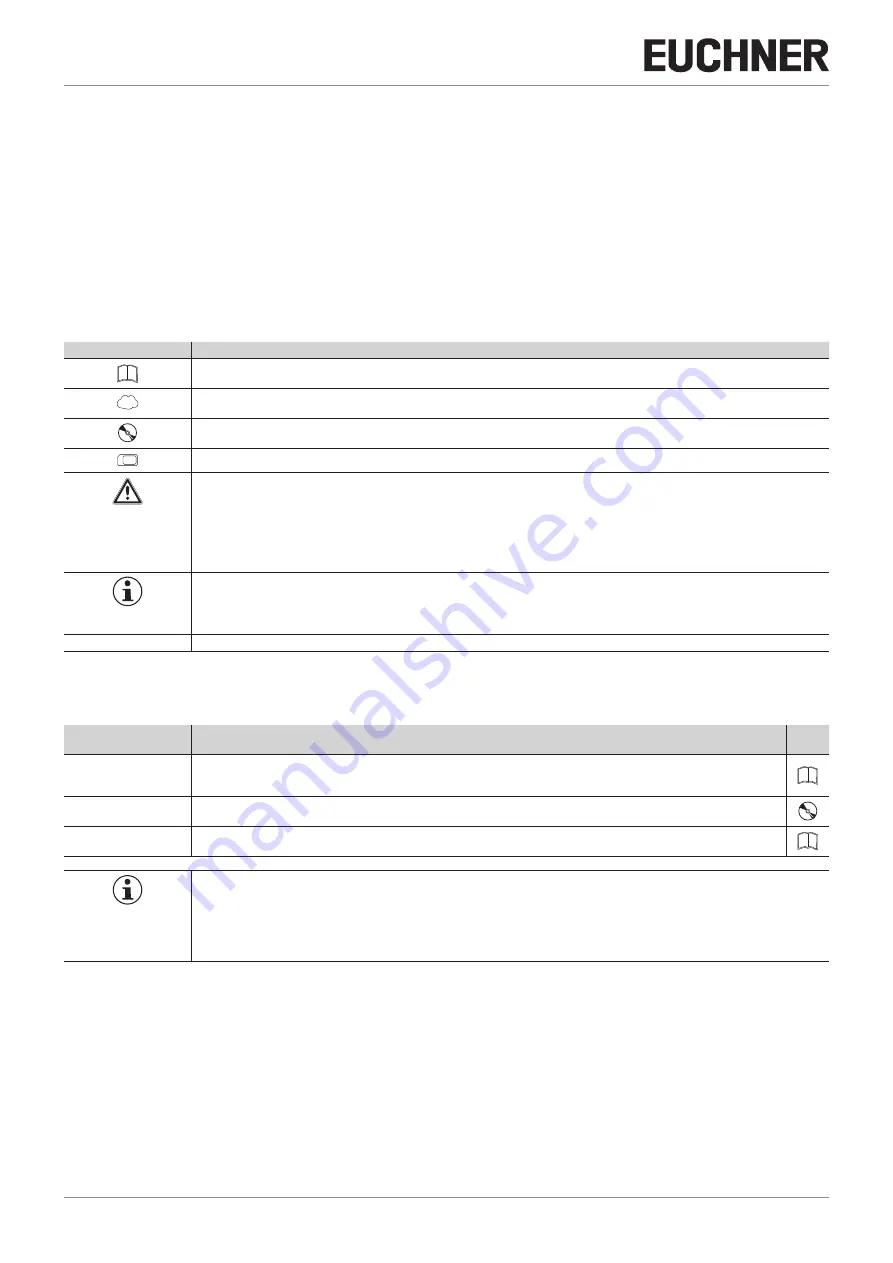
Operating Instructions
Safety System MGBS-P-L.-AR…
4
(Translation of the original operating instructions) 2527246-01-08/19
1. About this document
1.1.
Scope
These operating instructions are valid for all MGBS-P-L.-AR… from version V1.0.0. These operating instructions, the document
“Safety information and maintenance” and any enclosed data sheet form the complete user information for your device.
1.2.
Target group
Design engineers and installation planners for safety devices on machines, as well as setup and servicing staff possessing
special expertise in handling safety components.
1.3.
Key to symbols
Symbol/depiction
Meaning
Printed document
Internet
www
Document is available for download at www.euchner.com
Document on CD
MEM
This section is applicable only if the memory card is used
DANGER
WARNING
CAUTION
Safety precautions
Danger
of death or severe injuries
Warning
about possible injuries
Caution
slight injuries possible
NOTICE
Important!
Notice
about possible device damage
Important
information
Tip
Useful information
1.4.
Supplementary documents
The overall documentation for this device consists of the following documents:
Document title
(document number)
Contents
Safety Information and
Maintenance MGBS
(2519732)
Basic information for safe setup and service
Operating Instructions
(2527246)
(this document)
Possibly enclosed data
sheet
Item-specific information about deviations or additions
Important!
Always read all documents to gain a complete overview of safe installation, setup and use of the
device. The documents can be downloaded from www.euchner.com. For this purpose enter the doc.
no. in the search box.