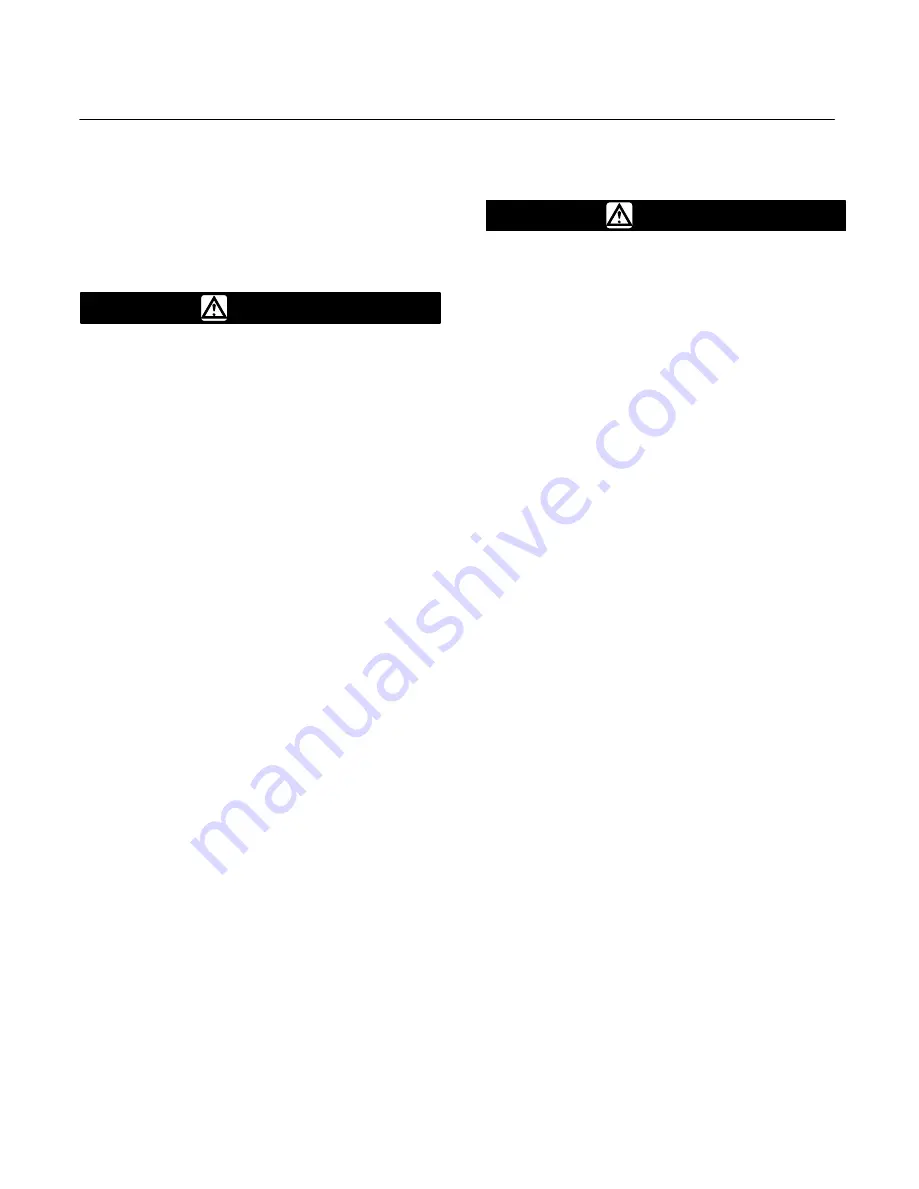
2502 Series Controllers
Instruction Manual
Form 1446
November 2006
9
the nuts are tight at each end of the stem. Install and
tighten suitable cap screws in the flanged connection
to complete the installation.
Regulator Supply Pressure
WARNING
Do not overpressurize any system
component. Personal injury or
property damage may occur due to
sudden pressure release or explosion.
To avoid damage, provide suitable
pressure-relieving or pressure limiting
devices if supply pressure can exceed
the maximum supply pressure listed in
table 1.
Personal injury or property damage
may occur from an uncontrolled
process if the supply medium is not
clean, dry, oil-free, or non-corrosive
gas. While use and regular
maintenance of a filter that removes
particles larger than 40 microns in
diameter will suffice in most
applications, check with an Emerson
Process Management field office and
industry instrument air quality
standards for used with corrosive gas
or if you are unsure about the proper
amount or method of air filtration or
filter maintenance.
Standard 2502 Series controllers come complete
with supply and output pressure gauges and an
integrally mounted Type 67CFR regulator to reduce
supply pressure from a maximum of 17.3 bar (250
psig) to the 1.4 or 2.4 bar (20 or 35 psig) required.
This regulator has built-in relief and a standard
40-micron to remove particles from the supply
source.
The output pressure connection is on the back of the
controller case (figure 3). Pipe the supply pressure
to the in connection of the regulator mounted to the
case back. Provide a clean, dry, and noncorrosive
air or gas supply to the controller as follows:
After pressure connections have been made, turn on
the supply pressure and check all connections for
leaks.
Prestartup Checks
WARNING
The following procedure requires
taking the controller out of service. To
avoid personal injury and property
damage caused by an uncontrolled
process, provide some temporary
means of control for the process
before taking the controller out of
service.
Adjustment locations are shown in figure 9 unless
otherwise indicted. When performing the checks
open loop conditions must exist. To obtain open-loop
conditions:
D
make sure there is no process flow through the
final control element, or
D
disconnect the controller output signal line and
plug the output connection.
During startup, it is necessary to change process
levels to position the displacer from its maximum to
its minimum range of operations. Provide a means to
change the process level or interface. If the process
variable cannot be varied sufficiently, follow the
instructions in the Calibration section to simulate the
process variable changes required for these checks.
Make sure that the RAISE LEVEL dial on the
controller is mounted with the correct side facing out.
The dial is printed on both sides with the arrow on
one side pointing to the left and the arrow on the
other side pointing to the right. Figure 9 shows the
dial arrow positioned for a sensor that is mounted to
the left of the controller; the arrow points to the left. If
the sensor is to the right of the controller, remove the
two mounting screws, turn the dial over so the arrow
points to the right, then reinstall the mounting
screws.
On a controller with optional level indicator assembly
the travel indicator plate is printed on both sides. If
the sensor is to the left of the controller (right-hand
mounting), use the side of the plate that has the
arrow pointing to the left. If displacer is to right of
controller (left-hand mounting), use the side of the
plate that has the arrow pointing to the right.