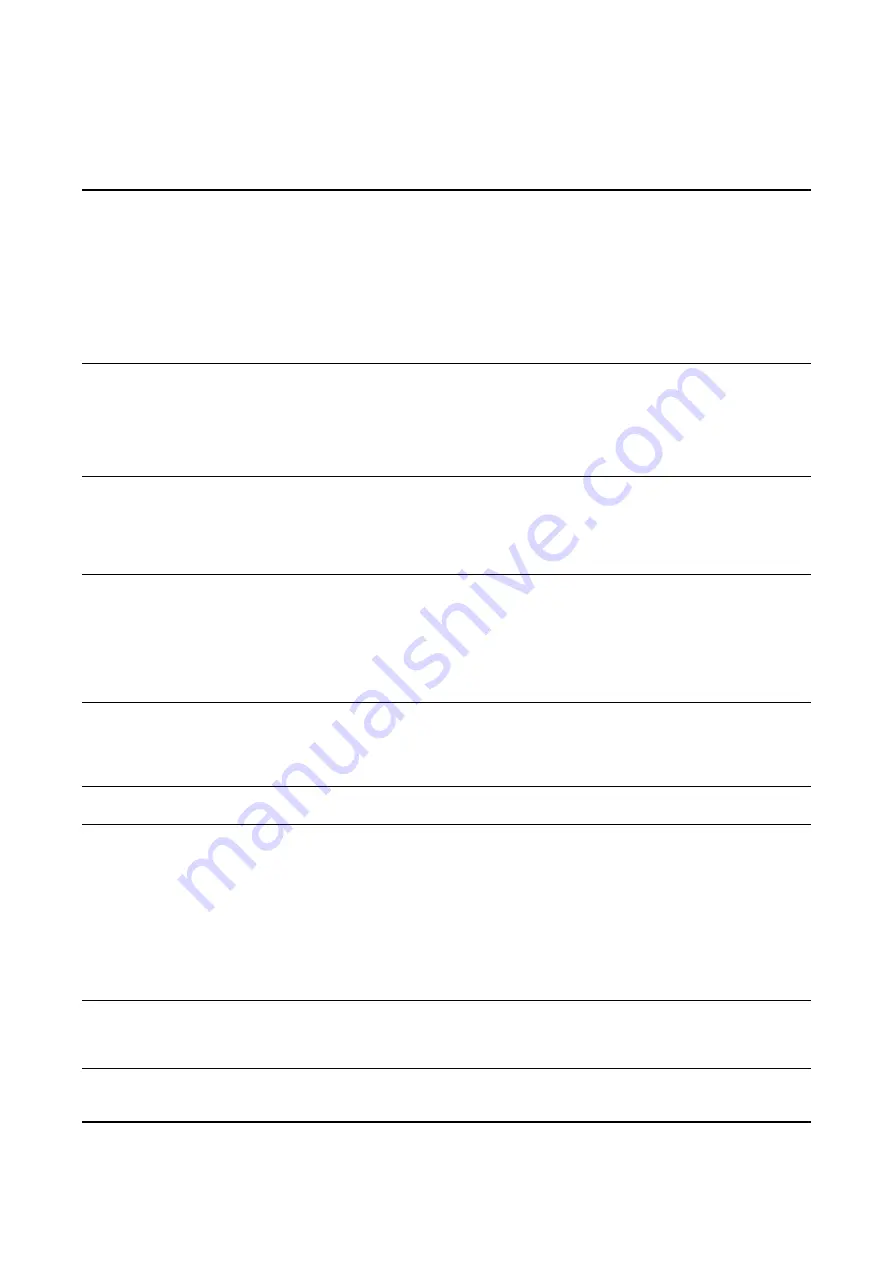
106
Micro Motion
®
Model 3711 Gas Flow Computers
PID Control Loops
10.5
Monitoring the PID control loop
The
PID Loop
window can be used to monitor the PID control loop. Fields that show current PID
information are listed and defined in Table 10-2.
Scale Factor
Ratio of control output span to process variable input span. The
sign of the number specifies the action of the loop:
• Negative = reverse action
• Positive = direct action
For example, if the analog output span is 100, and the input
process variable is read from the pulse input, which has a span
of 200, enter a value of –2 or +2.
• Reverse action: Negative
feedback loop: i.e., the control
loop produces a decrease in
output when the assigned
process variable exceeds the
setpoint.
• Direct action: Positive feedback
loop: i.e., the control loop
produces an increase in output
when the assigned process
variable exceeds the setpoint.
Integral
Deadband
Specifies a “no action range” around the setpoint. As long as
the process variable value is within this range, the PID control
loop does not perform any adjustments.
Enter the value in the EU used to specify the setpoint.
The “no action range” is
determined by:
• Lower end: subtracting the
integral deadband value from the
setpoint
• Higher end: adding the integral
deadband value to the setpoint
SP Ramp Rate
Maximum rate, in EUs per minute, at which the setpoint used by
the PID algorithm is allowed to ramp to a new value, when the
setpoint is reconfigured manually. Enter the value in the EU
used to specify the setpoint.
Applies to both the primary loop
and the override loop.
To disable SP ramp rate control,
enter a value of 0.0. In this case,
the new setpoint value will be used
in the next calculation.
Manual Tracking
• Enabled: The primary loop setpoint is set equal to the current
value of the primary loop process variable when the PID
control loop is in manual mode.
• Disabled: The primary loop setpoint is not modified when the
control loop is in manual mode.
Applies to the primary loop only.
Typically used to eliminate a
“bump” when changing from
manual to automatic mode.
The original setpoint is not
retained. To return to the original
operating value, the operator must
reconfigure the setpoint manually.
Halt PID on Reset
• Enabled: PID control is disabled when the Model 3711 is reset
or restarted.
• Disabled: PID control may or may not be active when the
Model 3711 is reset, depending on the setting of the Mode
parameter.
Override Type
Select
Controls how the override loop interacts with the primary loop.
See Section 10.2 and Section 10.3, Step 11.
Applies only if Override Control is
configured.
Table 10-2
PID loop monitoring parameters
Parameter
Description
Comments
Status
• Disabled: Scanning is set to Disabled.
• Primary: The primary loop is currently controlling the process.
• Override: The override loop is currently controlling the
process.
Actual Period
Displays the time elapsed between the beginning of the
previous execution of the PID algorithm and the beginning of
the current execution.
Will never be less than the value
configured for Loop period.
Table 10-1
PID loop tuning parameters
continued
Parameter
Description
Comments
Содержание Micro Motion 3711
Страница 32: ...24 Micro Motion Model 3711 Gas Flow Computers ...
Страница 44: ...36 Micro Motion Model 3711 Gas Flow Computers ...
Страница 56: ...48 Micro Motion Model 3711 Gas Flow Computers ...
Страница 68: ...60 Micro Motion Model 3711 Gas Flow Computers ...
Страница 92: ...84 Micro Motion Model 3711 Gas Flow Computers ...
Страница 108: ...100 Micro Motion Model 3711 Gas Flow Computers ...
Страница 140: ...132 Micro Motion Model 3711 Gas Flow Computers ...
Страница 196: ...188 Micro Motion Model 3711 Gas Flow Computers ...
Страница 210: ...202 Micro Motion Model 3711 Gas Flow Computers ...
Страница 233: ......