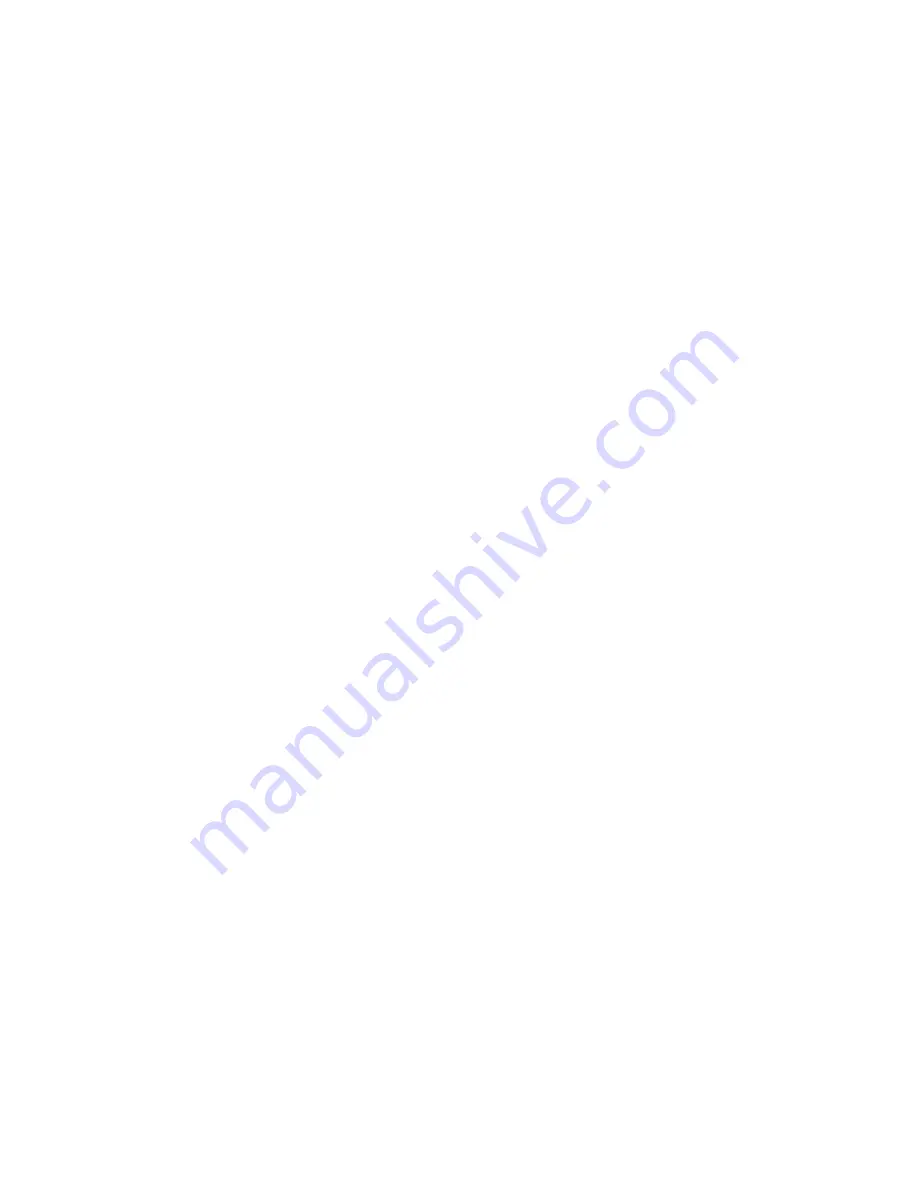
Electrical Test Instruments PI-6000
Section II - Detailed Description
==============================================================================
==============================================================================
Copyright(C) 1994-2019 Electrical Test Instruments, LLC All Rights Reserved
Page II-2
or 400-500 VAC, and will work on 50 Hz sources of 200-210 VAC or 400-420 VAC.
The line voltage is displayed on the indicator control panel digital meter. An
internal voltage sensor automatically configures the AC control power for
nominal 240 or 480 VAC, and monitors input voltage for compliance to
specifications. The main output section may be configured by means of a
simple rotary switch on the power input panel, and an interlock allows the
power section to be energized only when properly configured for the applied
voltage.
The rheostat uses a large wheel to adjust the output manually within the range
determined by the coarse tap, as well as a motorized control actuated by means
of a smart control switch. When the switch is pressed briefly, the rheostat moves
in a very small increment for fine control. When the switch is held, the rheostat
moves very quickly, so that the entire span may be traversed in less than five
seconds. The approximate rheostat position is displayed on an LED indicator bar
graph. For the PI-6000, the rheostat is always turned clockwise to increase
output.
The electronically controlled tap selection uses power contactors to set the
coarse tap. The unit powers up in the lowest tap position (1), and the setting may
be adjusted by means of a rocker switch on the indicator/control panel. If the
switch is held, the taps change at a rate of about one per second. Tap change is
not allowed when output is on.
The indicator/control panel features two temperature indicators: one for the
output bus temperature, and the other for the overall system temperature. This
is determined by a combination of actual winding temperature, and a “virtual
temperature” which is derived from time and current duty cycle usage as
monitored by a “POD”, or Programmable Overload Device. Additio
nal details are
available in a separate manual. If either temperature exceeds a safe operating
level, the interlock is asserted and the output section is de-energized. Additional
thermostatic sensors in the output transformer windings will also assert the
interlock if unsafe temperature levels are detected.
The output voltage of the test set is provided on the indicator/control panel for
monitoring by means of a separate digital voltmeter.
Primary catastrophic overload protection for the test set is accomplished with
input fuses having high interrupting current capacity. Overload of the output
system is sensed by means of the previously mentioned “POD” on the
rheostat
autotransformer, and thermal sensors in each winding and on the SCR. The
combination of these devices allows full utilization of the overload capability of
the test set and eliminates costly and cumbersome fuse replacement required
in other test sets.
The output of the test set is controlled by means of a proven SCR controller. This
provides precise initial phase angle control to reduce DC offset for inductive