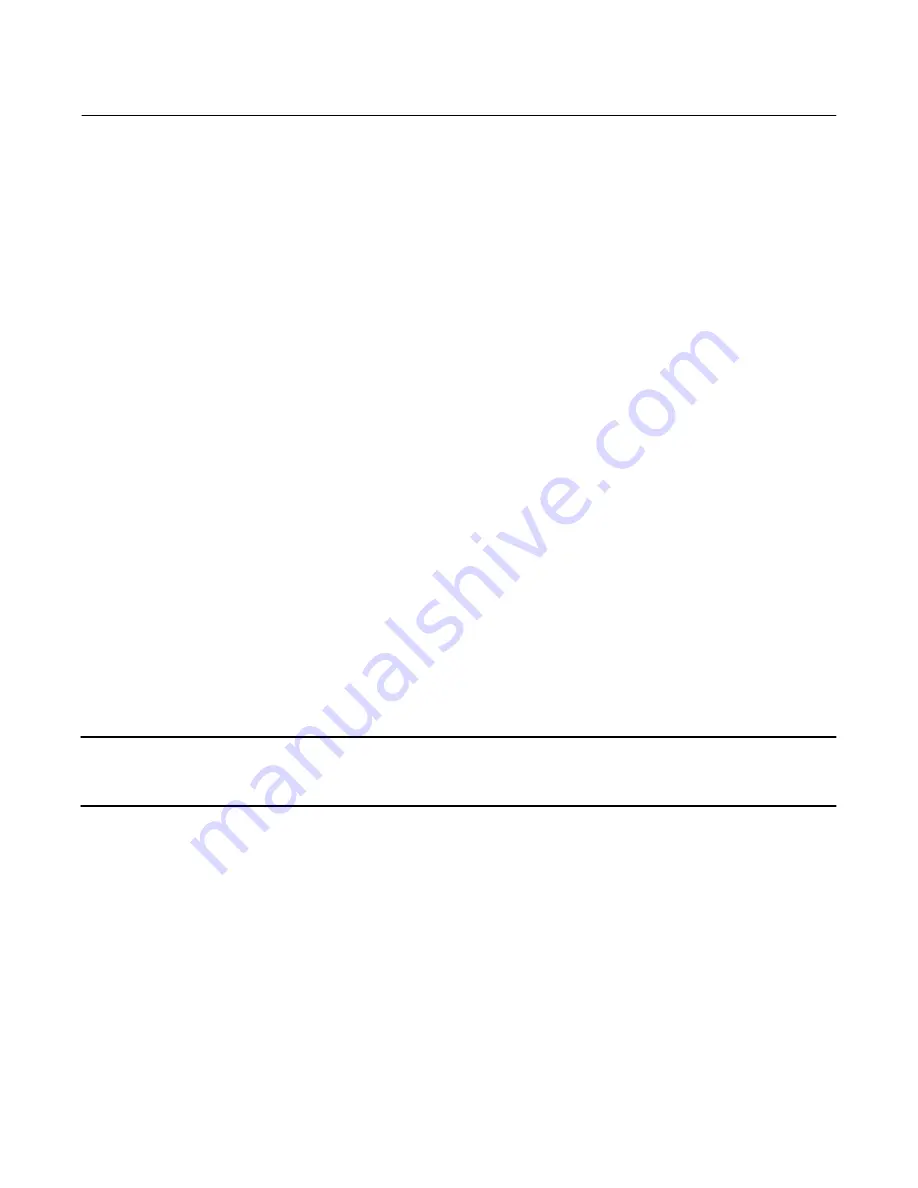
Instruction Manual
D103785X012
Maintenance and Troubleshooting
June 2017
75
DVC6025 Remote Feedback Unit
Refer to figure 7‐5 for key number locations.
1. Remove piping and fittings from the instrument.
2. Remove the instrument from the actuator.
3. Disconnect the bias spring (key 82) from the feedback arm assembly (key 84) and the arm assembly (key 91).
Remove the mounting bracket (key 74) from the back of the digital controller. If the torsion spring (key 93) needs to
be replaced, ensure that the shaft on which it is installed is smooth and free of rough spots. Replace the entire
feedback arm assembly if necessary.
4. Loosen the screw (key 80) that secures the arm assembly to the travel sensor assembly shaft.
5. Remove the arm assembly (key 91) from the travel sensor assembly shaft.
6. Disconnect the three travel assembly wires from the terminals.
7. Remove the screw (key 72) that fastens the travel sensor assembly to the housing.
8. Pull the travel sensor assembly (key 223) straight out of the housing.
DVC6035 Remote Feedback Unit
Refer to figure 7‐6 for key number locations.
1. Remove piping and fittings from the instrument.
2. Remove the instrument from the actuator. Loosen the screw (key 80) that secures the feedback arm (key 79) to the
travel sensor shaft. Remove the feedback arm from the travel sensor assembly shaft.
3. Disconnect the three travel sensor assembly wires from the terminals.
4. From within the housing, unscrew the travel sensor assembly (key 223) from the housing.
Assembly
Note
If the feedback arm (key 79) or feedback arm assembly (key 84) is removed from the digital valve controller, the travel sensor
assembly must be recalibrated.
DVC6015 Remote Feedback Unit
Refer to figure 7‐4 for key number locations.
1. Insert the travel sensor assembly (key 223) into the housing (key 1). Secure the assembly with screw (key 72).
2. Connect the travel sensor assembly wires to the terminals as follows:
red
terminal 1
white
terminal 2
black
terminal 3
3. Loosely assemble the bias spring (key 78), screw (key 80), plain washer (key 163), and nut (key 81) to the feedback
arm (key 79), if not already installed.
4. Attach the feedback arm (key 79) to the travel sensor assembly shaft.