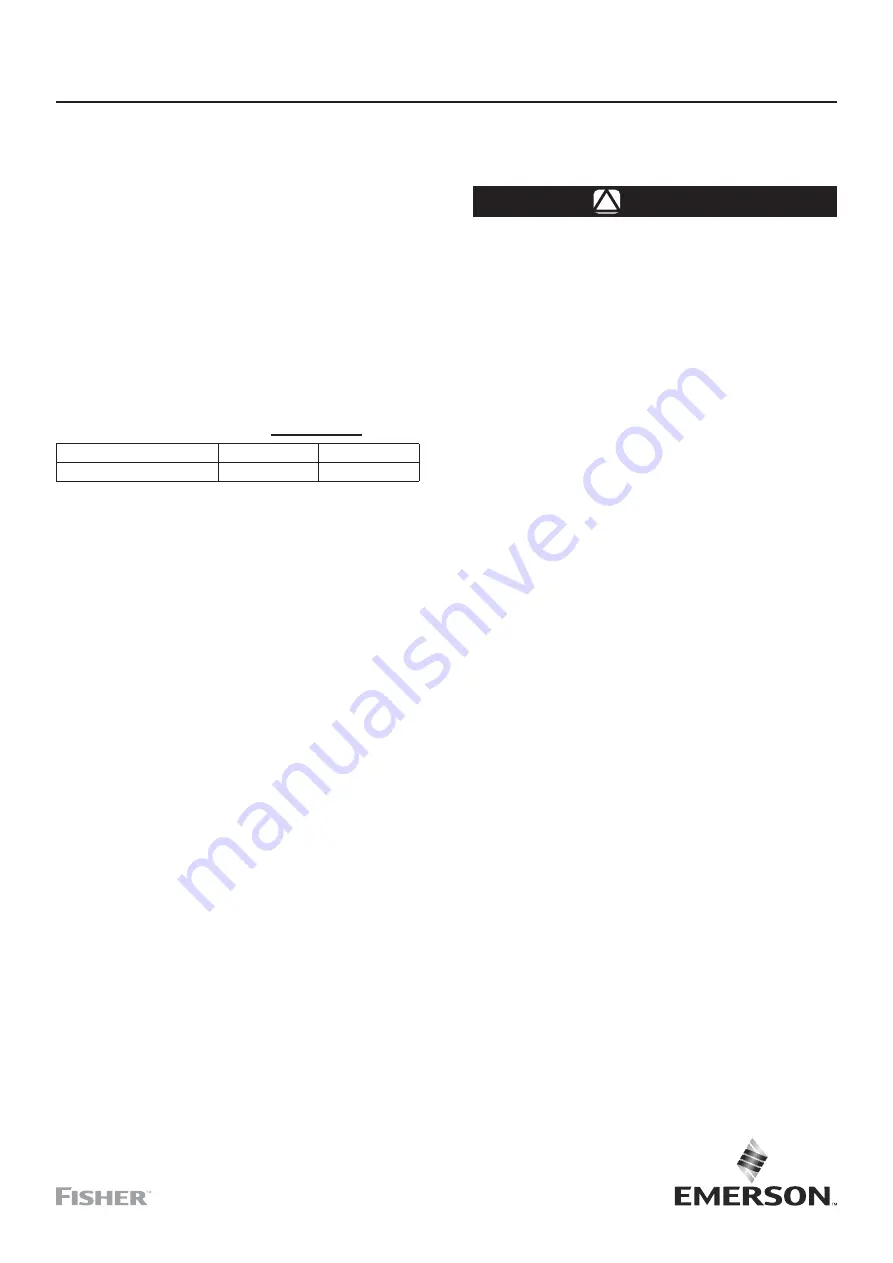
PRODUCT SIZE
CATEGORY
FLUID TYPE
DN 20 and 25 / 3/4 and 1 in.
SEP
1
!
Installation Guide
D103750X014
English – June 2020
Type T205B
Introduction
This installation guide provides instructions for
installation, startup and adjustment. To receive a copy of
the instruction manual, contact your local Sales Office or
view a copy at www.fisher.com. For further information,
refer to: Type T205B Balanced Tank Blanketing
Regulator Instruction Manual, D103750X012.
PED Categories
This product may be used as a safety accessory with
pressure equipment in the following Pressure Equipment
Directive categories. It may also be used outside of the
Pressure Equipment Directive using sound engineering
practice (SEP) per table below. For information on the
current PED revision see Bulletin:
.
Specifications
Body Sizes and End Connection Styles
See Table 1
Maximum Allowable and Operating Inlet Pressure
(1)
See Table 1
Maximum Outlet (Casing) Pressure
(1)
See Table 1
Maximum Emergency Outlet Pressure to Avoid
Internal Parts Damage
(1)
With Nitrile (NBR) or Fluorocarbon (FKM)
diaphragm:
2.4 bar / 35 psig
With Fluorinated Ethylene Propylene (FEP)
diaphragm:
0.69 bar / 10 psig
Outlet (Control) Pressure Ranges
(1)
See Table 3
Shutoff Classification per ANSI/FCI 70-3-2004
Class VI (Soft Seat)
Material Temperature Capabilities
(1)(2)
Elastomer Parts
Nitrile (NBR):
-40 to 82°C / -40 to 180°F
Fluorinated Ethylene Propylene (FEP):
-29 to 82°C / -20 to 180°F
Fluorocarbon (FKM):
4 to 149°C /
40 to 300°F
Ethylene Propylene Diene (EPDM):
-29 to 107°C /
-20 to 225°F
Perfluoroelastomer (FFKM):
-18 to 149°C /
0 to 300°F
Body Materials
Gray Cast Iron
(3)
:
-29 to 149°C / -20 to 300°F
WCC Carbon Steel:
-29 to 149°C / -20 to 300°F
LCC Carbon Steel:
-40 to 149°C / -40 to 300°F
CF8M/CF3M Stainless Steel:
-40 to 149°C /
-40 to 300°F
Installation
Only qualified personnel shall install
or service a regulator. Regulators
should be installed, operated and
maintained in accordance with
international and applicable codes
and regulations and Emerson
Process Management Regulator
Technologies, Inc. instructions.
If the regulator vents fluid or a leak
develops in the system, it indicates that
service is required. Failure to take the
regulator out of service immediately
may create a hazardous condition.
Personal injury, equipment damage
or leakage due to escaping fluid
or bursting of pressure containing
parts may result if this regulator is
overpressured or is installed where
service conditions could exceed the
limits given in the Specifications
section, or where conditions exceed
any ratings of the adjacent piping or
piping connections.
To avoid such injury or damage, provide
pressure-relieving or pressure-limiting
devices (as required by the appropriate
code, regulation or standard) to
prevent service conditions from
exceeding limits.
Additionally, physical damage to the
regulator could result in personal injury
and property damage due to escaping
fluid. To avoid such injury and damage,
install the regulator in a safe location.
Clean out all pipelines before installation of the
regulator and check to be sure the regulator has not
been damaged or has collected foreign material during
shipping. For NPT bodies, apply pipe compound
to the external pipe threads. For flanged bodies,
use suitable line gaskets and approved piping and
bolting practices. Install the regulator in any position
desired
(3)
, unless otherwise specified, but be sure flow
through the body is in the direction indicated by the
arrow on the body.
WARNING
1. The pressure/temperature limits in this Installation Guide and any applicable standard or code limitation should not be exceeded.
2. See Table 2 for operating temperature ranges for available trim combinations.
3. For proper operation to achieve the published capacities at low setpoint, the spring case barrel should be installed pointed down as shown in Figure 1.