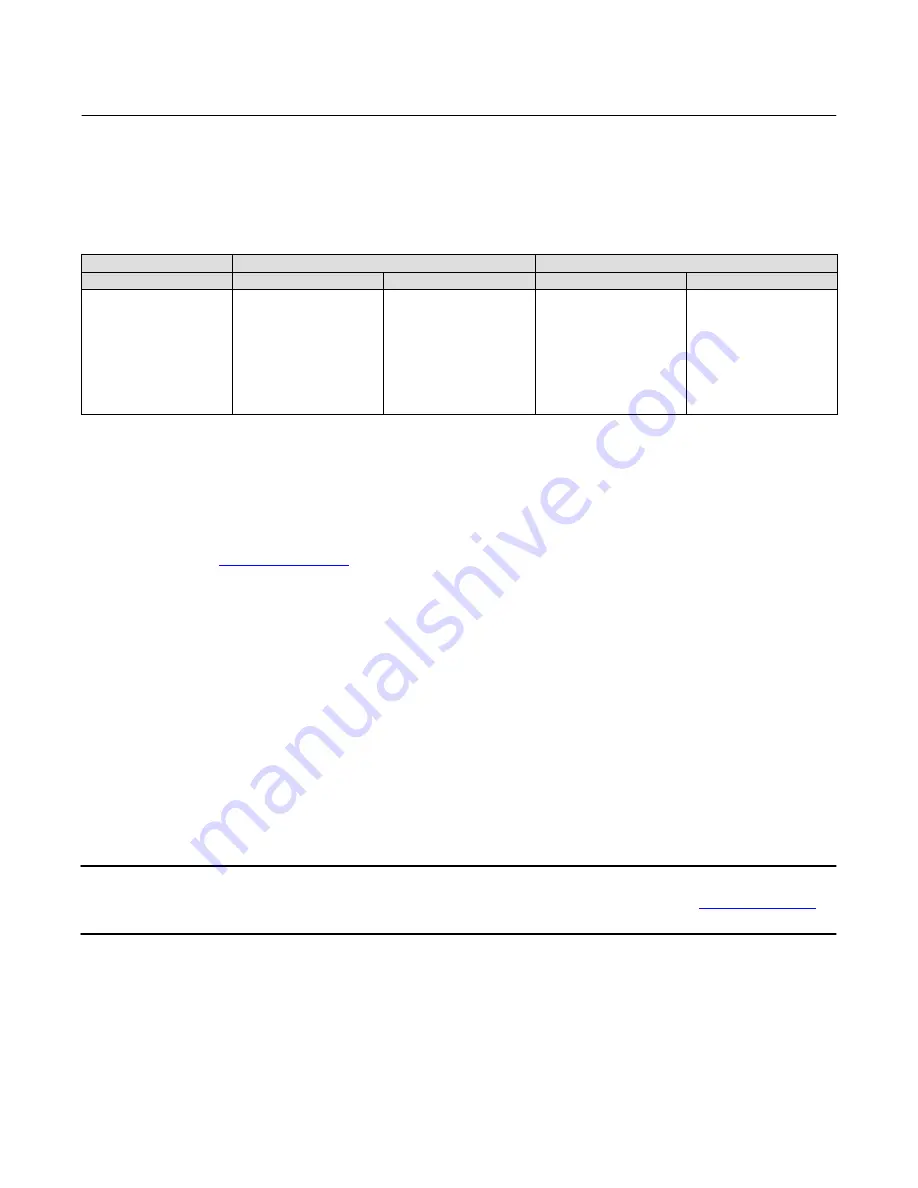
Instruction Manual
D103425X012
546NS Transducer
June 2021
12
Recalibration
Table 5 shows typical recorded data where recalibration is necessary.
Table 5. Typical Calibration Data
TRANSDUCER INPUT
ACTUAL OUTPUT PRESSURE
TARGET OUTPUT PRESSURE
mA DC
Bar
Psig
Bar
Psig
12.00
16.00
20.00
16.00
12.00
8.00
4.00
8.00
12.00
0.612
0.823
1.035
0.828
0.617
0.413
0.207
0.409
0.618
8.89
11.95
15.02
12.02
8.96
6.00
3.01
5.95
8.97
0.620
0.826
1.033
0.826
0.620
0.413
0.206
0.413
0.620
9.00
12.00
15.00
12.00
9.00
6.00
3.00
6.00
9.00
The 0.612 bar (8.89 psig) value at 12.00 mA DC is outside the accuracy limit of
±
0.09 from the target value. This data
point can be raised by recalibrating the transducer and raising the end points enough to bring this low value within
-0.6 mbar (-0.09 psig) of 0.62 bar (9.00 psig). A reasonable recalibration would be 0.21 and 1.04 bar (3.05 and 15.05
psig) at 4.00 mA DC and 20.00 mA DC, respectively. Recalibrate the instrument and recheck the calibration data as
described in steps 7 through 10.
If the transducer remains outside of accuracy specifications after altering the calibration end points as much as
possible consult your
For transducers inaccurate to less than 5 percent of output span, relay repair or replacement may correct the problem.
Refer to the alignment procedures in the Troubleshooting section to correct the operation of a faulty transducer. Also
check for air leaks at the tubing, nozzle, relay, and bellows.
If the accuracy error is greater than 5 percent of output span, check the clearance between the armature and the coils.
These parts are referenced as key 40 and key 42, respectively, in the Parts List section. The armature and the white
plastic coil bobbin should be approximately 0.4 mm (1/64 inch) apart. If the parts are in contact, loosen the machine
screws that hold the bobbin and reposition the bobbin.
Changing Output Pressure Range
Changing the output pressure range from 0.2 to 1.0 bar (3 to 15 psig) to 0.4 to 2.0 bar (6 to 30 psig) or vice versa
requires changing the feedback bellows (key 57, figure 8). To do this, refer to the replacing the feedback bellows
assembly procedures in the Maintenance section.
Note
Re‐magnetization of the torque motor is required when changing the output pressure range. Contact your
or
service center.
Reversing the Action
Reversing the action of a 546NS transducer requires no special parts. The direction of armature rotation is dependent
upon the direction of the current flow. Therefore, simply reverse the input current leads to the transducer to obtain
the opposite action. Whenever the action is changed, readjust the zero of the transducer as outlined in the
adjustments procedures.