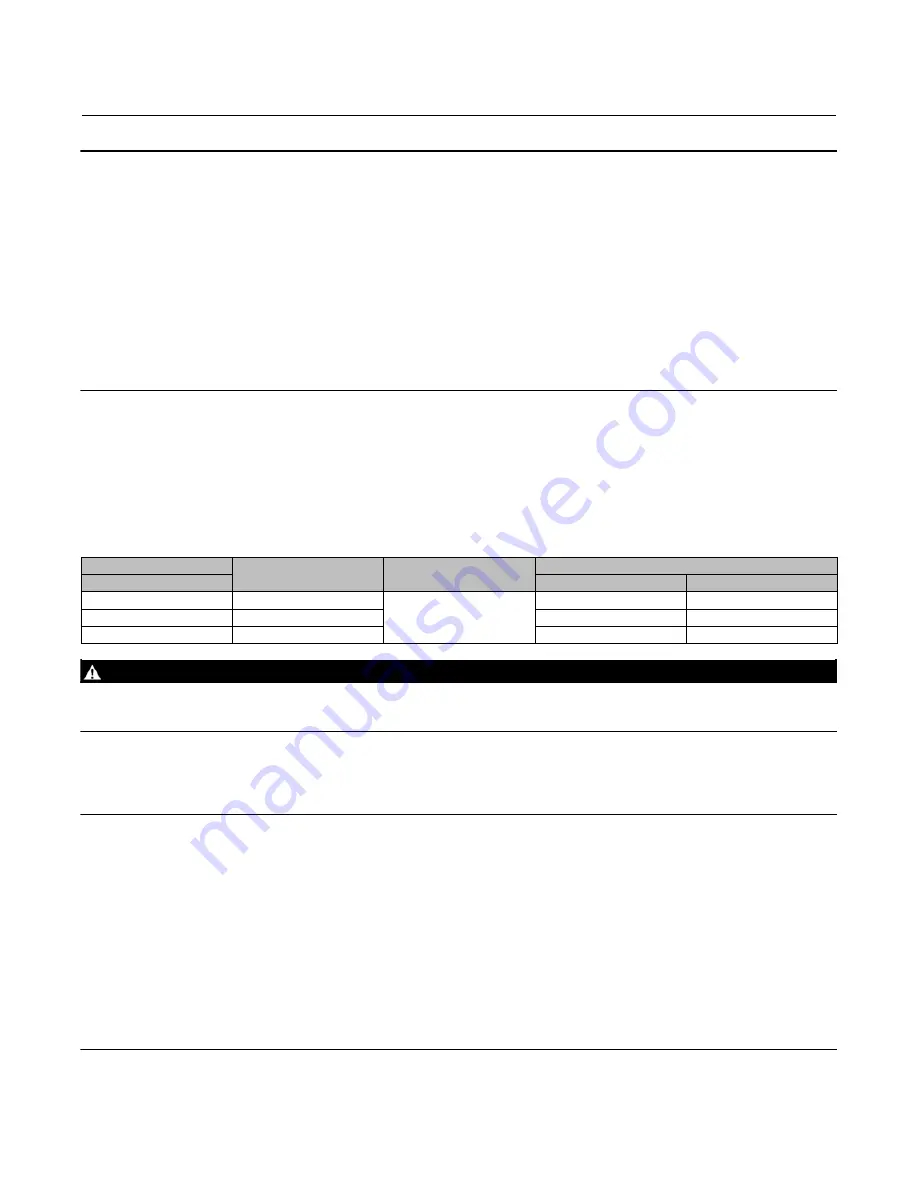
Instruction Manual
D103172X012
TBX Valve
May 2014
14
Note
Horizontal actuator only: TBX valves positioned in the process pipeline with a horizontal actuator/trim may require special
attention to ensure that the spiral wound gaskets are maintained in the proper location during the valve assembly procedures
without falling out of the gasket groove. Gasket manufacturer Flexitallic recommends spray adhesive 3M #77 Super Spray
Adhesive to temporarily hold gaskets in place until they are fully contained by the TBX valve body and trim components. It should
be noted that spiral wound gasket manufacturers other than Flexitallic may recommend different special gasket positioning
techniques. To use the adhesive with Flexitallic gaskets, lightly spray the gasket groove that the gasket will be installed in. Also
lightly spray one side of the spiral wound gasket that will be contacting the previously coated gasket groove. Let the spray
adhesive set for one minute and then lightly press the spiral wound gasket into the gasket groove.
Other Considerations: Ensure the spiral wound gasket is located in the correct location when contact is made. Trying to remove
the gasket after contact will damage the gasket by pulling out or removing the soft filler/facing material. If the gasket is incorrectly
positioned after applying the spray adhesive it must be removed and discarded. The gasket groove will then need to be cleaned
and a new gasket will need to be installed.
3. Lubricate the seat ring cap screws (key 76) and all surfaces that contact the screws, including the valve body and
seat ring.
4. Torque the cap screws in a crisscross pattern, using no more than 1/4 of the specified torque as indicated in table 5.
Repeat the crisscross pattern, working up to the specified torque in 1/4 increments until the final torque is
achieved. Wait a minimum of 1 minute to allow for gasket/screw relaxation and recheck the torque, adjusting as
necessary.
Table 5. TBX (Flow Up and Flow Down) Bolted Seat Ring Torque with Nickel Never-Seez Lubricant
CAP SCREW SIZE
THREADS PER INCH
LUBRICATION
RECOMMENDED BOLT TORQUE
Inch
N•m
lbf•ft
3/8
16
Nickel Never-Seez
41
30
1/2
13
91
67
5/8
11
163
120
WARNING
Different lubricants can produce different required torque values. Failure to calculate correct torque values for different
lubricants than recommended can lead to personal injury and equipment damage.
5. Install one cage gasket (key 43) into the groove in the valve body. If the valve has a horizontal stem orientation,
ensure that the gasket remains in the groove and does not get pinched during cage installation.
Note
Horizontal actuator only: TBX valves positioned in the process pipeline with a horizontal actuator/trim may require special
attention to ensure that the spiral wound gaskets are maintained in the proper location during the valve assembly procedures
without falling out of the gasket groove. Gasket manufacturer Flexitallic recommends spray adhesive 3M #77 Super Spray
Adhesive to temporarily hold gaskets in place until they are fully contained by the TBX valve body and trim components. It should
be noted that spiral wound gasket manufacturers other than Flexitallic may recommend different special gasket positioning
techniques. To use the adhesive with Flexitallic gaskets, lightly spray the gasket groove that the gasket will be installed in. Also
lightly spray one side of the spiral wound gasket that will be contacting the previously coated gasket groove. Let the spray
adhesive set for one minute and then lightly press the spiral wound gasket into the gasket groove.
Other Considerations: Ensure the spiral wound gasket is located in the correct location when contact is made. Trying to remove
the gasket after contact will damage the gasket by pulling out or removing the soft filler/facing material. If the gasket is incorrectly
positioned after applying the spray adhesive it must be removed and discarded. The gasket groove will then need to be cleaned
and a new gasket will need to be installed.