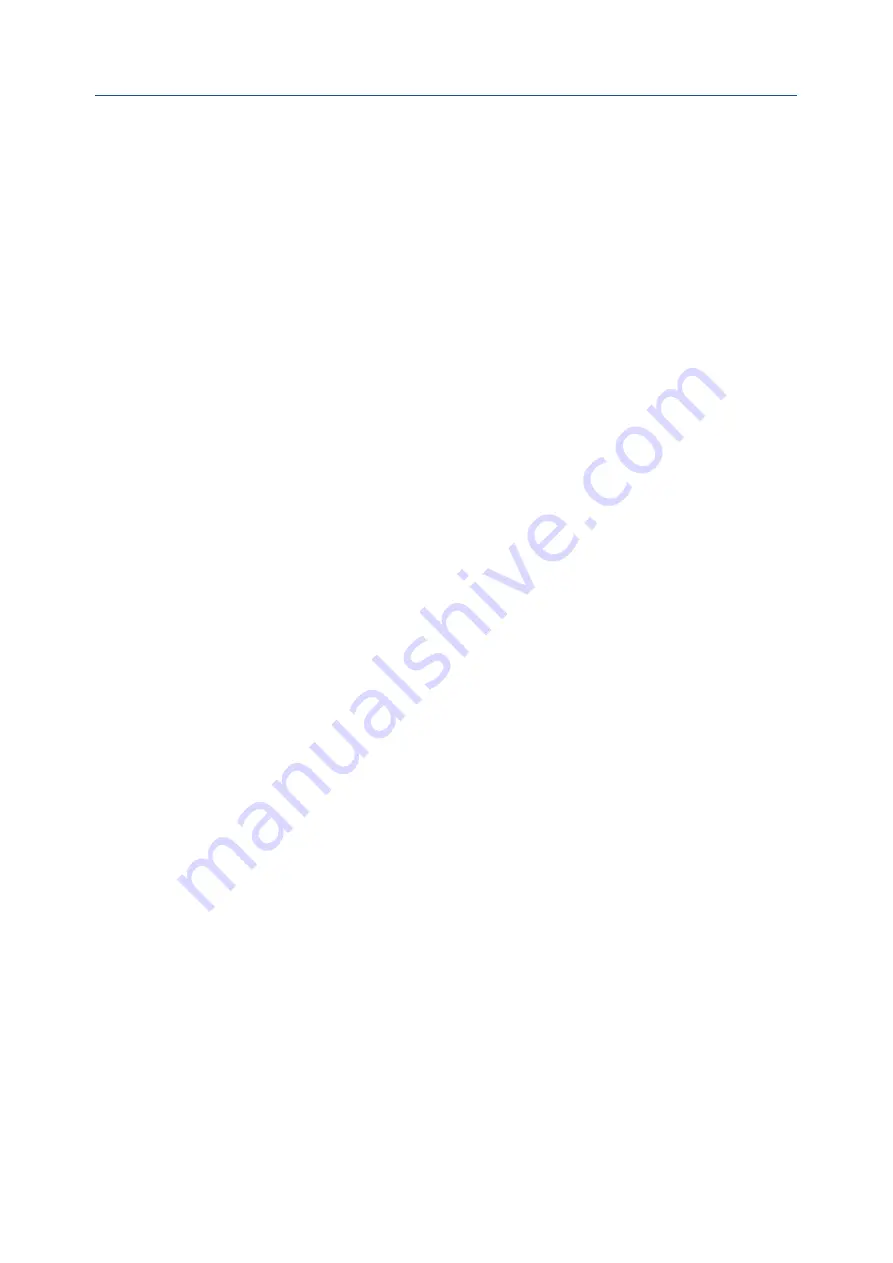
November 2022
Installation, Operation and Maintenance Manual
MAC050515 EN Rev. 0
ATEX Instructions in Explosive Areas
3
Section 2: ATEX Instructions in Explosive Areas
Section 2: ATEX Instructions for Use in
(Potential) Explosive Areas
2.1
Intended Use
The Hytork XL series pneumatic actuators are a Group II category 2 equipment and
intended for use in areas in which explosive atmospheres caused by mixtures of air and
gases, vapours, mists or by air/dusts are likely to occur. Therefore, it may be used in (ATEX)
classified Zones 1, 2 (Gases) and/or 21, 22 (Dust).
2.2
Safety Instructions
1.
Actuator assembly, disassembly, and maintenance is allowed only in absence of
explosive mixture.
2.
Prevent entry of explosive mixtures into the actuator. We suggest utilizing a
solenoid with a “breather” function on Spring-Return actuators when used in
potentially explosive atmospheres.
3.
The plastic position indicator caps are approved for ATEX gas group IIB areas.
—
In areas where ATEX gas group IIC requirements apply, the plastic
indicator for actuator sizes XL26 to 281 is approved for use.
—
In areas where ATEX gas group IIC requirements apply, do not use the
plastic position indicator cap for actuator sizes XL426 up to XL4581, to
avoid build up of static electricity.
4.
In order to avoid increasing dust explosion risk, periodically clean dust deposits
from all equipment.
5.
When equipment is installed in a hazardous area location (potentially explosive
atmosphere), prevent sparks by proper tool selection and avoiding other types of
impact energy.
6.
Proper care must be taken to avoid generation of static electricity on the
non-conductive external surfaces of the equipment (e.g. rubbing of surfaces, etc.).
7.
Hytork XL actuators do not have an inherent ignition source due to electro-static
discharge, but explosion hazard may be present due to the discharge of static
electricity from other valve assembly components.
—
To avoid personal injury or property damage, make sure that the valve is
grounded to the pipeline before placing the valve assembly into service.
—
Use and maintain alternate shaft-to-valve body bonding, such as a
shaft-to-body bonding strap assembly.
8.
The paint protection must not exceed 200 μm if the actuator is used in a group
IIC atmosphere. For group IIA or IIB atmospheres, the paint protection must not
exceed a thickness of 2 mm (0.08 inch).