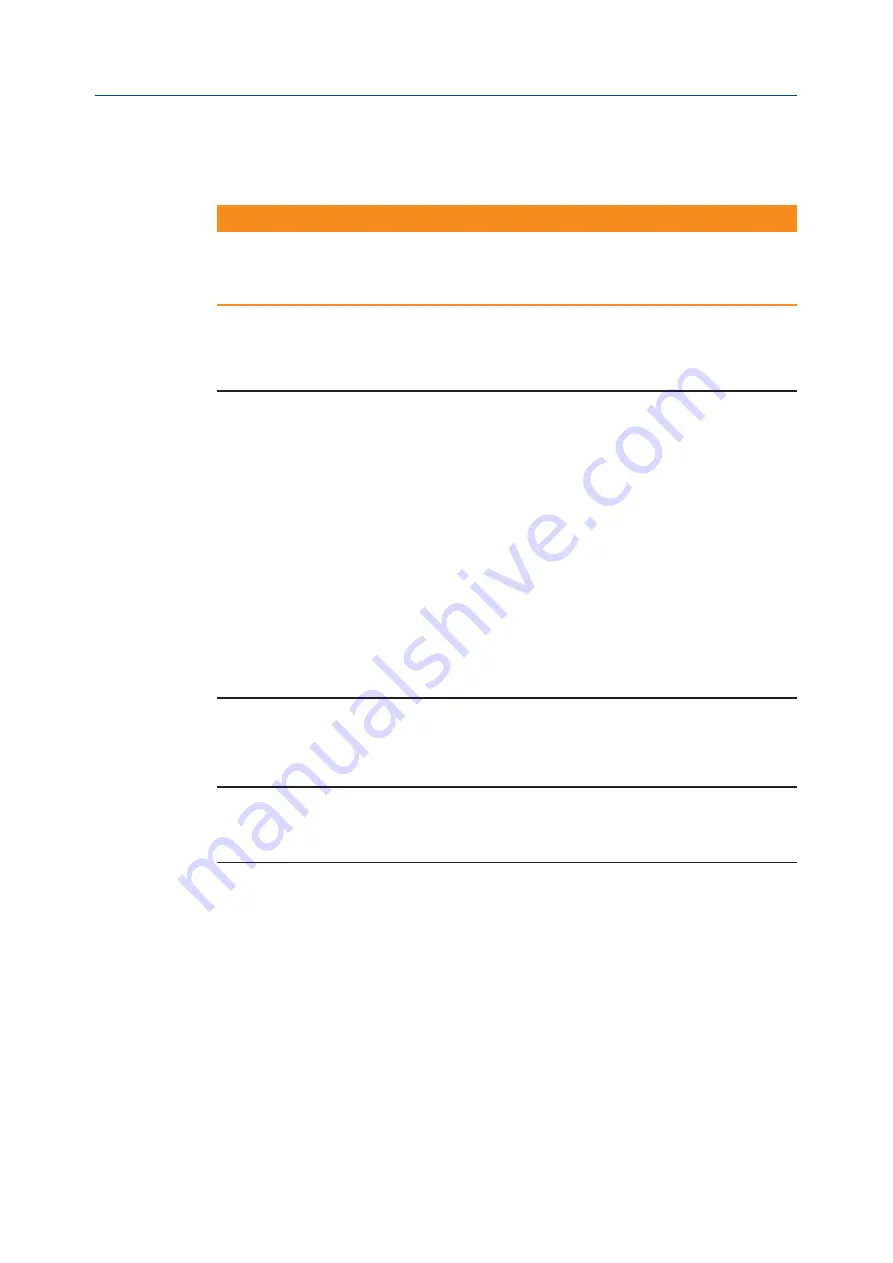
Installation, Operation and Maintenance Manual
MAN-10-04-100-0711-EN Rev. 0
October 2020
29
Actuator Configuration
Section 6: Actuator Configuration
6.2
Local Configuration of the Keystone EPI2
!
WARNING
The configuration must be done while the actuator is powered on. As a consequence,
all configuration operations must be carried out by specifically qualified personnel for
operations on powered electronic cards.
6.2.1
Keystone EPI2 Default General Configuration
NOTE
The actuators are set in the workshop with the following configuration (default value):
•
CL limit switch by position
•
OP limit switch by position
•
Stroking time in CL (6): 28 s for models 063/125/250/500, 45 s for model 1000 and
100 s for model 2000
•
Stroking time in OP (6): 28 s for models 063/125/250/500, 45 s for model 1000 and
100 s for model 2000
•
Torque limiting device in CL set at about 100% of nominal torque
•
Torque limiting device in OP set at about 100% of nominal torque
•
Reverse mode off
•
Monitor Relay NC (in normal condition, i.e. without alarms)
•
Blinker / Local Selector relay off (always Open)
If the application requires different actuator configurations, please proceed as described
in this chapter.
NOTE
Please note that the actuator configuration does not need to be done in succession as
indicated in the following pages. Each parameter can be set independently.
The configuration of the actuator parameters is done through the following tools:
•
Two rotary selector switches SW6 and SW4 for actuator configuration
•
Enter pushbutton SW5 (confirmation pushbutton)
•
Dip switch SW3 (enable configuration function)
•
Green LED indicating power ON (switched on when power supply is available)
•
Red LED for Enter confirmation (ON onceconfiguration is confirmed)
•
Mechanical stops