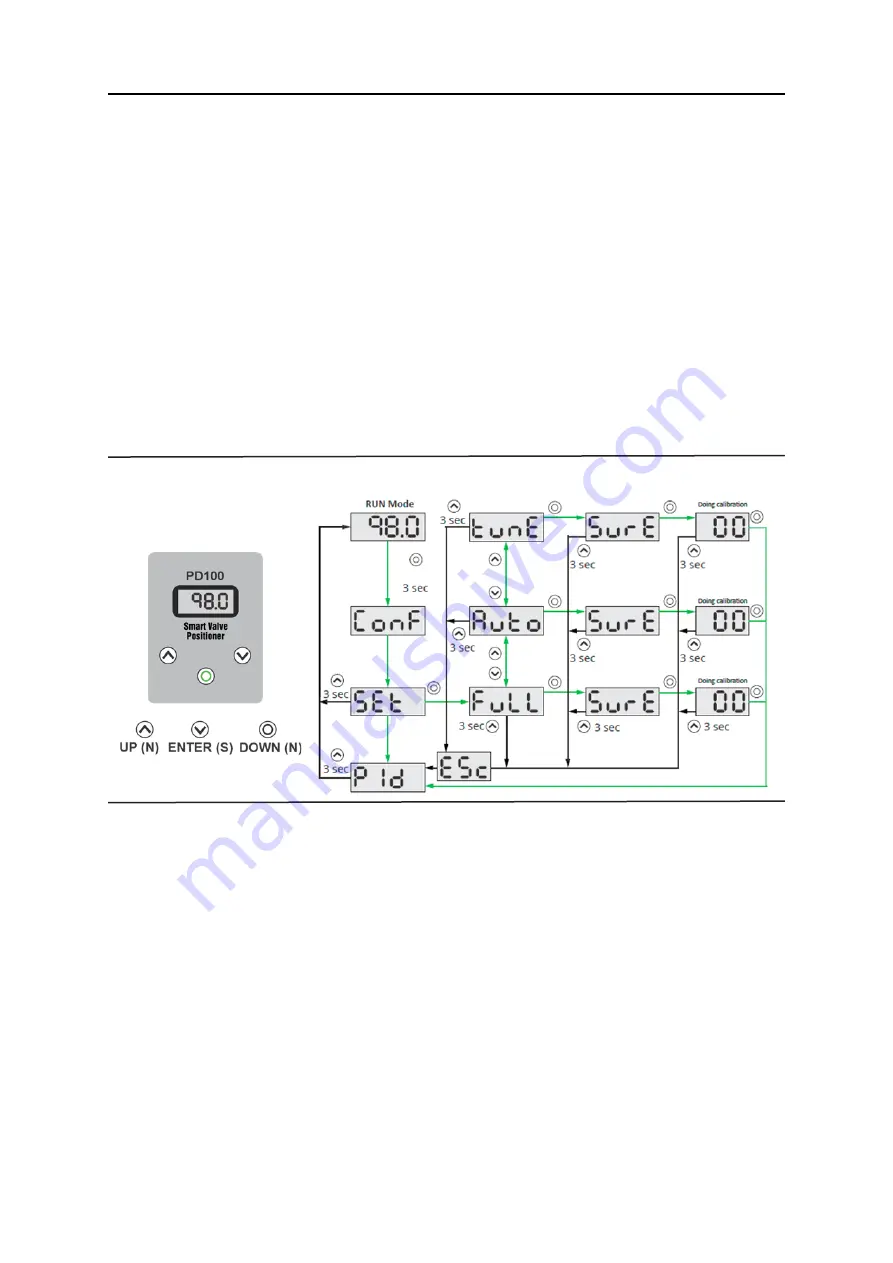
Configuration
34
Installation, Operation, and Maintenance Manual
ES-09373-1
Configuration
August 17, 2022
8.4
Configuration Menu (Continued)
8.4.1
Setup Menu
In this function you can perform the 3 modes of positioner calibration:
1 - FULL: Recognizes the open and closed points and adjusts the best parameters for
the PID.
Note: Recommended use for the first calibration.
2 - AUTO: Learns the open and closed points (0% and 100%).
Note: Recommended use in a process change or after maintenance.
3 - TUNE: Automatically calculates the PID parameters (Kp, Tr and Td).
NOTE: Recommended use in a process changeover.
Accessing the Setup Menu
•
Press the ENTER button for 3 seconds to enter the menu.
•
The first option is the SET menu.
•
Use the ENTER button to select this function.
•
Use the UP or DOWN buttons to navigate to the item you wish to set.
•
Use the ENTER button for the calibration procedure you want to perform.
•
To continue with the selected calibration procedure, confirm with the ENTER
button.
•
If you want to exit without performing the calibration, use the UP button for 3
seconds and return to the main menu.
NOTE: You can exit the calibration process at any time by pressing the UP button for 3
seconds. The message ESC will appear in the display.
Figure 8-7 Setup Menu