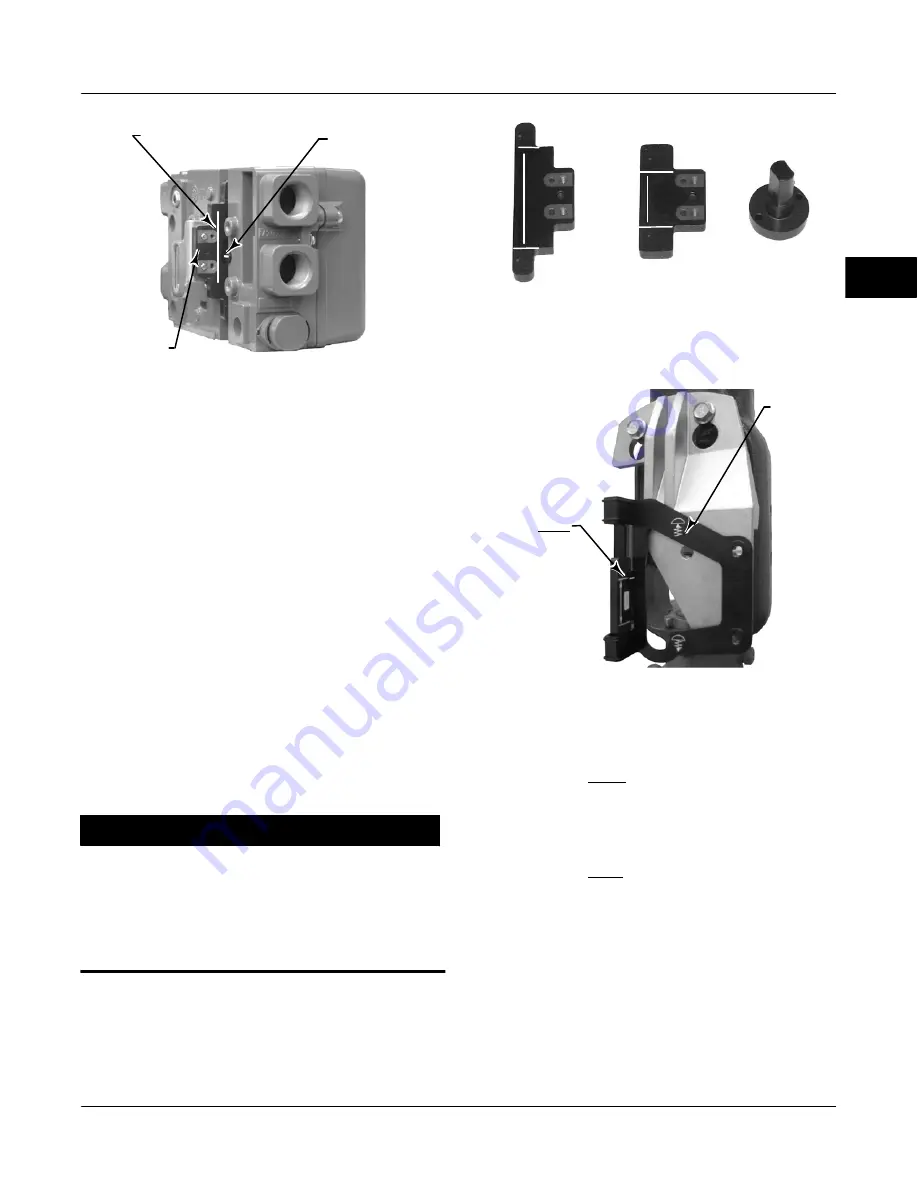
Installation
July 2009
2-5
Figure 2-2. Travel Range
INDEX MARK
VALID TRAVEL RANGE
50 mm (2 INCH) SHOWN
MAGNET
ASSEMBLY
(ATTACHED TO
VALVE STEM)
W8830
Rotary actuators with travel up to 90 degrees.
See figure 2-3 for the different travel feedback magnet
assemblies.
Sliding
−
Stem (Linear) Actuators
1. Isolate the control valve from the process line
pressure and release pressure from both sides of the
valve body. Shut off all pressure lines to the actuator,
releasing all pressure from the actuator. Use lock-out
procedures to be sure that the above measures stay in
effect while you work on the equipment.
2. Attach the mounting bracket to the actuator.
3. Loosely attach the feedback pieces and magnet
assembly to the valve stem connector. Do not tighten
the fasteners because fine adjustment is required.
CAUTION
Do not install a magnet array that is
shorter than the physical travel of the
actuator. Loss of control will result
from the magnet array moving outside
the range of the index mark in the
feedback slot of the DVC2000 housing.
4. Using the alignment template (supplied with the
mounting kit), position the feedback array inside the
retaining slot.
5. Align the magnet array as follows:
Figure 2-3. Magnet Assemblies
W9014
SLIDING STEM (LINEAR)
50 mm (2-INCH)
ROTARY
90
NOTE: VALID TRAVEL RANGE INDICATED BY WHITE ARROWS
SLIDING STEM (LINEAR)
25 mm (1-INCH)
Figure 2-4. Air-to-Open Magnet Array Alignment
W9220
ALIGNMENT
TEMPLATE
LINE UP WITH UPPER
EXTREME OF VALID
TRAVEL RANGE
For air-to-open actuators (e.g. Fisher 667)
vertically align the magnet array so that the center line
of the alignment template is lined up as close as
possible with the upper extreme of the valid travel
range on the feedback array. See figure 2-4.
For air-to-close actuators (e.g. Fisher 657)
vertically align the magnet array so that the center line
of the alignment template is lined up as close as
possible with the lower extreme of the valid travel
range on the feedback array. See figure 2-5.so that
the center line of the alignment template is lined up as
close as possible with the upper extreme of the valid
travel range on the feedback array. See figure 2-5.
6. Tighten the fasteners and remove the alignment
template.
7. Mount the digital valve controller to the mounting
bracket, using the mounting bolts. See figure 2-6.
8. Check for clearance between the magnet assembly
and the DVC2000 feedback slot. The magnet
assembly should be positioned so that the index mark
2
Содержание Fisher FIELDVUE DVC2000
Страница 40: ...DVC2000 Digital Valve Controller July 2009 3 14 3 ...
Страница 70: ...DVC2000 Digital Valve Controller July 2009 6 10 6 ...
Страница 71: ...Parts July 2009 7 1 7 7 Section 7 Parts Parts Ordering 7 2 Parts Kits 7 2 Parts List 7 2 7 ...
Страница 77: ...Principle of Operation July 2009 A 1 A A Appendix A Principle of Operation DVC2000 Operation A 2 A ...
Страница 80: ...DVC2000 Digital Valve Controller July 2009 A 4 A ...
Страница 104: ...DVC2000 Digital Valve Controller July 2009 Index 8 C Index ...
Страница 105: ......