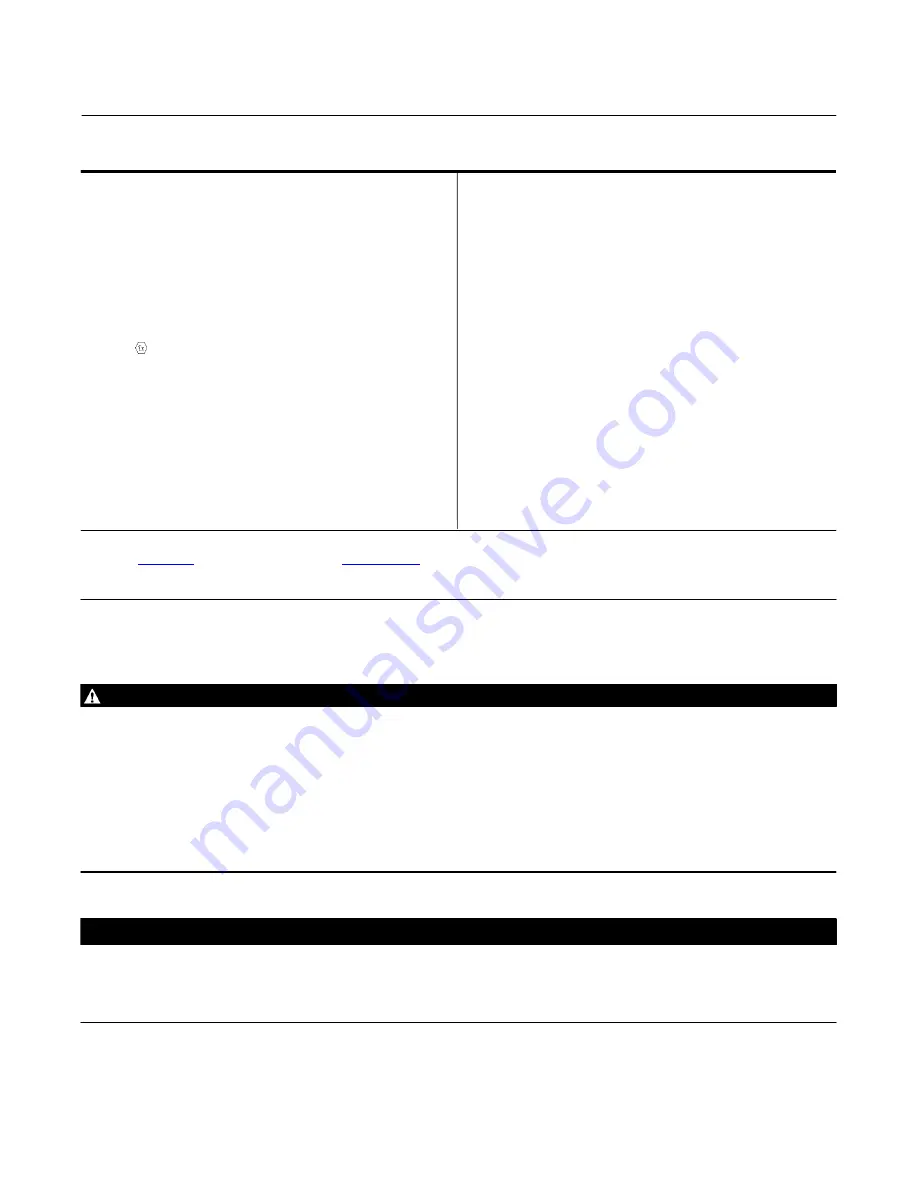
Instruction Manual
D103531X012
L2e Controller
June 2022
4
Table 1. Specifications (continued)
Hazardous Area Classifications Available
Switch Only
Refer to to GH04148 instruction manual
(D104234X012) for switch information
cCSAus
Explosion-proof Class I Division 1, Groups ABCD
Dust Ignition-proof Class II Division 1 2, Groups EFG
Single Seal
ATEX II 2 GD
Flameproof Ex d IIC T5 (Ta ≤ @85°C) /
T6 (Ta≤ @ 78°C)
Dust Ex tb IIIC T92°C / T85
°
C Db IP6X
1 A Max
IECEx
Flameproof Ex d IIC T5 (Ta ≤ @85°C) /
T6 (Ta≤ @ 78°C)
Dust Ex tb IIIC T92°C / T85
°
C Db IP6X
1 A Max
Ingress Protection Rating per IEC 60529: IP66
Refer to D104234X012 for Special Conditions of Safe
Use
Canadian Registration (CRN)
Refer to the L2 CRN which is deemed applicable to
the L2e.
Declaration of SEP
Fisher Controls International LLC declares this
product to be in compliance with Article 4 paragraph
3 of the PED Directive 2014/68/EU. It was designed
and manufactured in accordance with Sound
Engineering Practice (SEP) and cannot bear the CE
marking related to PED compliance.
However, the product may bear the CE marking to
indicate compliance with other applicable European
Community Directives.
NOTE: Specialized instrument terms are defined in ANSI/ISA Standard 51.1 Process Instrument Terminology.
1. Converting from a threaded NPT connection to a flange connection is to be done by the end-user. Refer to Converting a Threaded NPT Connection to a Flange Connection instruction Manual
Supplement (
), available at Fisher.com or from your
2. Maximum span setting with 1 7/8 x 12 inch horizontal displacer plus 6 inch extension is not recommended due to potentially insufficient zero adjustment.
3. The pressure and temperature limits in this document and any applicable code limitations should not be exceeded.
4. Electronic switch pressure rating is based on maximum pressure at sensor. Controller housing vent is designed to drop maximum process pressure to less than 6.9 bar (100 psig) at switch.
Installation
WARNING
Always wear protective clothing, gloves, and eyewear when performing any installation operations to avoid personal
injury.
To avoid personal injury or property damage caused by the sudden release of process fluid, be certain the service
conditions do not exceed the sensor pressure limits. Use pressurelimiting or pressurerelieving devices to prevent service
conditions from exceeding these limits.
Check with your process or safety engineer for any additional measures that must be taken to protect against process
media.
If installing this into an existing application, also refer to the WARNING at the beginning of the Maintenance section of this
instruction manual.
NOTICE
If the L2e
electric level controller is installed on a vessel that is to be shipped to a different location (e.g. skid mounted
units), remove the displacer and displacer rod extensions before shipment. Failure to do so could result in damage to the
instrument and or the displacer rod due to vibration and impact loading during shipment. After the vessel is installed at its
final location, reassemble the displacer and displacer rod extension.