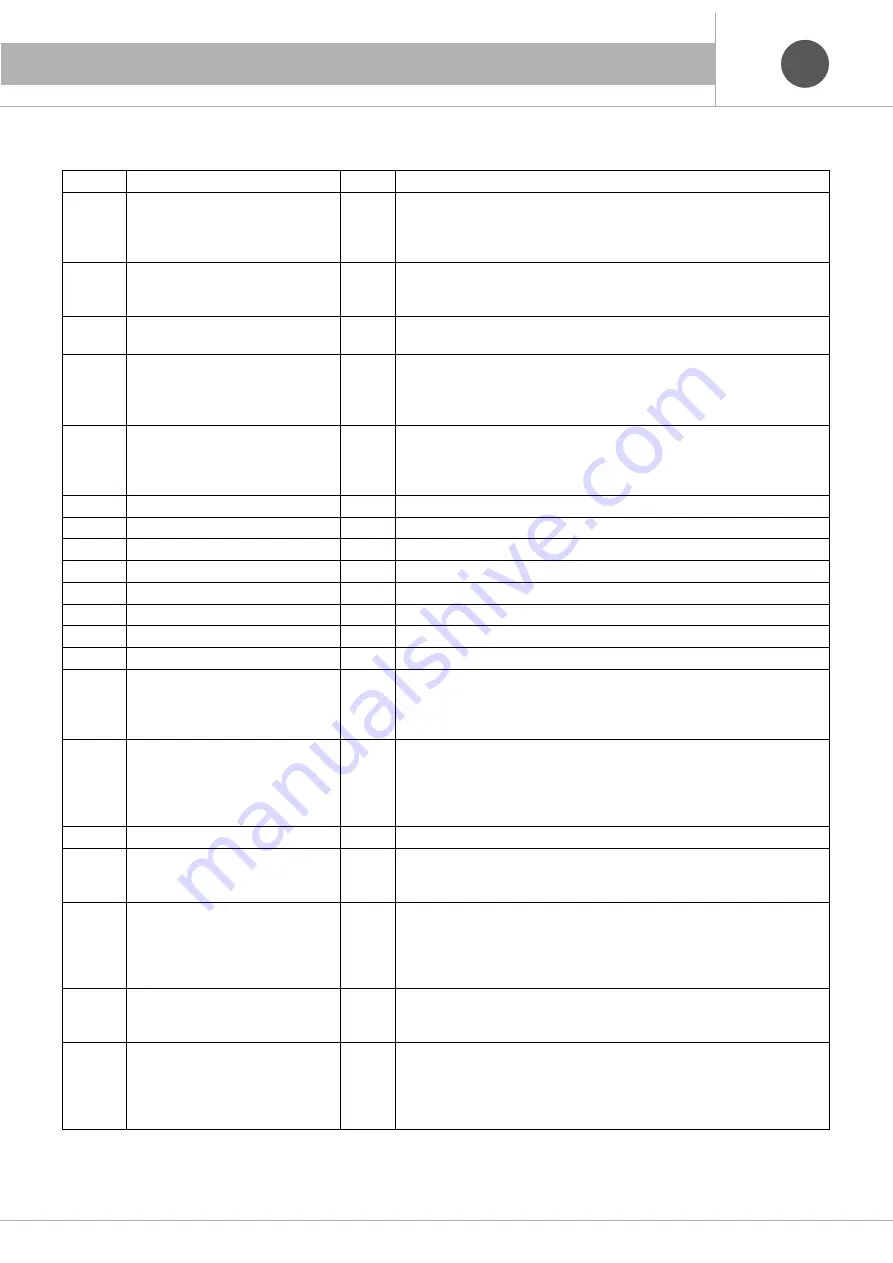
47
1. DESCRIZIONE DEI COMPONENTI
IT
IT
N°
Type of anomaly
Display Possible causes
1
High pressure protection
E1
1. Too much coolant.
2. Poor heat exchange (exchanger dirty or poor air circulation).
3. Ambient temperature too high.
2
indoor unit ice protection
E2
1. Poor heat exchange (exchanger dirty or poor air circulation).
2. indoor unit fan motor damaged.
3
Low pressure protection
E3
1. Not enough coolant;
2. Loss of coolant.
4
Compressor discharge high temperature
protection
E4
1. Too much coolant.
2. Ambient temperature too high.
3. Poor heat exchange (exchanger dirty or poor air circulation).
5
Overload protection
E5
1. Supply voltage unstable.
2. Supply voltage low.
3. Too much coolant.
4. Ambient temperature too high.
5. Poor heat exchange (exchanger dirty or poor air circulation).
6
Communication error
E6
1. Communication cable between indoor and outdoor units not connected correctly.
2. Control wire not connected correctly (if installed).
7
Operating mode in conflict
E7
The operating mode of the indoor unit is in conflict with the operation of the outdoor
unit.
8
Capacitor coil overheating protection
E8
1. Too much coolant;
2. Poor heat exchange (exchanger dirty or poor air circulation);
3. Ambient temperature too high.
9
EEPROM anomaly
EE
Outdoor unit AP1 electronic board damaged.
10
Reduced frequency for overcurrent of the
IPM module
En
1. Check the thermal insulation of the IPM module and the radiator (the unit must be
off for at least 20 minutes);
2. Outdoor unit electronic board damaged.
11
Reduced frequency for overtemperature
of the IPM module
EU
1. Check the thermal insulation of the IPM module and the radiator (the unit must be
off for at least 20 minutes);
2.
2. Outdoor unit AP1 electronic board damaged.
12
Bridge anomaly
C5
The bridge on the electronic board of the indoor unit is not inserted correctly.
13
Coolant recovery
F0
The outdoor unit has received the signal to start the "Coolant recovery"
14
Indoor unit ambient temperature sensor
anomaly
F1
1. Loosening or bad contact of the temperature sensor with the electronic board.
2. Temperature sensor damaged.
3. Indoor unit electronic board damaged.
15
Indoor unit evaporator temperature
sensor anomaly
F2
1. Loosening or bad contact of the temperature sensor with the electronic board.
2. Temperature sensor damaged.
3. Indoor unit electronic board damaged.
4. The temperature sensor head has not been inserted inside the copper pipe.
16
Outdoor unit ambient temperature sensor
anomaly
F3
1. Loosening or bad contact of the temperature sensor with the electronic board.
2. Temperature sensor damaged.
3. Outdoor unit electronic board damaged.
17
Outdoor unit capacitor temperature
sensor anomaly
F4
1. Loosening or bad contact of the temperature sensor with the electronic board.
2. Temperature sensor damaged.
3. Outdoor unit electronic board damaged.
4. The temperature sensor head has not been inserted inside the copper pipe.
18
Outdoor unit discharge temperature
sensor anomaly
F5
1. Loosening or bad contact of the temperature sensor with the electronic board.
2. Temperature sensor damaged.
3. Outdoor unit electronic board damaged.
4. The temperature sensor head has not been inserted inside the copper pipe.
19
Reduced frequency for overheating of the
condensing coil
F6
1. Supply voltage low.
2. Too much coolant.
3. Ambient temperature too high.
4. Poor heat exchange (exchanger dirty or poor air circulation).
GB
GB
N°
Type of anomaly
Display Possible causes
20
Reduced frequency for overcurrent
F8
1. Supply voltage low.
2. Too much coolant.
3. Ambient temperature too high.
4. Poor heat exchange (exchanger dirty or poor air circulation).
21
Reduced frequency for overtemperature
of exhaust air.
F9
1. Ambient temperature too high;
2. Not enough coolant;
3. Malfunction of the electronic expansion valve.
22
Reduced frequency for indoor unit ice
protection
FH
1. Poor heat exchange (exchanger dirty or poor air circulation).
2. Indoor unit fan speed too low;
23
Voltage too high for the electronic board
PH
1. Voltage between L and N on the terminal board over 265 VAC;
2. Wiring loose (the unit must be off for at least 20 minutes before checking the
wiring);
3. Electronic board damaged.
24
Voltage too low for the electronic board
PL
1. Voltage between L and N on the terminal board below 150 VAC;
2. Wiring loose (the unit must be off for at least 20 minutes before checking the
wiring);
3. Electronic board damaged.
25
Fixed frequency test
P0
Displayed during the P0 fixed frequency test.
26
Fixed frequency test
P1
Displayed during the P1 fixed frequency test.
27
Fixed frequency test
P2
Displayed during the P2 fixed frequency test.
28
Fixed frequency test
P3
Displayed during the P3 fixed frequency test.
29
Fixed frequency test
P4
Displayed during the P4 fixed frequency test.
30
Fixed frequency test
P5
Displayed during the P5 fixed frequency test.
31
Fixed frequency test
P6
Displayed during the P6 fixed frequency test.
32
Fixed frequency test
P7
Displayed during the P7 fixed frequency test.
33
IPM module high temperature protection
P8
1. Check the thermal insulation of the IPM module and the radiator (the unit must be
off for at least 20 minutes);
2.
2. Outdoor unit AP1 electronic board damaged.
34
Capacitor charging anomaly
PU
1. Voltage between L and N on the terminal board different from 210 ÷ 250 VAC
2. Wiring loose or cut (the unit must be off for at least 20 minutes before checking the
wiring);
3. Capacitor damaged
4. Outdoor unit AP1 electronic board damaged.
35
Defrosting
H1
Normal operation during the heating mode.
36
Ionizer protection
H2
1. Ionizer wiring loose or cut;
2. Ionizer damaged;
3. Indoor unit electronic board damaged.
37
Compressor overload protection
H3
1. Compressor wiring loose or cut (in normal operating conditions the resistance for
this terminal should be less than 1 ohm);
2. Too much or not enough coolant.
3. Obstruction in the cooling circuit;
4. Malfunction of the compressor.
38
Anomaly in the system
H4
1. Condensing temperature too high;
2. Ambient temperature too high;
3. Poor heat exchange (exchanger dirty or poor air circulation).
39
IPM module protection
H5
1. Voltage between L and N on the terminal board different from 210 ÷ 250 VAC;
2. Compressor wiring loose or cut;
3. Compressor damaged;
4. Too much or not enough coolant;
5. High load or insufficient heat transfer.
9. MALFUNCTION