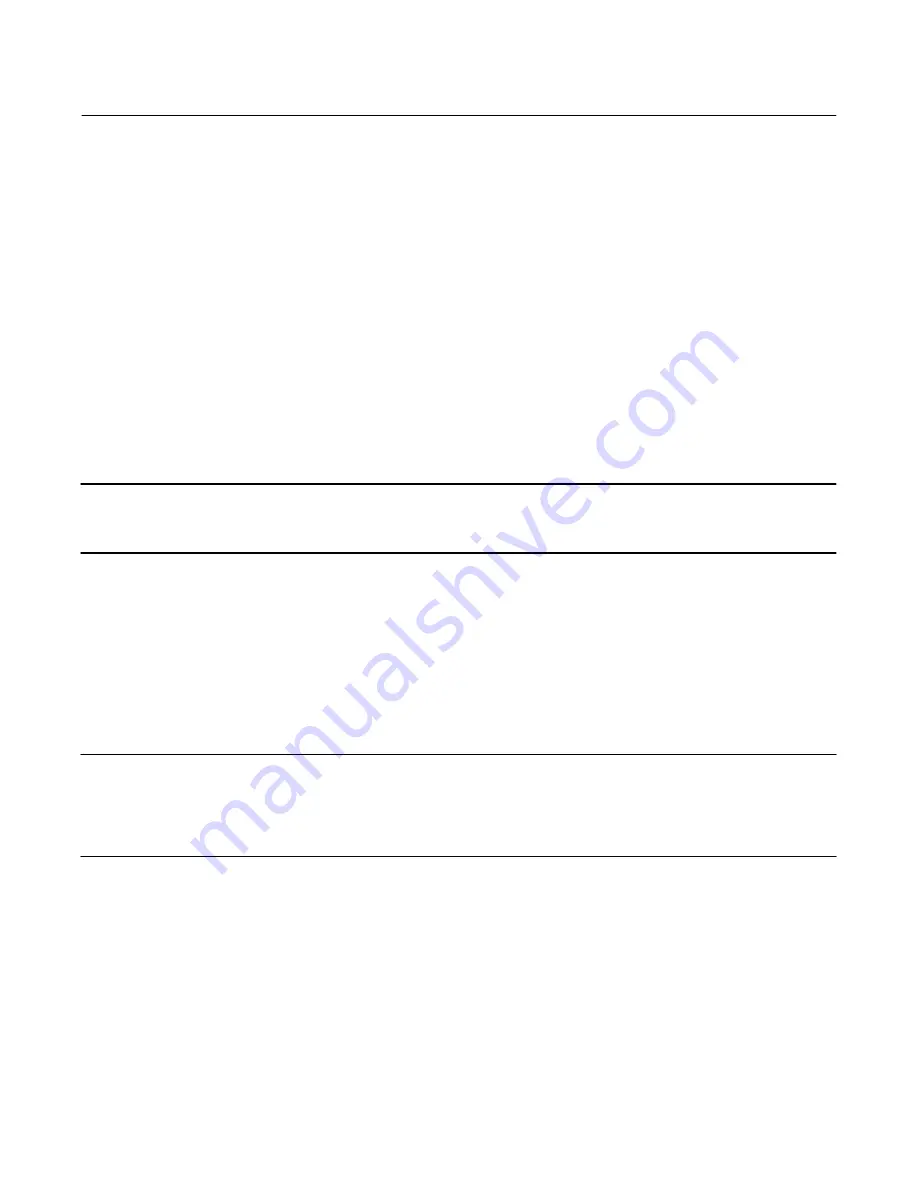
Instruction Manual
D200126X012
2502 Controllers
June 2017
18
1. Connect a supply pressure source to the controller and provide a supply pressure suitable for the sensing element
range: 1.4 bar (20 psig) for a 0.2 to 1.0 bar (3 to 15 psig) output pressure range or 2.4 bar (35 psig) for a 0.4 to 2.0
bar (6 to 30 psig) output pressure range.
2. Rotate the reset knob to 0.01 minutes per repeat.
3. Rotate the proportional band knob to zero.
4. Set the liquid at the minimum limit (dry displacer).
5. Turn the RAISE LEVEL knob to zero.
6. Adjust the nozzle until output pressure is between 0 and 0.2 bar for a 0.2 to 1.0 bar signal range (0 and 3 psig for a 3
to 15 psig signal range) or 0 and 0.4 bar for a 0.4 to 2.0 bar signal range (0 and 6 psig for a 6 to 30 psig signal range).
7. Set the liquid at the maximum limit (covered displacer).
8. Turn the RAISE LEVEL knob until the output pressure is 1.0 bar for a 0.2 to 1.0 bar signal range (15 psig for a 3 to 15
psig signal range) or 2.0 bar for a 0.4 to 2.0 bar signal range (30 psig for a 6 to 30 psig signal range).
9. The controller is within its calibration accuracy if the RAISE LEVEL knob is between the 9.0 and 10.0 positions.
10. If the controller is out of calibration, adjust the calibration adjuster as follows:
Note
Loosen the two calibration adjuster screws (key 45, figure 14), and slide the calibration adjuster (key 100, figure 14) in the desired
direction.
a. If output is
below
1.0 bar for a 0.2 to 1.0 bar signal range (15 psig for a 3 to 15 psig signal range) or 2.0 bar for a
0.4 to 2.0 bar signal range (30 psig for a 6 to 30 psig signal range), move the adjustor a small distance away from
the pivot to
increase
span (movement should be away from the torque tube). Then repeat steps 4 through 9.
b. If output is
above
1.0 bar for a 0.2 to 1.0 bar signal range (15 psig for a 3 to 15 psig signal range) or 2.0 bar for a
0.4 to 2.0 bar signal range (30 psig for a 6 to 30 psig signal range), move the adjustor a small distance toward the
pivot to
decrease
span (movement should be toward the torque tube). Then repeat steps 4 through 9.
Note
If the controller cannot be calibrated, look for other problems as described in the Troubleshooting section, such as a
nonperpendicular flapper‐nozzle condition, leaky connections, or a binding displacer rod. If none of these troubles is apparent, the
displacer or torque tube may be sized for a different set of service conditions. Ensure that the displacer is sized correctly for the
application.
Startup
Adjustment locations are shown in figure 9.
2. Set the percent proportional band control to 200.
3. Set the reset control to .05 minutes per repeat.