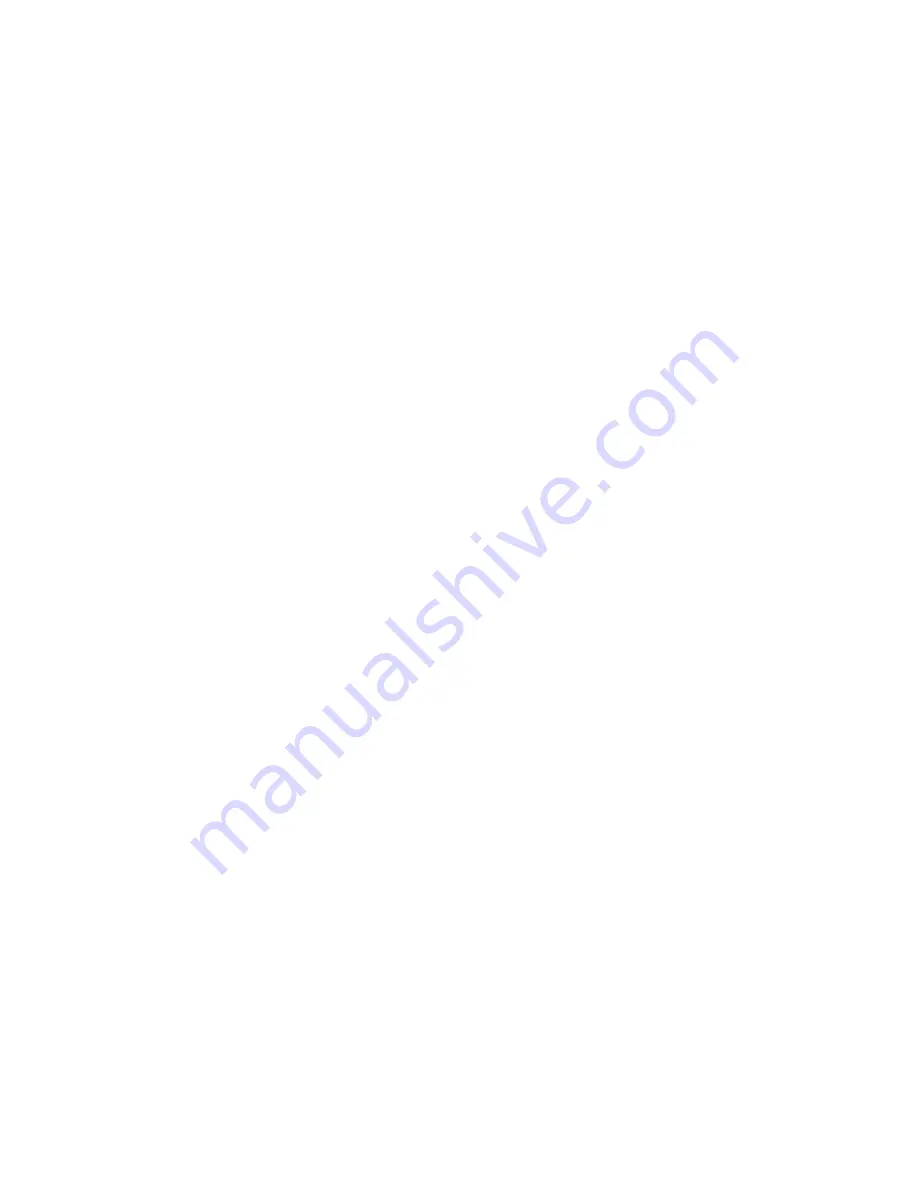
extending past the exit bushing, press the CUT key to cut and
remove the cut piece to allow the guard to open. While
paused, the length compensation may be edited with the “+”
or “-” keys. Material may be fed using the JOG key. By
depressing the JOG key, material will be fed with the length
being displayed. Each time a manual cut is performed, the
length is reset back to zero. The feed rate may be changed
while paused by pressing EDIT and selecting a new feed rate.
Press ESC/PAUSE when paused to abort the run and return
to the Batch Prompt screen. When the run is complete, the
message Run Complete will appear on the bottom line.
OPERATION:
The WC601B will not operate unless the front cover is closed.
If the cover is opened during a run the unit will stop and the
screen will display “cover open/system disabled.” The sys-
tem cannot be run until the cover is closed and the display
reads “ready to run/any key continues.” Pressing the ESC or
PAUSE key will return to the run screen in the pause mode.
Pressing the RUN key will immediately resume the run.
POWER FAILURE:
In case of a power failure, the WC601B will be reinitialized and
will not start unexpectedly. All parameters stored in a batch
program will remain in memory. Parameters in the 0 batch will
be lost. The controller is protected by a fuse located in the
back of the housing just above the IEC connector.
BLADE CHANGE, OR REPLACEMENT AND
BLADE DEPTH ADJUSTMENT
CAUTION: BE SURE UNIT IS UNPLUGGED BEFORE
CHANGING BLADES.
To replace the blade, with the front cover open, find the exit
bushing and loosen the set screw holding it in place with the
5/64" Allen wrench provided. Slide the exit bushing to the right
and remove. Next, remove one of the screws holding the blade
in place, with the 3/32" Allen wrench provided and loosen the
other one. Slide the blade out from under the screw and
washer. Replace blade, screw, and tighten.
NOTE: If this is the first time the blade has been dulled, it may
be used again by turning the blade around and using the other
side. The cutting edge of the blade is offset, so the blade may
be used twice.
To adjust the depth of the blade, locate the socket head cap
screw located on the rotary head and loosen the locking
socket head set screw, which locks the socket head cap
screw in place, using the 5/64" Allen wrench provided. To
adjust the blade deeper, turn the socket head cap screw
using the 7/64" Allen wrench provided counterclockwise. To
raise the blade, turn the screw clockwise. NEVER ALLOW
THE BLADE TO GO PAST CENTER OF BUSHING! Blade
depth is properly set when the blade is slightly deeper than
the inside wall of the tubing being cut. After adjusting the
blade depth, tighten the locking socket head set screw to
keep the blade from moving.
MAINTENANCE:
CAUTION: BE SURE TO UNPLUG THE UNIT BEFORE
PERFORMING ANY MAINTENANCE. BE SURE TO EM-
PLOY APPROPRIATE ANTI-STATIC PROCEDURES/DE-
VICES WHEN DISASSEMBLING AND ASSEMBLING UNIT.
1. Check the blade for wear after prolonged use. Due to the
number of different materials, this maintenance should be
reviewed by your plant maintenance personnel and adjusted
accordingly.
2. No other maintenance is required for the units.
TROUBLESHOOTING:
PROBLEM: The blade does not move and is stuck in a closed
position.
SOLUTION:
Adjust the blade as described in the blade change or
replacement section: Head or exit bushings may be adjusted
too close to the blade.
PROBLEM: Material does not feed properly through the bushings.
SOLUTION:
1. Tighten the belt-feed adjusting knob clockwise to increase
the belt pressure on the material.
2. Check the blade and bushing position. Readjust if necessary.
PROBLEM: Display does not function.
SOLUTIONS:
1. Check the fuse located in the rear of the housing. Only use
the recommended fuses. If the fuse continues to blow after
replacement, return the unit to the factory for repair.
2. Check the on/off switch.
PROBLEM: Poor quality cut or no cut.
SOLUTIONS:
1. Check that the blade is not dull. Replace or turn if
necessary.
2. Make certain the head and exit bushings are close enough
to the blade on both sides and chamfers are facing out.
3. Check blade depth adjustment.
4. Lower the motor cutter speed and increase the cutter on time.
5. Check cut motor brushes. Replace if less than ¼” length.
PROBLEM: Erratic cut lengths.
SOLUTIONS:
1. Check dereeler to make certain material is feeding correctly.
2. Make certain proper tension is applied to belt feed.