection against tampering. The system thus
possesses a high coding level.
Ì
Devices with multicode evaluation
: Unlike systems with unicode evaluation, on multi-
code devices a specific code is not requested but instead it is only checked whether the
actuator is of a type that can be detected by the system (multicode evaluation). There
is no exact comparison of the actuator code with the taught-in code in the safety switch
(unicode evaluation). The system possesses a low coding level.
When the guard is closed, the actuator is moved into the safety switch. When the operat-
ing distances are reached, power is supplied to the actuator by the switch and data are
transferred.
The door position signal OD is set when a permissible code is detected. Guard locking is
activated automatically if no voltage is present at IMP. The safety outputs are switched on when guard locking is active.
The safety outputs are switched off and the guard locking signal OL is cleared when guard locking is released.
In the event of a fault in the safety switch, the safety outputs are switched off and the DIA LED illuminates red. The occurrence
of faults is detected at the latest on the next demand to close the safety outputs (e.g. on starting).
6.1.
Bistable guard locking
Guard locking of the switch functions according to the bistable principle. This means that guard locking is kept in its last
position if the power supply is interrupted or when the machine is switched off for servicing, for example. As a result, the
safety door is either constantly locked or it can be closed and opened as required without activating the guard locking. Guard
locking is released via control input IMP or via IO-Link communication. Also see chapter
.
6.2.
Guard lock monitoring
All versions feature two safe outputs for monitoring guard locking. The safety outputs FO1A and FO1B are switched off
when guard locking is released.
6.3.
Monitoring outputs/status bits
Depending on version, the signals listed in the following are available as a status bit or on the monitoring output. The status
bits are evaluated via the BR/IO-Link Gateway. Please refer to the enclosed data sheet for further information.
6.3.1. Door position signal OD
The door position signal is sent as soon as the actuator is inserted into the switch head (state: guard closed and not locked).
The signal is also present if the guard locking is active.
6.3.2. Diagnostic signal OI
The diagnostic signal is present if there is an error (switch-on condition as for DIA LED).
6.3.3. Guard locking signal OL
The guard locking signal is present if the guard locking is active.
6.3.4. Status signal OM
The status signal is present if the device’s safety outputs are switched.
Transponder-coded
actuator
Safety switch