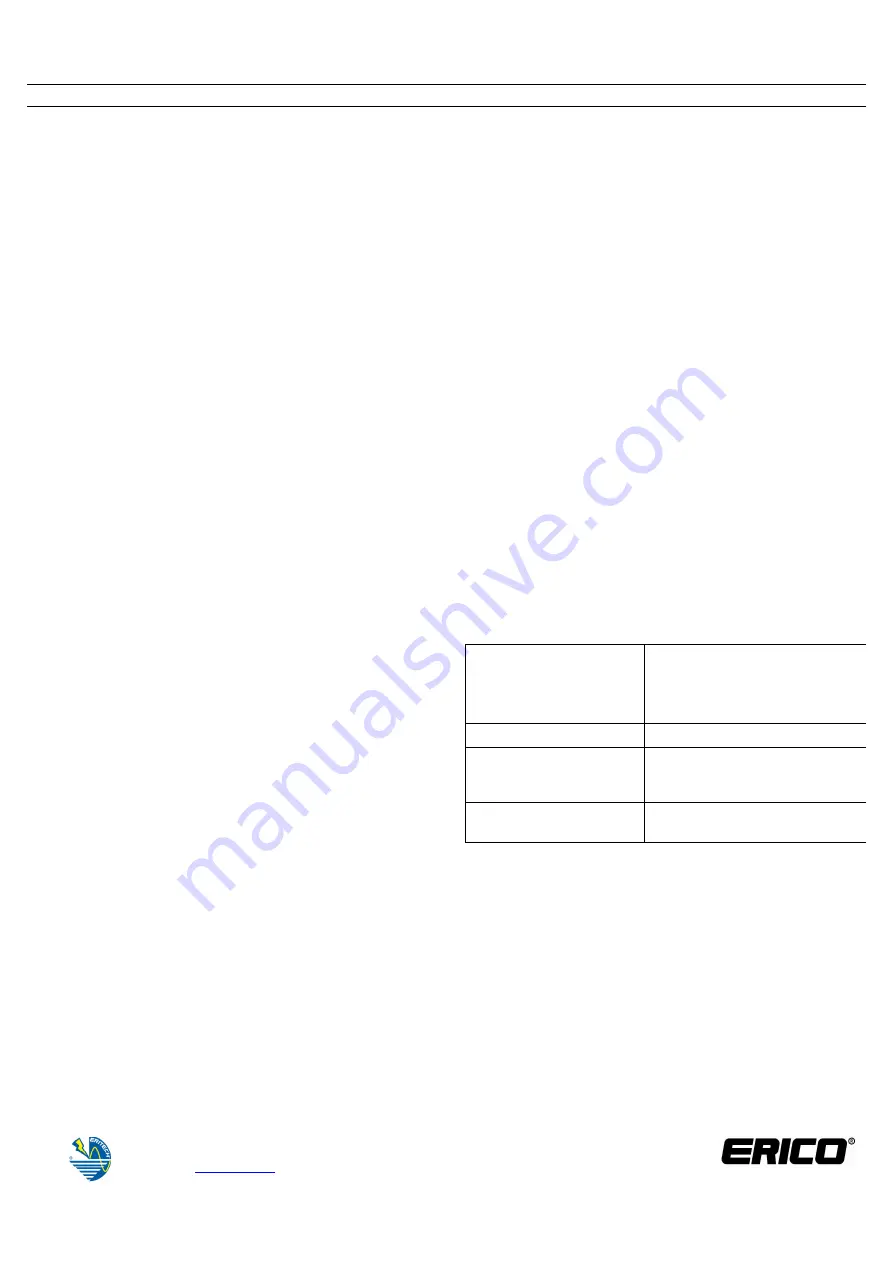
INSTRUCTION SHEET
TECHNICAL SUPPORT: IPCR1502 REV. 5
2 of 2
IPCR1502_5.DOC
www.erico.com
ESN12623
§
The location of this enclosure prevents the temperature of the
TDS unit(s) from exceeding its maximum specified rating.
§
Adequate electrical and safety protection is provided by the
enclosure to all exposed terminals.
§
The location and type of enclosure meets the specified
environmental requirements and prevents the ingress of
moisture and water.
§
The indicator status of the TDS can be readily inspected.
5. ELECTRICAL CONNECTION
When connecting the TDS on the input side of the distribution panel
wiring, it is usual to wire the TDS L-N (L1, L2, L3 to N on 3 phase
systems). When connecting the TDS to the output side of the panel
wiring, it is usual to wire it L-PE/PEN.
§
On TN-C networks, three TDS units are required. L1, L2, L3
should be protected to PEN.
§
On TN-S networks, four TDS units are required. L1, L2, L3
should be protected to N, and N should be protected to PE.
§
On TT networks, three TDS units and a SGD unit are required.
L1, L2, L3 should be protected to N using the TDS units, and N
should be protected to PE using the SGD unit.
§
On IT networks, four TDS units are required. L1, L2, L3, N
should be protected to PE using 440V TDS units on a normal
230V system.
§
On the TDS1100 series, a “Kelvin” type connection can be
made using separate input and output terminal pairs. This
configuration helps reduce the effects of lead length. The
maximum load current under such a configuration should be
limited to 125A.
6. WIRING
The interconnecting wiring should:
§
Be as short as possible - not exceeding 300mm (12”).
§
Avoid sharp bends >100mm radius is recommended.
§
Have the conductors twisted together where possible.
§
Terminals will allow connection of 25mm² (#4AWG) multi-
strand wiring or 35mm² (#2AWG) solid – ref. Table 1. The wire
insulation should be stripped back 8mm (5/16").
7. RESIDUAL CURRENT DETECTORS (RCD)
When an RCD is used, it is preferable that the TDS modules be
installed prior to (upstream of) this device to avoid nuisance tripping
which may occur during transient activity.
8. FUSING AND ISOLATION
Overcurrent protection must be installed in the upstream circuit of
every TDS unit if the mains supply is > 100A. This is to provide
protection to the TDS, the load and the wiring in the case of a fault
– ref. Table 1 for suitable fuse ratings.
NOTE:
Operation of this over-current protection under excessive
surge conditions may occur removing protection from the circuit.
The Remote Status contacts should be monitored for this
possibility.
9. STATUS INDICATION
TDS modules incorporate an internal thermal disconnect element,
which automatically disconnects the varistor from the network in the
event of a thermal overload. Should the internal disconnect
operate, a red flag appears in the transparent window of the Status
Indicator(s) on the front of the TDS.
10. MAINTENANCE & TESTING
Before removing a TDS module from service, ensure that the power
has been removed and if possible “locked out”. Qualified personnel
should only undertake replacement of TDS modules. Replacement
plug-in modules are available.
NOTE:
It is very important to ensure that the new module is of the
same type and voltage as that being replaced.
NOTE:
TDS units should be inspected periodically, and also
following any periods of lightning or transient voltage activity. Check
the Status Indicator and replace the module if required.
11. REMOTE STATUS
The TDS provides remote status monitoring via voltage-free
contacts. Failure of the TDS is signified by the N/C contacts (11,14)
opening and the N/O contacts (11,12) closing. Ensure that the
voltage and current ratings of the contacts are not exceeded.
NOTE:
The TDS contacts are
independent of whether power is
supplied, or not, to the TDS module. The status of the
contacts is given solely by the failure status of the TDS
module.
Table 1. TDS operating specifications
Max. continuous operating
voltage, Uc (AC)
170, 275, 320, 610 Vac
(Important: ensure correct TDS is
selected, Uc must be higher than
power frequency voltage).
Max Torque
4.5N.m./40in-lbs
Main terminals – wire cross
section / backup fuse
multi-strand 25 mm2 (#4AWG)
(single-strand 35 mm
2
(#2AWG)) /
max. 125 AgL
Remote status contacts
0.5 A / 250 VAC; 3 A / 125 VAC
1.5 mm
2
wire cross section