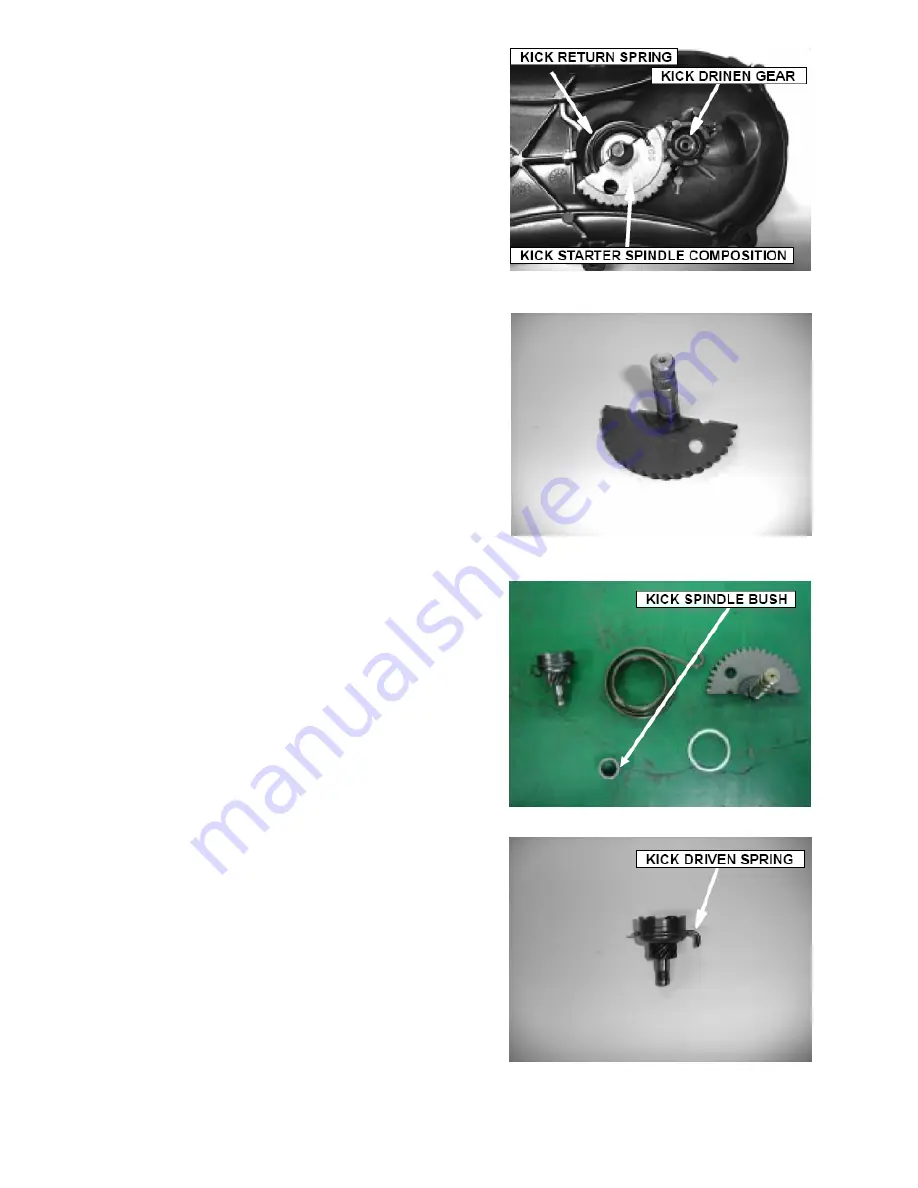
Rotate the kick-starter spindle composition to remove
the kick driven gear and spring.
Remove the kick-starter spindle composition and return
spring.
Remove the kick spindle bush.
INSPECTION
Inspect the kick starter spindle composition for wear or
damage.
Inspect the kick return spring for fatigue or damage.
Inspect the kick spindle bush for wear or damage.
Inspect the kick driven gear and spring for wear or
damage.
Содержание Matrix R4-150
Страница 1: ...ETON America MATRIX R4 150 Service Manual Covers MATRIX R4 150 PN2I SCOOTER ...
Страница 65: ...9 6 REAR SHOCK ABSORBER DRAWING ...
Страница 74: ...11 6 WIRING DIAGRAM MATRIX R4 150 ...