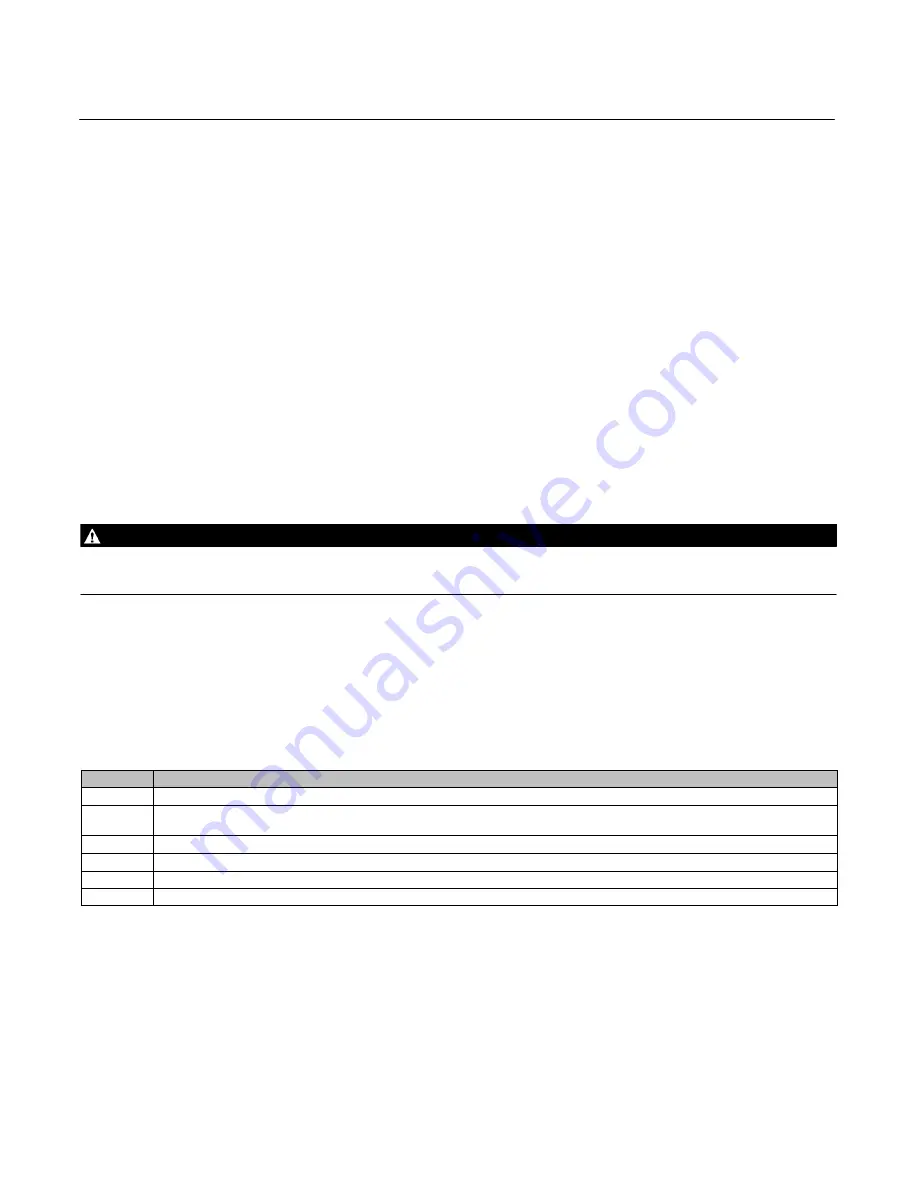
Instruction Manual Supplement
D103401X012
ED, ES, ET, EW, EZ, HP Valves
November 2017
9
General Requirements
The system's response time shall be less than process safety time. The final control element subsystem needs to be
sized properly to assure that the response time is less than the required process safety time. The ED, ES, ET, EW, EZ, or
HP valve will move to its safe state in less than the required SIF's safety time under the specified conditions.
All SIS components including the ED, ES, ET, EW, EZ, or HP valve must be operational before process startup.
The user shall verify that the ED, ES, ET, EW, EZ, or HP valve is suitable for use in safety applications.
Personnel performing maintenance and testing on the ED, ES, ET, EW, EZ, or HP valve shall be competent to do so.
Results from the proof tests shall be recorded and reviewed periodically.
The useful life of the ED, ES, ET, EW, EZ, or HP valve is discussed in the Failure Modes, Effects and Diagnostic Analysis
Report for the Fisher ED, ES, ET, EW, EZ, and HP valves.
Installation and Commissioning
Installation
WARNING
To ensure safe and proper functioning of equipment, users of this document must carefully read all instructions, warnings,
and cautions in each applicable instruction manual.
The Fisher ED, ES, ET, EW, EZ, or HP valve must be installed per standard practices outlined in the appropriate
instruction manual.
The environment must be checked to verify that pressure and temperature conditions do not exceed the ratings.
The ED, ES, ET, EW, EZ, or HP valve must be accessible for physical inspection.
Table 1. Recommended Full Stroke Proof Test
Step
Action
1
Bypass the safety function and take appropriate action to avoid a false trip.
2
Interrupt or change the signal/supply to the actuator to force the actuator and valve to perform a full stroke to the FailSafe state and
confirm that the Safe State was achieved and within the correct time.
3
Restore the supply/signal to the actuator and confirm that the normal operating state was achieved.
4
Inspect the ED, ES, ET, EW, EZ, or HP valve and the other final control element components for any leaks, visible damage or contamination.
5
Record the test results and any failures in your company's SIF inspection database.
6
Remove the bypass and restore normal operation.
Physical Location and Placement
The Fisher ED, ES, ET, EW, EZ, or HP valve shall be accessible with sufficient room for the actuator, pneumatic
connections, and any other components of the final control element. Provisions shall be made to allow for manual
proof testing.
The ED, ES, ET, EW, EZ, or HP valve shall be mounted in a low vibration environment. If excessive vibration can be
expected special precautions shall be taken to ensure the integrity of pneumatic connectors or the vibration should be
reduced using appropriate damping mounts.