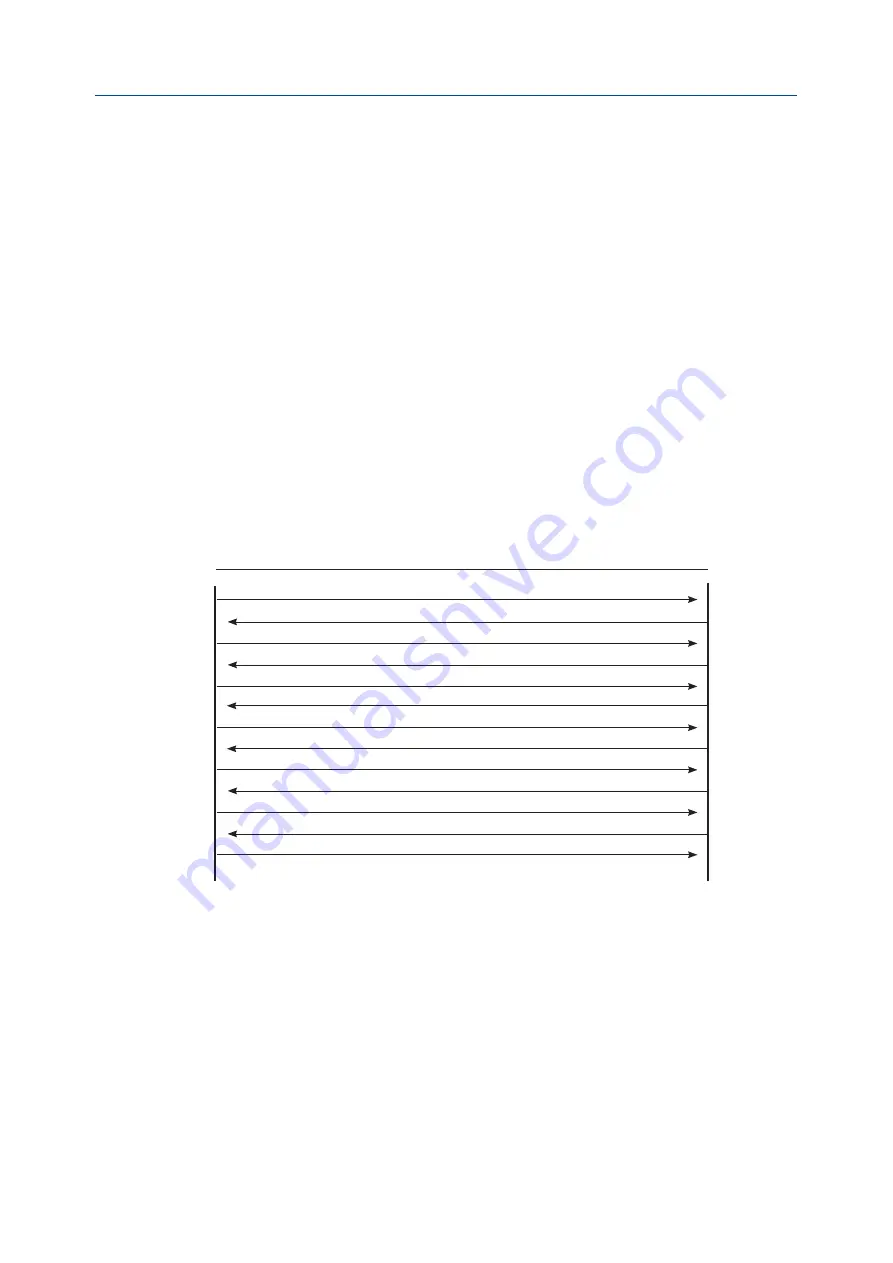
11.1.3
Positioning Algorithm
A positioning algorithm (position closed loop control) is implemented on the EPI2 DPV1
interface card. Positioning function compares the position received from the base card
with the position request received from the bus. If the difference between “position
request and present position” is greater than the “dead band”, an open or a close
command is sent to the base card. Dead band is configurable via bus from 0.3 to 2.0%.
11.1.4
Diagnostic Message
The EPI2 DPV1 interface manages the diagnostic indication coming from the actuator as
stated by the Profibus DPV1 standard. When the EPI2 DPV1 interface needs to notify a fault
to the master while in data exchange mode, it changes the function code in its response
message to “high priority”. During the next regular bus cycle, the master, in turn, sends
a “Slave_Diag” request that is answered with a “Slave_Diag” response. The availability of
specific diagnosis information is notified by Dia.Ext_Diag flag set to 1. Once the master
was able to catch the diagnosis information, it returns to the standard cyclic data exchange
mode. To notify the termination of the diagnosis incident, the EPI2_DPV1 interface send a
“high priority” response. The master answers with a “Slave_Diag” request that is followed
by a “Slave_Diag” response with Dia.Ext_Diag flag set to 0.
MASTER
EPI 2_DPV1
Data exchange request
Data exchange response
Data exchange request
Data exchange response
(Function code = high priority)
Slave_Diag request
Slave-Diag response (Diag Ext-Diag = 1)
Data exchange request
Data exchange response
Data exchange request
Data exchange response (Function code = high priority)
Slave_Diag request
Slave_Diag response (Diag.Ext_Diag = 0)
Data exchange request
Data exchange response
Fault on
Fault off
Installation, Operation and Maintenance Manual
VCIOM-01493-EN Rev. 0
May 2022
31
Section 11: Data Exchange Mode
Data Exchange Mode