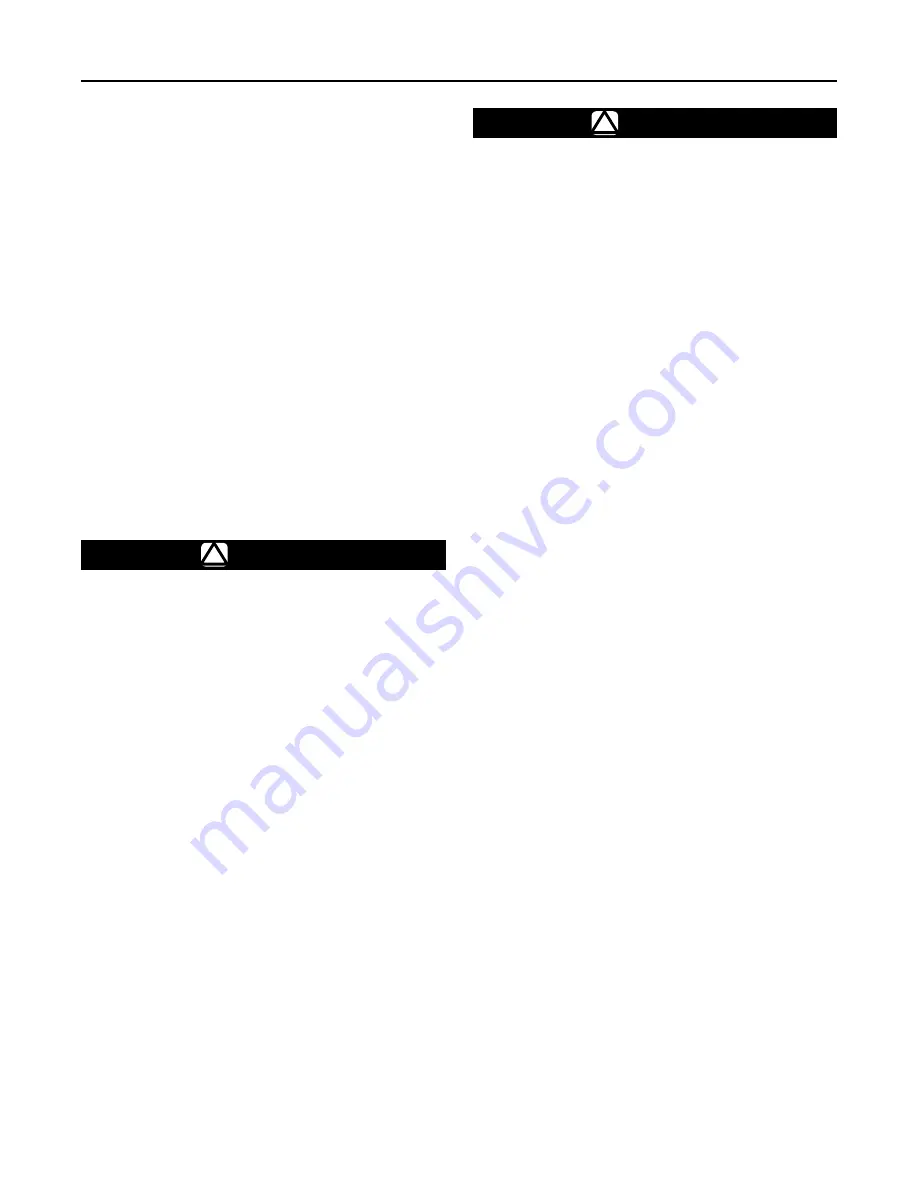
630 Series
5
the valve open. When the outlet pressure exceeds the
set pressure, the diaphragm moves to compress the
spring and the lever closes the valve until the outlet
pressure returns to set pressure.
Type 630R Relief Valves
Refer to Figure 3. In the relief valve construction, inlet
pressure registers beneath the diaphragm. As long
as the inlet pressure is less than the set pressure,
spring force causes the lever to hold the valve closed.
When the inlet pressure exceeds the set pressure,
the diaphragm moves to compress the spring and the
lever opens the valve allowing inlet pressure to bleed
into the downstream line or to atmosphere until the
inlet pressure returns to set pressure.
Maintenance
Parts are subject to normal wear and must be inspected
and replaced as necessary. Frequency of inspection
depends upon severity of service conditions.
!
WaRnIng
To avoid personal injury or equipment
damage, isolate the regulator or
relief valve from the pressure system
and release all pressure from the
regulator or relief valve before
performing maintenance.
Except where indicated, key numbers in the following
procedures are shown in Figures 4 and 5 for the
Type 630 regulator, in Figure 6 for the Type 630R
relief valve.
Replacing Orifice, Valve Disk and Lever
note
With some piping systems it may
be possible to omit step 1 below by
removing four cap screws (key 17) and
spreading the body (key 23) and inlet
adaptor (key 18) far enough apart to
allow removal of the orifice (key 20)
and Type 630 valve disk (key 21,
Figures 4 and 5) or the orifice (key 20)
and the Type 630R valve seat O-ring
(key 37, figure 6).
CaUTIOn
If step 1 is omitted and the body and
inlet adaptor are separated, take care to
avoid pinching fingers between the body
and the inlet adaptor.
1. Disconnect piping from inlet adaptor (key 18).
Remove four cap screws (key 17) and adaptor.
2.
Remove orifice (key 20) and gaskets (key 19).
3. To remove Type 630 valve disk (key 21, Figures 4
and 5) or Type 630R valve seat O-ring (key 37,
Figure 6), first disconnect remote vent pipe (if one
is used).
4. Unscrew the two cap screws (key 31, not shown)
that secure diaphragm adaptor (key 13) to body
(key 23); remove diaphragm adaptor and attached
spring case (key 3).
5. If it is necessary to replace the lever (key 14),
drive out the pin (key 15) and slide the lever out
of the diaphragm adaptor. When replacing the
lever, make sure the slot engages the connector
assembly (key 12) and replace the pin.
6. Remove valve carrier assembly (key 22)
from body.
7. To replace seating surface:
a. For Type 630, use a 3/4 in. / 19.1 mm socket
wrench to remove and re-install valve disk and
holder assembly (key 21, Figures 4 and 5).
b. For Type 630R, unscrew machine screw (key 36,
Figure 6) and remove O-ring washer and
O-ring (keys 32 and 37, Figure 6) from O-ring
holder (key 21, Figure 6). When reassembling,
apply a good-quality gasket shellac to the
machine screw thread.
8.
Use new orifice gaskets (key 19) and body
gasket (key 16) when reassembling. Insert valve
carrier assembly (key 22) into the body before
re-installing the diaphragm adaptor.
note
The spring case (key 3) must point
away from the inlet adaptor (key 18)
on Type 630 regulators as shown in
figures 4 and 5. On Type 630R relief
valves, the spring case (key 3) must face
the same direction as the inlet adaptor
(key 18) as shown in figure 6.