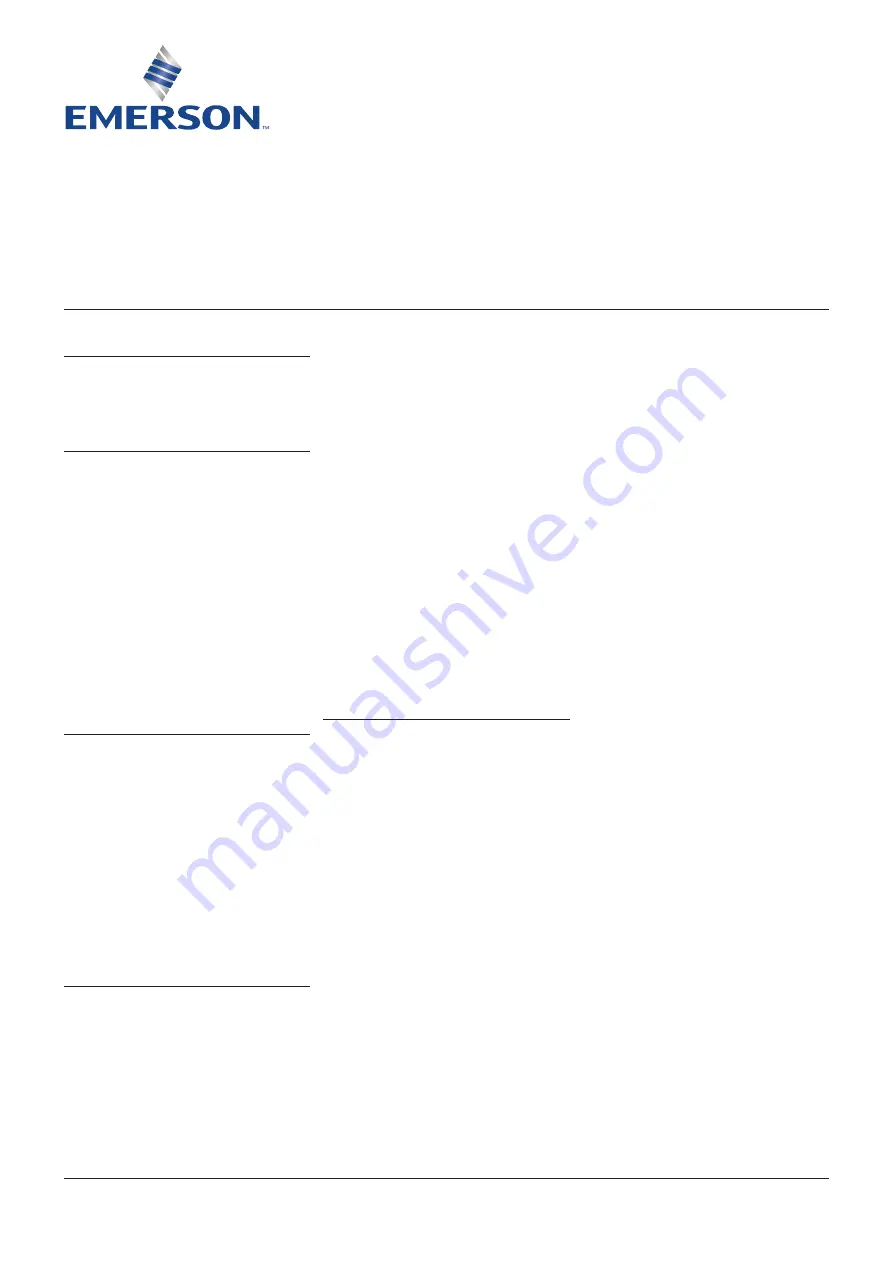
© 2017 Emerson. All Rights Reserved.
Emerson.com/FinalControl
KEYSTONE
FIGURE 634/637 AND 638 SLURRY VALVES
INSTALLATION AND COMMISSION ING INSTRUCTIONS
Complete installation and commisioning for:
F634 (light duty slurry valves), F637 (medium duty slurry valves) and F638 (heavy duty slurry valves)
VCIOM-02445-EN 15/08
INSTALLATION INSTRUCTIONS
1. Ensure that the flanges are clean,
undamaged and compatible with the valve.
2. Spread the flanges to allow sufficient
clearance for the valve and gaskets.
DO NOT USE THE VALVE AS A CROWBAR.
3. Loosely fit two bolts at the bottom of the
flanges to bear the weight of the valve.
Note:
F638 300 - 600 mm use short flange
bolts, for F634, F637 and F638 40 - 250 mm
use thru bolts.
GENERAL
The F634 and F637 are bi-directional valves and
will control flow in either direction.
The F638 40 - 300 mm is a uni-directional valve
and will only control flow in one direction.
The F638 350 - 600 mm is a bi-directional valve
and will control flow in either direction.
In most horizontal pipe installations it is
recommended that the valve be installed with
its shaft horizontal and the lower disc edge
opening downstream, particularly on slurry
or sedimentary duties. Flange gaskets are
required to ensure effective sealing. Check that
the gasket material is suitable for the service.
SAFETY PRECAUTIONS
For safety reasons, it is important to take the
following precautions before working on the
valve.
1. Ensure that the procedures below meet or
agree with the site procedures, if not review
with your site safety officers.
2. Personnel making any adjustments to
the valve arrangement should utilize all
necessary equipment and clothing normally
used to work with the process where the
valve is installed.
3. The line must be depressurized, drained and
vented before installing or maintenance on
the valve.
4. Handling and installation of all valves,
operators and actuators must be carried
out by personnel trained in all aspects
of installation and manual/mechanical
handling techniques using site occupational
health and safety procedures.
STORAGE INSTRUCTIONS
The valve faces should be adequately protected
against damage and coated with corrosion
inhibitor even when stored under cover.
FLANGE AND PIPE COMPATIBILITY
Emerson valves are suitable for installation into
most piping systems.
The standard end connections are:
F638 - Flanged ASME Class 150, 300, 600
F634, F637 - Flanged ASME Class 150
Refer valve literature sheet for standard
drillings.
Weld neck flanges (flange ID approximates
valve bore) are recommended to ensure
maximum valve performance. However slip on
flanges may be used.
NOTE
These valves are not recommended for dead
end service.
4. For F638 40 - 300 mm check that the flow
arrow on the side of the valve agrees with
the direction of flow. (Longest end of the
valve must face downstream).
5. Insert the valve between the flanges with
gaskets either side.
6. Loosely fit the remainder of the flange
bolts.
7. Center the valve and ensure the gaskets
are properly positioned.
8. Hand tighten all the flange bolts.
9. Open the valve fully and check that the
valve cycles correctly. (The disc is in line
with the parallel flats or keyway in the
stem).
10. Cross tighten all the flange bolts.
(See flange diagram for tightening
sequence and bolt torque table for
torques).
11. After the pipeline is pressurized, check
for flange leaks and adjust the gland as
necessary.
5. Ensure the valve pressure/temperature
limitations marked on the name plate
comply with the service application.
6. When used for line fluids with a temperature
of 80°C or higher, the valve body can
become very hot and should not be handled
without appropriate protection.
7. Do not weld near the valve, as this will result
in serious damage to the valve.