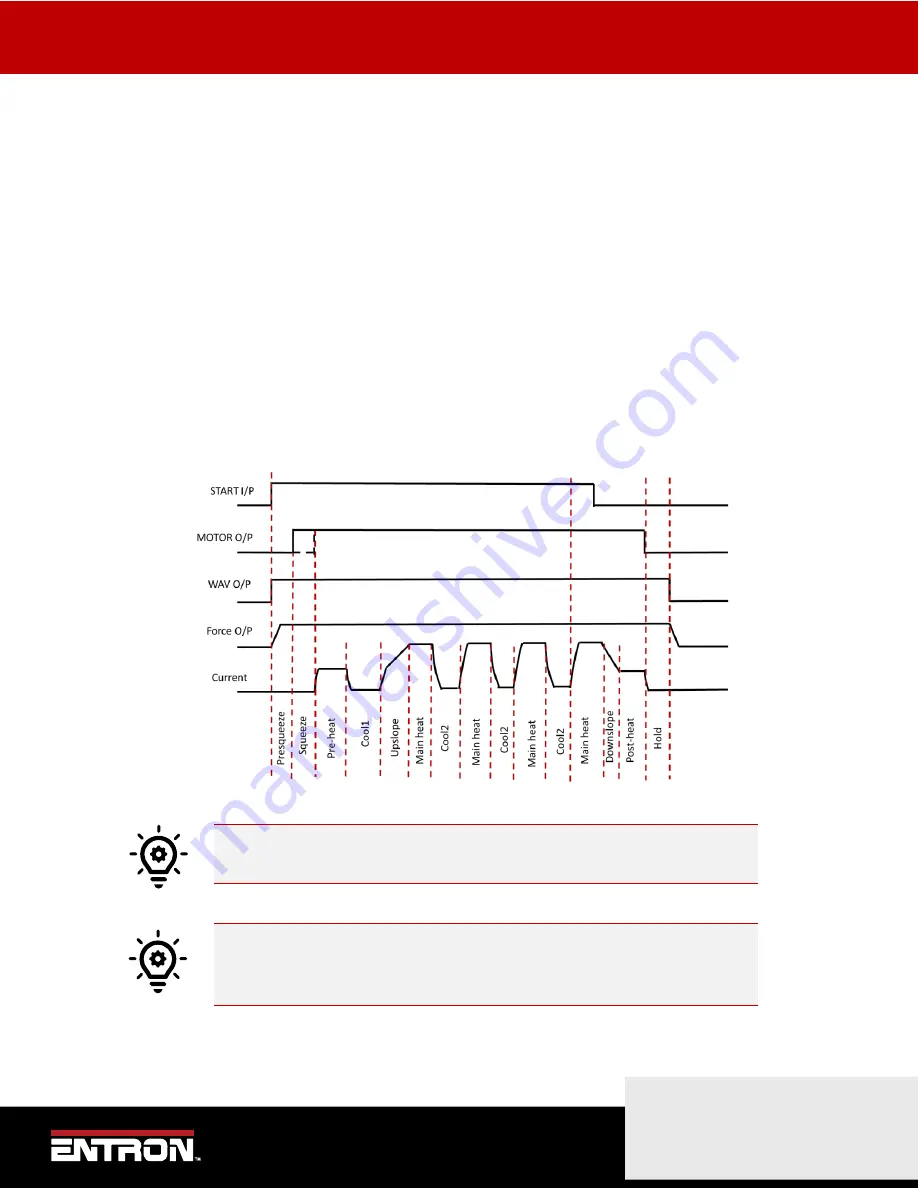
PROGRAMMING WELD PROGRAMS
Weld Program Types
102 |
P a g e
Copyright © 2021 BF ENTRON and/or its affiliates. All rights reserved
Product Model:
iPAK2v2
Firmware Version:
V2.10
May 22 | Doc No 700253-2
The timing sequence follows the order of operations defined below:
1)
The START input is initiated
2)
The WAV output is enabled to actuate the force
3)
The Presqueeze sequence is executed and the MOTOR output is enabled to drive the weld wheels
4)
The Squeeze sequence is executed
5)
The Cool1 sequence is executed
6)
An upslope current pulse is executed to ramp the current to the main heat in a controlled manner
7)
The Main heat current pulse is executed followed by the Cool2 sequence
8)
The Main heat current and Cool2 pulse is repeated while the START signal is maintained
9)
The START input is removed
10)
A downslope current pulse ramps down the current in a controlled manner
11)
A post heat weld pulse is executed
12)
The MOTOR output is disabled
13)
A Hold sequence is executed
14)
The WAV output is disabled to release the actuator
Figure 31: Seam Weld Timing Diagram
Continuous Seam Weld
For a continuous seam weld, the Cool2 parameter should be set to 0.
MOTOR
–
2
nd
Stage
The initiation of the MOTOR output signal is a function of the Second Stage
parameter.