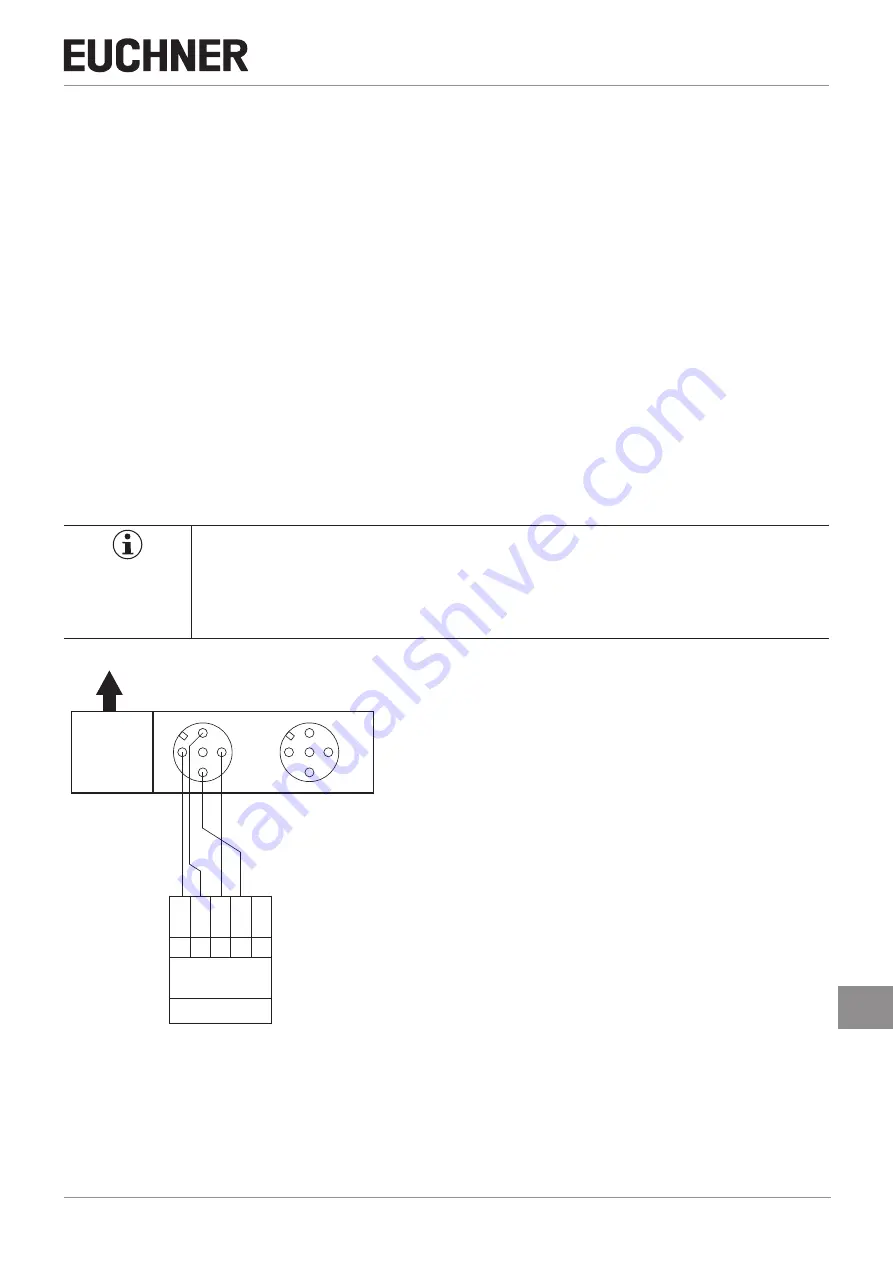
15
2112663-08-02/20 (Translation of the original operating instructions)
Operating Instructions
Non-Contact Safety Switch CES-AP-C01-…
EN
9.7. Notes on operation with safe control systems
Please observe the following requirements for connection to safe control systems:
Ì
Use a common power supply for the control system and the connected safety switches.
Ì
A pulsed power supply must not be used for U
B
. Tap the supply voltage directly from the power supply unit. If the power
supply is connected to a terminal of a safe control system, this output must provide sufficient electrical current.
Ì
The safety outputs (OA and OB) can be connected to the safe inputs of a control system. Prerequisite: The input must
be suitable for pulsed safety signals (OSSD signals, e.g. from light grids). The control system must tolerate test pulses
on the input signals. This normally can be set up by parameter assignment in the control system. Observe the notes of
the control system manufacturer. For the pulse duration of your safety switch, refer to chapter
.
A detailed example of connecting and setting the parameters of the control system is available for many devices at
www.euchner.com, in the area
Downloads/Applications/CES
. The features of the respective device are dealt with there in
greater detail.
9.8. Devices for direct connection to IP65 field modules
The version CES-AP-...-SB-... (M12, 5-pin; pin 5 not assigned) is optimized for connection to decentralized peripheral systems
with M12 plug connector, such as the ET200pro series from Siemens. The devices are parameterized and connected like
an OSSD (e.g. like light curtains).
If flying leads are used, connection to IP20 input and output modules (e.g. ET200s) is naturally also possible.
Important!
Observe the following notes prior to connection:
Ì
Parameter assignment must be performed for the input/output modules (see application example
at www.euchner.com, in the area
Downloads/Applications/CES
).
Ì
Additionally observe notes from the control system manufacturer where necessary.
CES-AP-...-SB-...
U
B
1
FO1A
2
0V
3
FO1B
4
S1: M12 plug-connector
(5-pin)
n.
c.
5
decentralized
periphery
e.g. ET 200pro
PLC
DI
1
5
2
4
3
1 5
2
4
3
DO
Figure 4:
Connection example for connection to decentralized peripheral systems