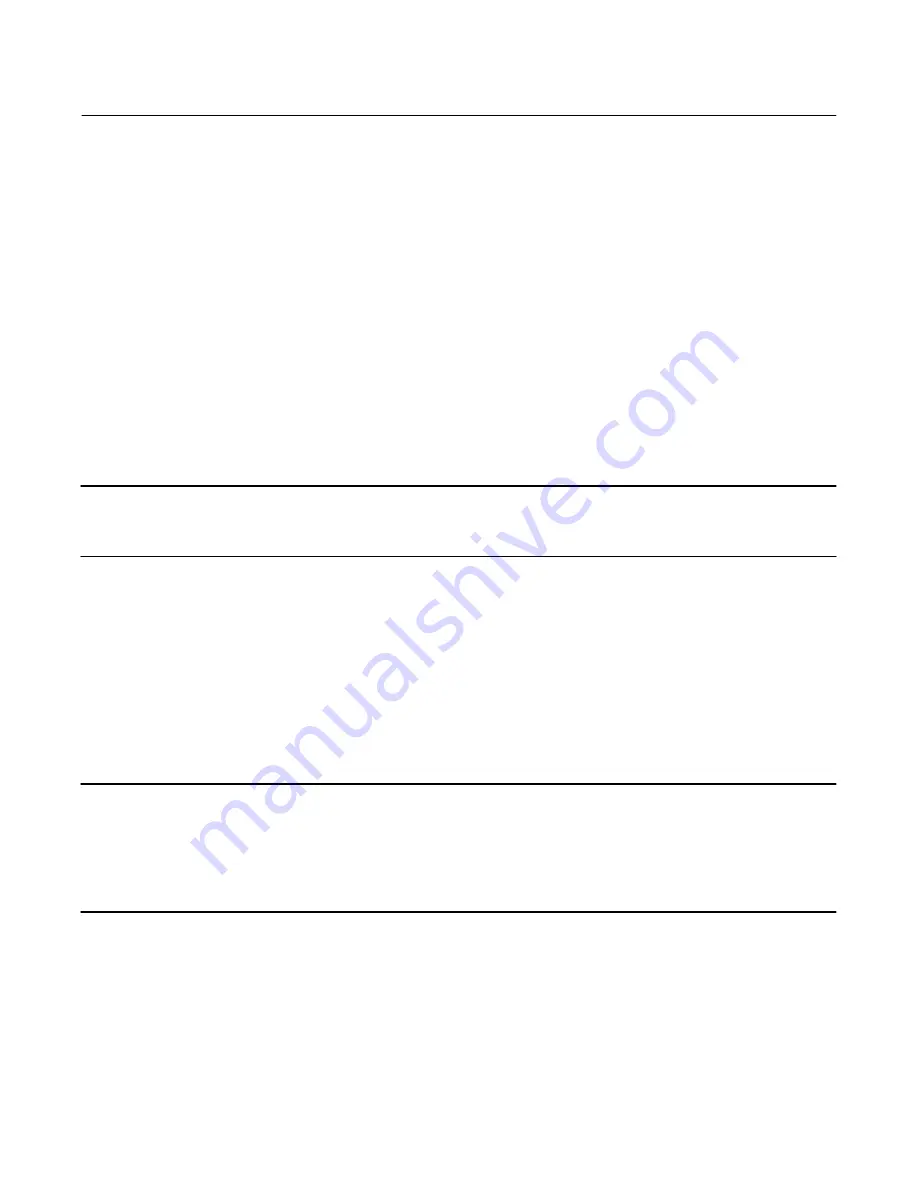
Instruction Manual
D101728X012
3710 and 3720 Positioners
September 2017
27
Tighten the zero adjustment locknut before proceeding to step 5.
5. Slowly increase the input signal until the input reaches the maximum input signal. Observe the actuator travel and
valve position as the input increases. Determine the actuator/valve position at the maximum input signal.
6. After observing the actuator/valve travel at maximum input signal, return the input signal to the minimum input
signal before turning the span adjustment knob.
D
If the actuator/valve travel, observed in step 5,
stopped short
of the required valve position at maximum input
signal, increase the actuator/valve travel by rotating the positioner span adjustment knob toward the zero
adjustment nut (key 35) to add active spring coils to the range spring.
D
If the actuator/valve travel, observed in step 5, reaches the required valve position
before
the input signal
reaches the maximum input signal, decrease the actuator/valve travel by rotating the positioner span
adjustment knob away from the zero adjustment nut (key 35) to remove active spring coils from the range
spring.
7. After turning the span adjustment knob to change actuator travel, re‐zero the positioner using the procedure given
Note
The outputs of a properly calibrated positioner will be in the saturated condition (zero pressure or full supply) when the valve is
fully open or closed.
8. Increase the input signal until the input reaches the maximum input signal. Observe the actuator/valve travel as the
input increases.
Repeat steps 3 through 8 until the actuator travel corresponds to the input signal range.
9. Properly align the indicator and replace the positioner cover assembly.
Standard or Beacon Indicator Alignment
Note
The standard, low‐profile indicator consists of the indicator cover (key 14), indicator (key 15) with internal retaining ring (e‐clip)
(key 12), and separate pointer (key 13) recessed into the indicator. An O‐ring (key 15A) fits over the molded screwdriver slot in the
indicator to retain the pointer.
The optional beacon indicator consists of an external unit (key 10) with external retaining ring (key 12) and extension shaft
(key 11).
1. Locate the indicator/extension shaft (key 11 or key 15) inside the front cover. To align the indicator, rotate the
indicator/extension shaft to match the position of the feedback shaft extending from the cam (key 36).
2. Install the cover assembly (key 7) so that the indicator/extension shaft joins with the feedback shaft. The standard
indicator (key 15) features a molded screwdriver slot that protrudes through the indicator cover (key 14). If
necessary, use a small, Phillips head screwdriver to align the indicator with the feedback shaft.