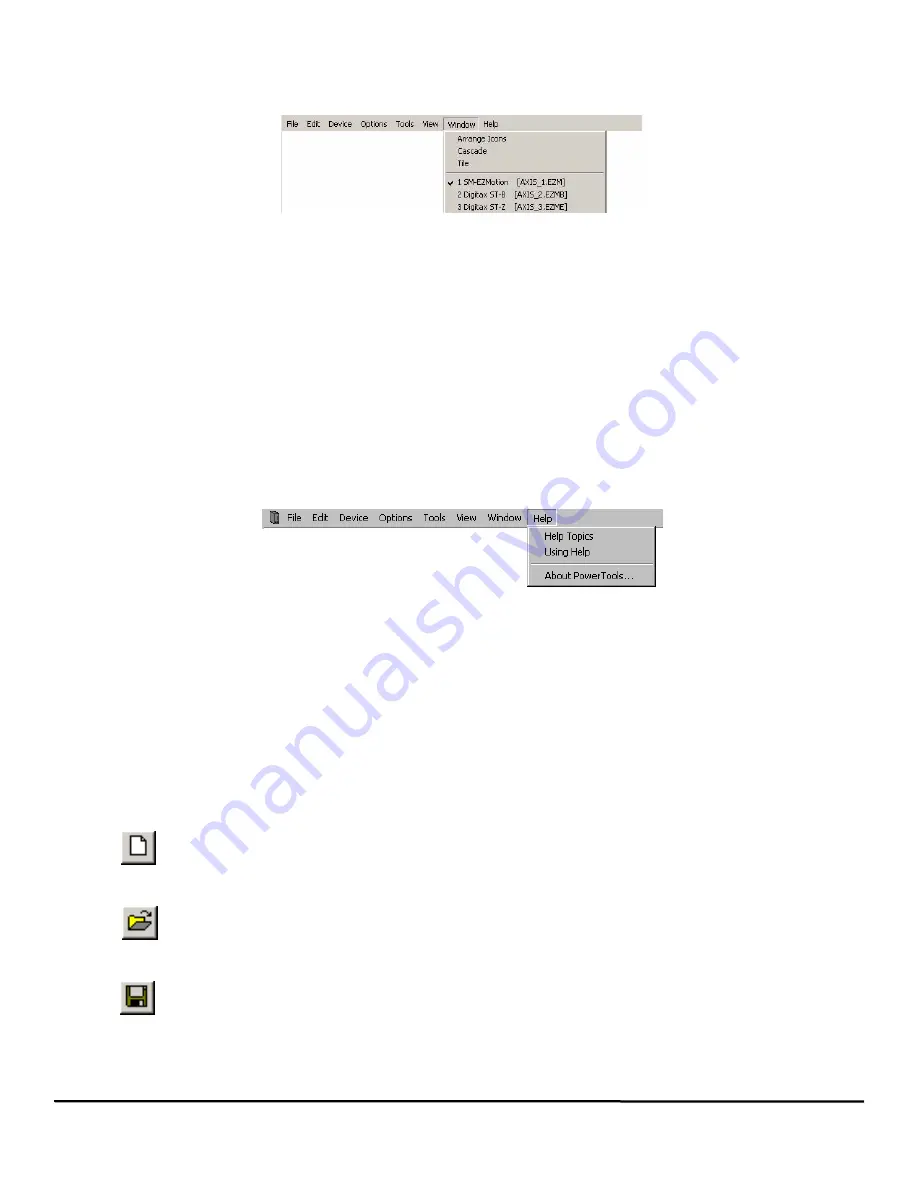
20
EZMotion User/Programming Guide
www.controltechniques.com
Revision: A8
all the original default settings.
4.4.7
Window
Figure 21 shows the
Window
menu as selected from the PowerTools Pro Menu Bar.
Figure 21:
Window Menu
Arrange Icons
No function.
Cascade
If the user has multiple configurations open simultaneously, selecting
Cascade
will neatly layer the windows so the title bars are
visible and the active configuration is in front.
Tile
If the user has multiple configurations open simultaneously, selecting
Tile
will resize each of the windows to have equal area on the
screen. The active configuration will have a highlighted title bar on the window.
Current Files Open
If the user has multiple configurations open simultaneously, each of the open files will be listed on the Window menu. The active file
will have a check mark next to it as seen in Figure 21. By selecting a different file from this list, the selected file will become the
active file.
4.4.8
Help
Figure 22 shows the
Help
menu as selected from the PowerTools Pro Menu Bar.
Figure 22:
Help Menu
Help Topics
By selecting
Help Topics
, the help file will be launched allowing the user to lookup and read information related to the SM-EZMotion
module and PowerTools Pro software.
Using Help
Selecting
Using Help
will launch a window that lets the user select different topics available as part of the help file. This utility makes
it easier to navigate the different sections of the help file.
About PowerTools...
About PowerTools Pro
will open a window that shows what revision of PowerTools Pro software is currently running.
4.5
Toolbar
4.5.1
New
Same as
File
>
New
from the menu bar. Selecting
New
will open a new PowerTools Pro configuration file. The user will
be asked what type of configuration to create. For modules used with the Unidrive SP/Digitax ST, select SM-EZMotion
Setup then the correct drive type.
4.5.2
Open
Same as
File
>
Open
from the menu bar. Selecting
Open
will allow the user to open an existing application created with
PowerTools Pro. Navigate to the directory that the desired file is located in, and double-click on the specific file. Doing so
will open the file for editing.
4.5.3
Save
Same as
File
>
Save
from the menu bar. Selecting
Save
will save the active file on the users PC. The location to which
the file is saved is based on where the file was previously saved. If the file has not yet been saved, the Save As control
box will open instead.
Содержание EZMotion
Страница 2: ......
Страница 12: ...x EZMotion User Programming Guide www controltechniques com Revision A8 ...
Страница 18: ...6 EZMotion User Programming Guide www controltechniques com Revision A8 ...
Страница 36: ...24 EZMotion User Programming Guide www controltechniques com Revision A8 ...
Страница 158: ...146 EZMotion User Programming Guide www controltechniques com Revision A8 ...
Страница 186: ...174 EZMotion User Programming Guide www controltechniques com Revision A8 ...
Страница 266: ...256 EZMotion User Programming Guide www controltechniques com Revision A8 ...
Страница 267: ......