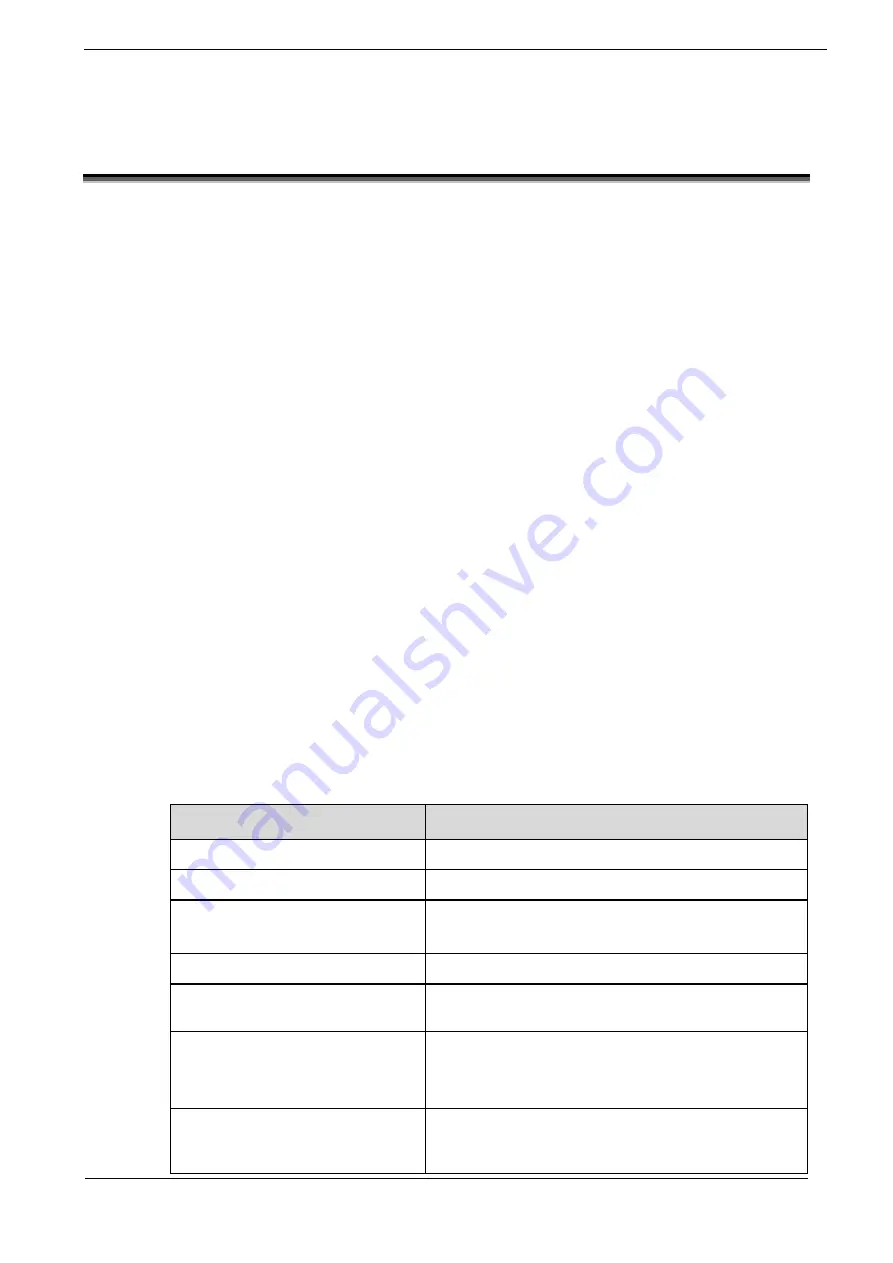
Summa Series Servodrive Product Manual
EtherCAT Communications
Document Version: V1.01
(Dec, 2019)
© 2019 ESTUN Automation Co., Ltd. All right reserved.
5-1
Chapter 5
EtherCAT Communications
5.1
Introduction
5.1.1
Protocol Overview
EtherCAT is an open network based on Ethernet to achieve real time control. It could support high speed
and synchronized control. By using efficient network topology, the network structure with too many
concentrator and complicated connections are avoided. It is very suitable to use this protocol in motion
control and other factory automation applications.
EtherCAT is registered trademark and patented technology, licensed by Beckhoff Automation GmbH,
Germany.
EtherCAT technology breaks the limits of normal internet solution. Through this technology, we don’t
need to receive Ethernet data, decode the data, and then copy the process data to different devices.
EtherCAT slave device could read the data marked with this device’s address information when the frame
passes this device. As the same, some data will be written into the frame when it passes the device. In this
way, data reading and data writing could be done within several nanoseconds.
EtherCAT uses standard Ethernet technology and support almost kinds of topologies, including the line
type, tree type, star type and so on. Its physical layer could be 100 BASE-TXI twisted-pair wire,
100BASE-FX fiber or LVDS (low voltage differential signaling). It could also be done through switch or
media converters or in order to achieve the combination of different Ethernet structure.
Relying on the ASICs for EtherCAT in the slave and DMA technology that reads network interface data,
the processing of the protocol is done in the hardware. EtherCAT system could update the information for
1000 I/O within 30 µs. It could exchange a frame as big as 1486 bytes within 300 µs. This is almost like
12000 digital output or input. Controlling one servo with 100 8-byte I/O data only takes 100 µs. Within
this period, the system could update the actual positions and status presented by command value and
control data. Distributed clock technology could make the cyclic synchronous error lower than 1 µs.
5.1.2
Specification
The specifications for EtherCAT communication are as follows.
Item
Specifications
Applicable Communications Standards
IEC 61158 Type12, IEC 61800-7 CiA402 Drive Profile
Protocol
100BASE-TX (IEEE802.3)
Communications Connectors
CN3-IN (RJ45): EtherCAT signal input connector
CN4-OUT (RJ45): EtherCAT signal output connector
Cable
Category 5, 4 shielded twisted pairs
Sync Manager
SM0: Mailbox output, SM1: Mailbox input, SM2: Process
data output, and SM3: Process data input
FMMU
FMMU 0: Mapped in process data output (RxPDO) area.
FMMU 1: Mapped in process data input (TxPDO) area.
FMMU 2: Mapped to mailbox status.
EtherCAT Commands
(Data Link Layer)
APRD, FPRD, BRD, LRD, APWR, FPWR, BWR, LWR,
ARMW, FRMW (APRW, FPRW, BRW, and LRW
commands are not supported.)