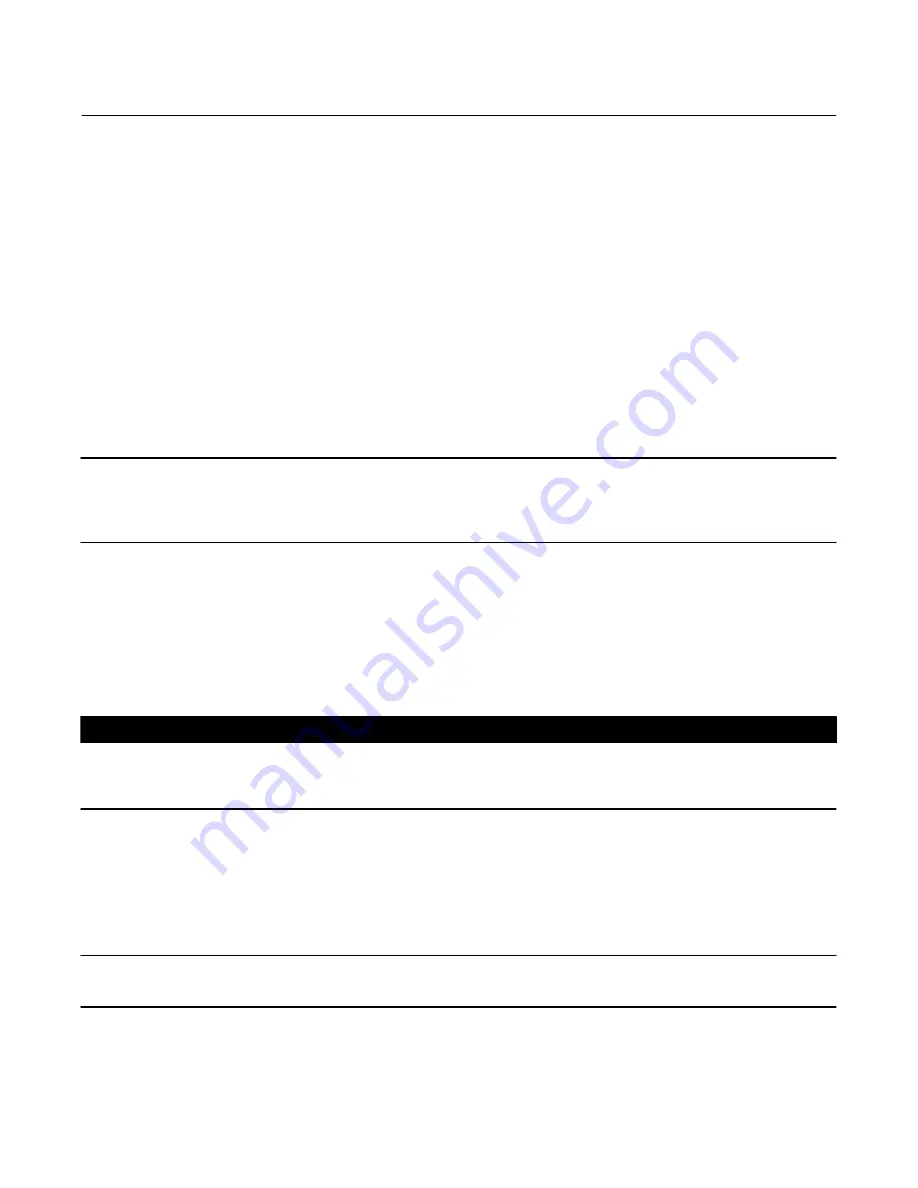
Instruction Manual
D200126X012
2502 Controllers
June 2017
26
1. Remove the controller as described previously.
mount is with the case to the right of the displacer when looking at the front of the case. Left hand mount is with
the case to the left of the displacer. For a 249 sensor, remove the torque tube arm from the sensor or vessel and
reinstall the torque tube arm in the opposite position according to the appropriate instruction manual.
3. Check the desired control action to determine if it is also necessary to reverse the controller action. The nozzle
block and bellows tubing should be arranged in the proper position as shown in figure 13.
4. Remove the RAISE LEVEL dial, turn it over, and install it in the desired position. The arrow on it under the word
FLOAT should point toward the displacer. On a controller with indicator assembly, remove two screws (key 41,
figure 14), turn the front plate (key 54, figure 14) to the side that will have the float arrow pointing toward the
displacer, and secure the plate with the screws.
5. Install the controller according to the next section.
Installing Controller on Sensor
Note
If the installation is in a location that is not readily accessible and shop calibration is required, remove the torque tube arm from
the cage or vessel before mating the controller to the sensor. Install the controller on the torque tube arm in the shop; then
calibrate and return the controller and torque tube arm assembly to the installation.
Perform step 1 only if adding a heat insulator to a unit that does not have one. Key numbers in this step are shown in
figure 12, unless otherwise indicated.
1. To install the heat insulator, secure the shaft extension (key 37) to the torque tube assembly rotary shaft with the
shaft coupling (key 36). Tighten both set screws (key 38), with the coupling centered as shown in the figure. Then
mount the insulator assembly (key 35) on the controller case with four washers (key 53) and button‐head cap
screws (key 40). Tighten the screws.
CAUTION
In the following step, avoid bending the torque tube rotary shaft of the torque tube assembly. Bending or side loading of
this shaft could cause erroneous readings. Additionally, make sure the ball bearing assembly (key 12, figure 14) is removed
from the case (key 1, figure 14) to provide clearance when installing the case on the sensor.
2. Remove the bearing assembly (key 12) from the case (key 1).
3. Carefully slide the controller case straight in, guiding the bearing assembly (key 12), operating arm base or pointer
assembly (key 68 or 51, figure 14) over the rotary shaft and easing an attached heat insulator over the shaft
coupling (key 36) if necessary. Secure the case or insulator to the torque tube arm with the four cap screws (key 39).
Note
If a heat insulator is used, do not insulate its exterior.
4. On a unit without a heat insulator, tape the joint between the case and torque tube arm to minimize the entrance of
atmospheric moisture around the torque tube rotary shaft.