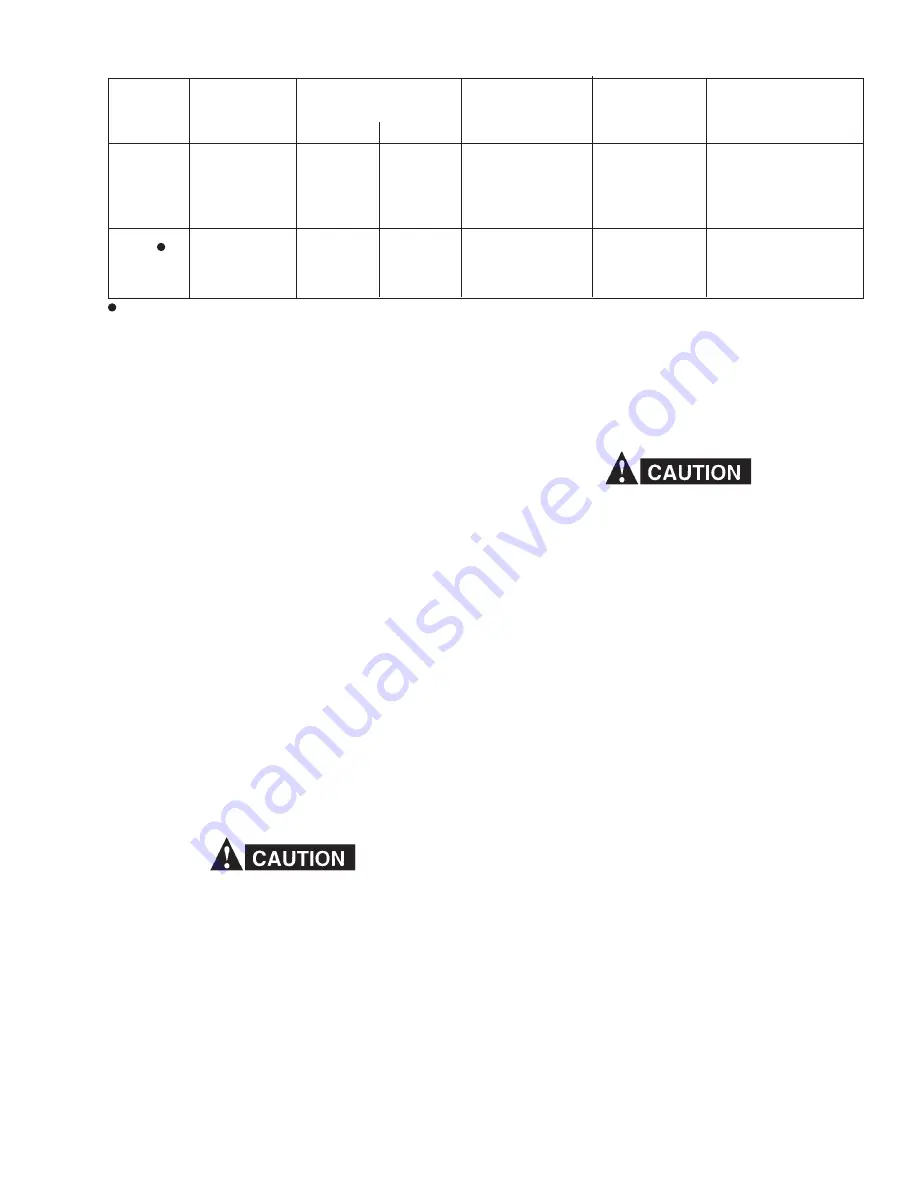
7
Table 3 - ST-16 Wire Feed Accessories Using Conduit/Replaceable Liner System
Wire
Type/
Size
Hard
Cored
Contact
Tube
(Slip-in)
996104
996105
996816
996106
996105
996816
996816
Contact Tip
(Threaded)
632794
632796
948335
632798
-
-
-
632793
632795
948308
632797
632795
948308
632797
Long Short
Wire Outlet Guide
29N13
29N13
29N13
29N13
29N13
29N13
29N13
Mig-35
Digimig
Replaceable
Spring
Liner
636843
598786
598786
598786
598786
598786
598786
Soft-Lined
Conduit
10-ft.. x (I.D.)
598922 (.195)
598922 (.195)
598922 (.195)
598922 (.195)
598922 (.195)
598922 (.195)
598922 (.195)
Use No. 12M Nozzle (P/N 997310).
B. USING CONDUITS WITH REPLACEABLE LIN-
ERS
1.
Insert the torch end of the conduit through the rear
of the torch handle and into the conduit connection
fitting.
Refering to Figure 3, loosen the two No. 10-32 screws
on locking nut (598787), slide handle back, and then
lock the conduit in place by tightening the No. 10-32
setscrew on the conduit connection fitting. Reas-
semble handle to locking nut and tighten setscrews.
2.
Insert the liner into the conduit and through the torch.
The shoulder spring about the liner should rest in-
side and below the threads of the wire feeder end of
the conduit.
3.
Slip the wire outlet guide (see Table 3) over the liner
protruding from the conduit and screw into the con-
4.
duit connection. If necessary, adjust shoulder spring
on liner so that the end of the liner is about flush with
the end of the wire outlet guide.
Complete the installation by following steps 5 through
8 as described on page 5 , (Section IV, Using Self-
Lined Conduits).
5.
V. ADJUSTMENT & OPERATION
Before adjustments are made, disengage the pessure
roll to prevent wire from feeding and arcing to an
accidental ground.
To set the shielding gas flow rate, press the torch lever
to open the gas solenoid valve and adjust the flowmeter
to the desired flow rate. For proper operation a minimun
flow of .40 gpm of cooling water at 60-deg.F or less,
must be maintained if the torch is to perform at rated
capacity. A torch inlet water pressure of 25 psi minimum
will provide adequate flow. Check these water flow re-
quirements before starting. The wire feed conduit should
be kept as straight as possible and without sharp bends
to assure smoother wire feed.
Specific operation of the torch depends on the particular
wire feeder with which it is used. Therefore, consult the
instruction manual supplied with the wire feeder.
VI. MAINTENANCE
If this equipment does not operate properly, stop
work immediately and investigate the cause of the
malfunction. Maintenance work must be performed
by an experienced person, and electrical work by a
trained electrician. Do not permit untrained persons
to inspect, clean, or repair this equipment. Use only
recommended replacements.
A. POWER CABLE
If the power cable assembly becomes damaged, it is
recommended that (1) a new one be purchased, or (2)
the damaged unit be turned over to an ESAB authorized
repair station for repair. The connection fittings are
crimped on at the factory by special crimping tools to
ensure strong connections and prevent leakage. A sat-
isfactory job cannot be done without these tools.
B. GAS AND WATER HOSE ASSEMBLIES
(Refer to Fig. 3)
If shielding gas (46V63) or water hose assemblies
(46V25) require replacement, loosen the two No. 10-32
x 3/16-in. set screws on the handle locking nut and pull
handle back.
To replace gas hose assembly, proceed as follows:
Clip off wire hose clamp (53N46) and remove hose.
1.
Clean off fitting, and then brush on some Loctite
Prism 447 (P/N 71201202 - 20 gm tube) onto the
fitting.
2.
Slide new wire hose clamp on the new hose and
insert the hose over the grooved sealing area of the
hose fitting on the torch.
3.
Using a pair of pliers, pull on the hose clamp tightly
over the grooved sealing surface and apply 1/2 twist.
Be sure to position the wire hose clamp so that the
3.