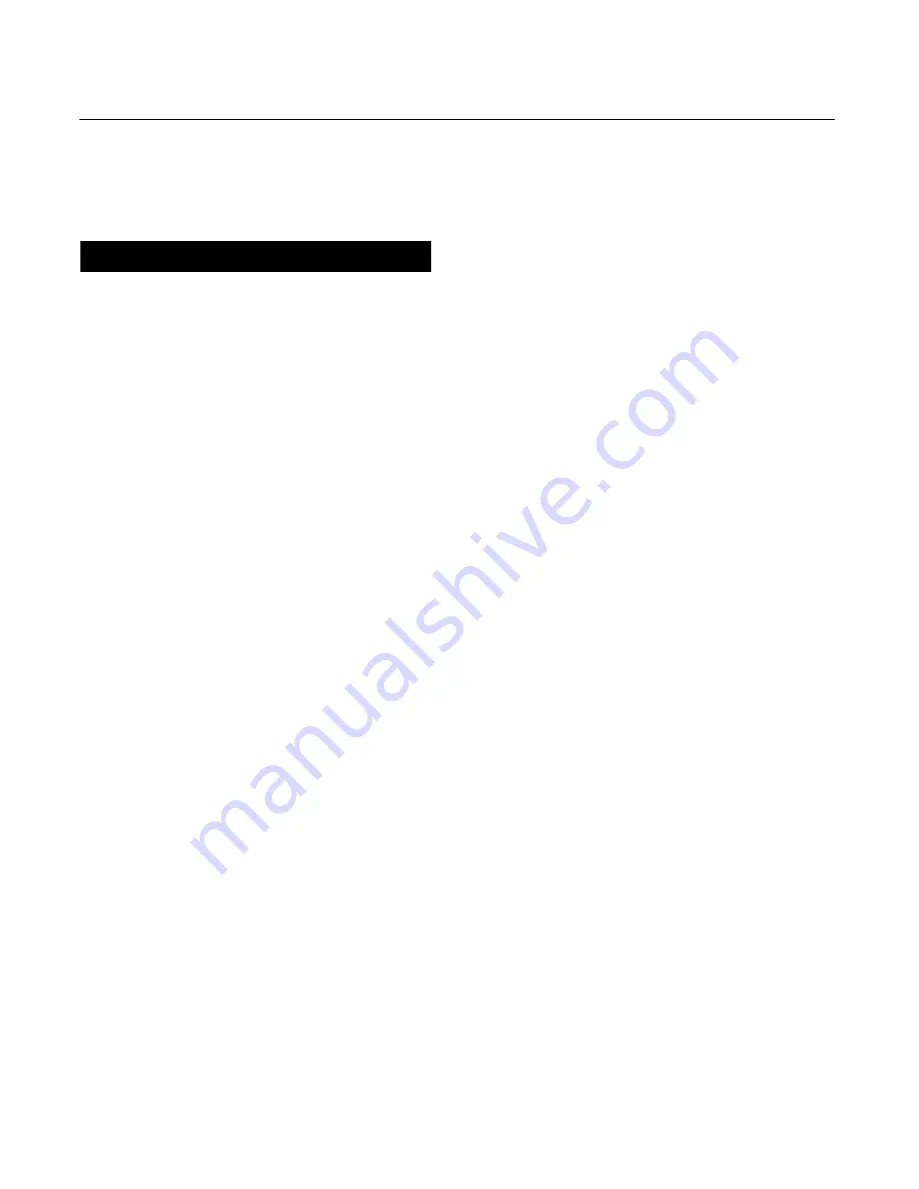
2502 Series Controllers
Instruction Manual
Form 1446
November 2006
21
as shown in the figure. Then mount the insulator
assembly (key 35) on the controller case with four
washers (key 53) and button-head cap screws
(key 40). Tighten the screws.
CAUTION
In the following step, avoid bending
the torque tube rotary shaft of the
torque tube assembly. Bending or side
loading of this shaft could cause
erroneous readings. Additionally,
make sure the ball bearing assembly
(key 12, figure 14) is removed from the
case (key 1, figure 14) to provide
clearance when installing the case on
the sensor.
2. Remove the bearing assembly (key 12) from the
case (key 1).
3. Carefully slide the controller case straight in,
guiding the bearing assembly (key 12), operating
arm base or pointer assembly (key 68 or 51,
figure 14) over the rotary shaft and easing an
attached heat insulator over the shaft coupling
(key 36) if necessary. Secure the case or
insulator to the torque tube arm with the four cap
screws (key 39).
Note
If a heat insulator is used, do not
insulate its exterior.
4. On a unit without a heat insulator, tape the joint
between the case and torque tube arm to minimize
the entrance of atmospheric moisture around the
torque tube rotary shaft.
5. Install and tighten the bearing assembly (key 12,
figure 14) in the case (key 1, figure 14). Secure the
operating arm base or pointer assembly to the rotary
shaft by tightening the hex nut (key 40, figure 14).
Connect the supply and output pressure tubing and
perform the calibration procedure.
Changing Proportional, Reset, or
Differential Relief Valve
1. Remove the proportional band valve assembly
(key 36, figure 14) by unscrewing it from the relay
base (key 23, figure 14). Install the desired
replacement assembly, or a 1/8-inch NPT pipe plug
into the proportional band tapping if testing relay
dead band.
2. To change the reset restriction valve assembly
(key 91), remove the two mounting screws (key 182)
located on the back side of case. Install the
replacement valve assembly, and reconnect the
tubing connections.
3. Remove the differential relief valve assembly
(key 186, figure 14) by removing the two mounting
screws (figure 9) that anchor the valve to the
manifold (key 184, figure 14). Install the valve with
the arrow pointing to the same letter(s) as before
removal, unless it is desired to change the relief
action.
Testing Relay Dead Band
1. Replace the proportional band adjustment
assembly with a 1/8-inch NPT pipe plug according to
the Changing Proportional, Reset, or Differential
Relief Valve section.
2. Turn on the supply pressure and set it to1.4
or 2.4 bar (20 or 35 psig).
3. By changing the process variable and adjusting
the RAISE LEVEL control, set the output pressure to
1.0 or 2.0 bar (15 or 30 psig). While monitoring the
output pressure, slowly change the process until an
output pressure change can just be detected, and
record the value of the process variable at the
detection point.
4. Change the process variable in the opposite
direction until another output pressure change can
be detected, and again record the value of the
process variable. If the difference between the two
recorded values (the dead band) is more than 0.2
percent of the maximum displacer length, the relay
will have to be replaced or repaired according to the
Changing Relay and the Disassembling Relay
sections.
5. Turn off the supply pressure, remove the pipe
plug, and install the proportional band adjustment
assembly.
Changing Relay
The relay may be removed for cleaning or
replacement, and must be taken off to remove the
lower bellows.
1. On a controller with indicator assembly, loosen the
two lower screws of the relay case and slide out the
indicator base plate (key 53, figure 14).
2. Disconnect the tubing (key 11, figure 14) from the
relay.
3. Remove both mounting screws, the relay, and the