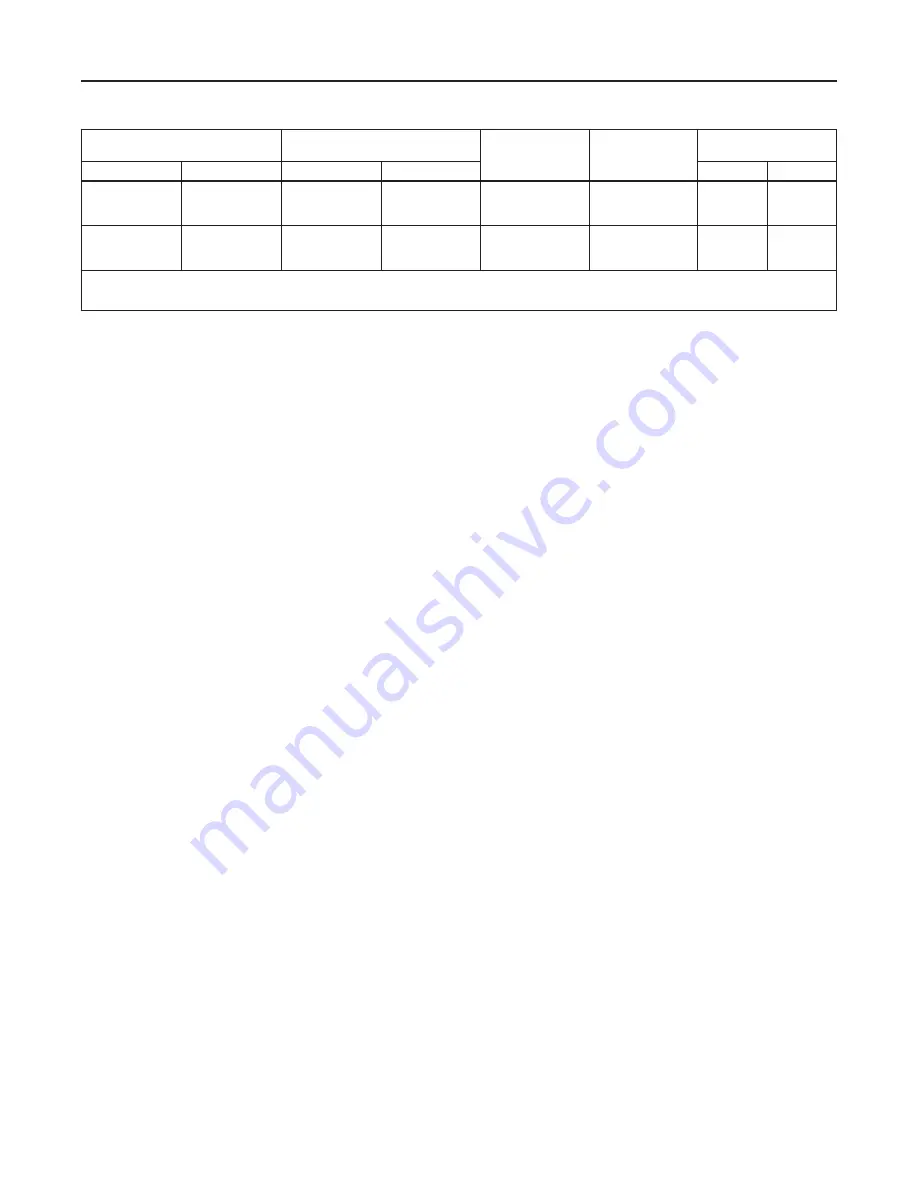
Body Area
These procedures are for gaining access to the disk
assembly, orifice, and body gasket. All pressure must
be released from the diaphragm case before the
following steps can be performed. Key numbers are
referenced in Figure 3.
1. To inspect and replace the disk holder assembly
(key 25), remove the body cap assembly (key 38).
2. If it is necessary to replace the disk holder
assembly (key 25), remove the machine screw
(key 47) and cotter pin (key 14) from the disk stem
(key 40).
3. To inspect and replace the orifice (key 27),
loosen the union nut (key 19), tip the diaphragm
casing (key 20) toward the inlet, and separate the
diaphragm casing from the body (key 28).
4. Remove and inspect the body gasket (key 16).
5. Inspect and replace the orifice (key 27) if necessary.
Lubricate the threads of the replacement orifice with
a good grade of pipe thread sealant and tighten
using 29 to 37 ft-lbs / 39 to 50 N•m of torque.
6. If necessary, install the replacement body gasket
(key 16) into the body (key 28).
7. Slide the union nut (key 19) as far as it will go
onto the diaphragm casing (key 20). Install both
halves of the split ring (key 17) into the slots of the
diaphragm casing (key 20) and secure them by
sliding the union nut down on the split ring.
8. Install the diaphragm casing (key 20) by tightening
the union nut (key 19) until the diaphragm case is
secure on the body (key 28).
9. The disk holder assembly (key 25) consists of the
disk and disk holder, as well as the valve disk washer
(key 46) and the machine screw (key 47). Install the
disk spring (key 41) and valve holder assembly and
secure it to the disk stem (key 40) with the cotter pin
(key 14).
10. Use a good quality thread sealer when replacing
the body cap assembly (key 38).
Diaphragm and Spring Case Area
These procedures are for gaining access to the
control spring, diaphragm assembly, valve stem, and
stem O-ring. All pressure must be released from the
diaphragm case before these steps can be performed.
Key numbers are referenced in Figure 3.
Type Y696VR Vacuum Regulator
1. Remove the closing cap (key 3) and turn the
adjusting nut (key 2) counterclockwise until all
compression is removed from the control spring
(key 1). If the only further maintenance is to
change the control spring (key 1), skip to step 10.
2. Remove the screws (key 21) and hex nuts (key 22)
and lift off the spring case assembly (key 23).
3. Remove the diaphragm (key 5) and attached
parts by tilting it so that the pusher post (key 8)
slips off the lever assembly (key 9). To separate
the diaphragm (key 5) from the attached parts,
unscrew the diaphragm hex nut (key 37). If
the only further maintenance is to replace the
diaphragm parts, skip to step 8.
4. To replace the lever assembly (key 9), remove the
machine screws (key 11).
5. To replace the valve stem (key 13) pull it out of the
diaphragm casing (key 20) and install a new valve
stem by pushing it into the diaphragm casing.
Table 2.
Vacuum Control Pressure Ranges and Spring Part Numbers
VACUUM CONTROL
PRESSURE RANGE
(1)
CHANGE IN VACUUM CONTROL
PRESSURE TO REACH WIDE-OPEN
SPRING
PART NUMBER
SPRING COLOR
SPRING
WIRE DIAMETER
In. w.c.
mbar
In. w.c.
mbar
In.
mm
1 to 3
(2)
1-1/2 to 5
(2)
3 to 8
(2)
2 to 7
(2)
4 to 12
(2)
7 to 20
(2)
1.5
2
3
4
5
7
1D892527022
1D7654000A2
0B0197000A2
Brown
Unpainted
Purple
0.109
0.120
0.148
2.8
3.1
3.8
8 to 16
16 to 32
0.25 to 3 psig
20 to 40
40 to 80
17 to 207
4
7
1.2 psig
10
17
83
1B766627062
1B883327022
1A630627022
Gray
Unpainted
Black
0.156
0.187
0.275
4.0
4.8
7.0
1. Pressure ranges are based on the spring case pointing up. Pointing the spring case down increases the pressure range 1.7 in. w.c. / 4 mbar.
Example: 1 to 3 in. w.c. / 2 to 7 mbar) changes to 2.7 to 4.7 in. w.c. / 7 to 12 mbar.
2. Do not use Fluorocarbon (FKM) diaphragm with these springs at diaphragm temperatures lower than 40°F / 4°C.
4
Y696VR Series