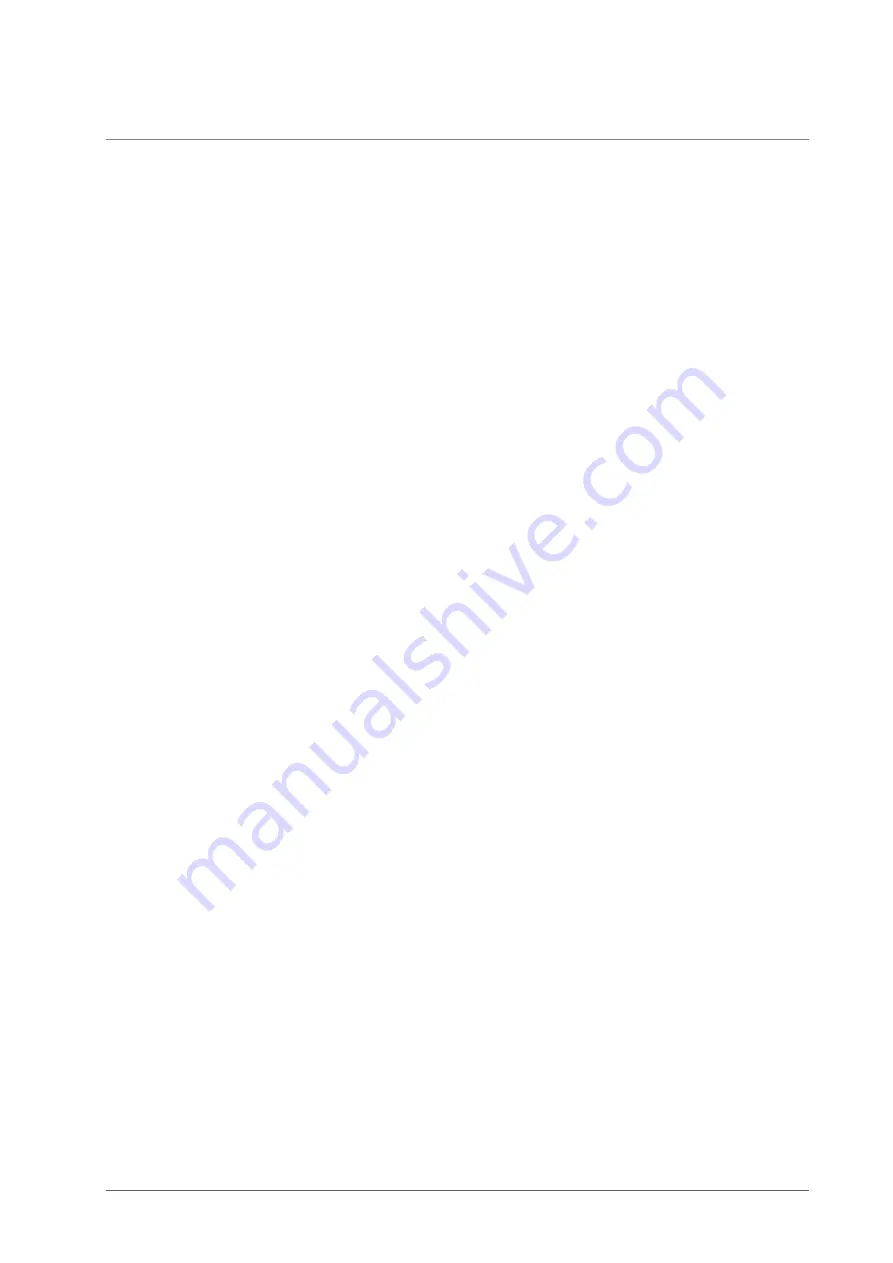
Users’ Manual
EDI-53 Series Digital Indicator
Page
|
7
3
OPERATING PRINCIPLE
3.1
Transducers
A transducer is basically a device that converts a measured variation in any physical parameter to a
corresponding variation in an electrical parameter like voltage, current or resistance.
The EDI-53 series of indicators are available in three versions, EDI-53P for potentiometric displacement
transducers, EDI-53L for resistance strain gage bridge-based load cells, and EDI-53I for 4 to 20 mA DC
current loop transducers.
The EDI-53P accepts inputs from Encardio-rite series of potentiometric displacement transducers type
EDE-PXX. The EDE-PXX series of displacement transducers have a displacement measurement range
from 0…50 mm to 0… 250 mm and provide 0…2 V DC output proportional to measured displacement.
These displacement transducers also need a 5 to 12 V DC excitation supply voltage. EDI-53P provides a
5 V DC excitation supply for the transducers. The EDI-53P can also be used with potentiometric
transducers for geo-technical applications from some other manufacturers as well.
The EDI-53L accepts input from resistance bridge foil strain gage load cells. These load cells basically
consist of four resistance strain gages connected as a bridge. They require an excitation voltage and
their output is specified as between 1mV per Volt to 3 mV per Volt of excitation voltage at full rated load
(i.e. load cell capacity). The output of these load cells is in the form of a voltage signal and is directly
proportional to the applied load and the excitation voltage. The magnitude of the voltage signal is very
small and special shielding precautions have to be taken to keep the output signal free of induced noise.
Resistance strain gage bridge load cells can normally provide higher accuracies than possible with
vibrating wire load cells but are more susceptible to damage from overloading and impact load than
vibrating wire load cells.
Resistance strain gage-based load cells are commonly used for monitoring load on anchor bolts, struts,
roof support, and cable tension, etc.
The EDI-53L provides an excitation voltage of 5 V DC. It can be programmed to accept input from load
cells with a rated output between 1 mV/V to 3 mV/V.
The EDI-53I is for use with transducers that provide a 4-20 mA DC current loop output proportional to the
measured input physical parameter. Although this type of transducers are widely used in the process
control industry, their use in geo-technical applications is fairly limited. Current loop output is generally
not used with vibrating wire sensors so their use is limited to other type of sensors based on resistance
strain gauges, potentiometers and inductive coils.
Current loop output transducers need a two conductor twisted pair cable and the signal can be
transmitted over fairly long distances without much degradation in signal. The same pair of conductors is
used to carry both the supply voltage as well as the output signal saving on cable costs. Current loop
output transducers are generally known as two wire transmitters in the process industry.
Current loop output transducers always require a supply voltage, generally between 12 to 24 V DC. The
EDI-53I does not provide any power supply for the current loop transducers, so an external power supply
will have to be used to power the sensors. When a number of current loop output transducers are used at
a particular location, a single power supply with suitable output voltage and current rating can be used to
power all the transducers.
3.2
Measurement of transducer output
The EDI-53 digital indicator converts the input voltage and current to a proportional 0…
±
2 V DC signal
and measure this voltage with the help of an Analogue to Digital Converter, generally referred to as ADC.
The ADC has a measurement resolution of 20,000 divisions or counts, so the ADC can measure the 2V