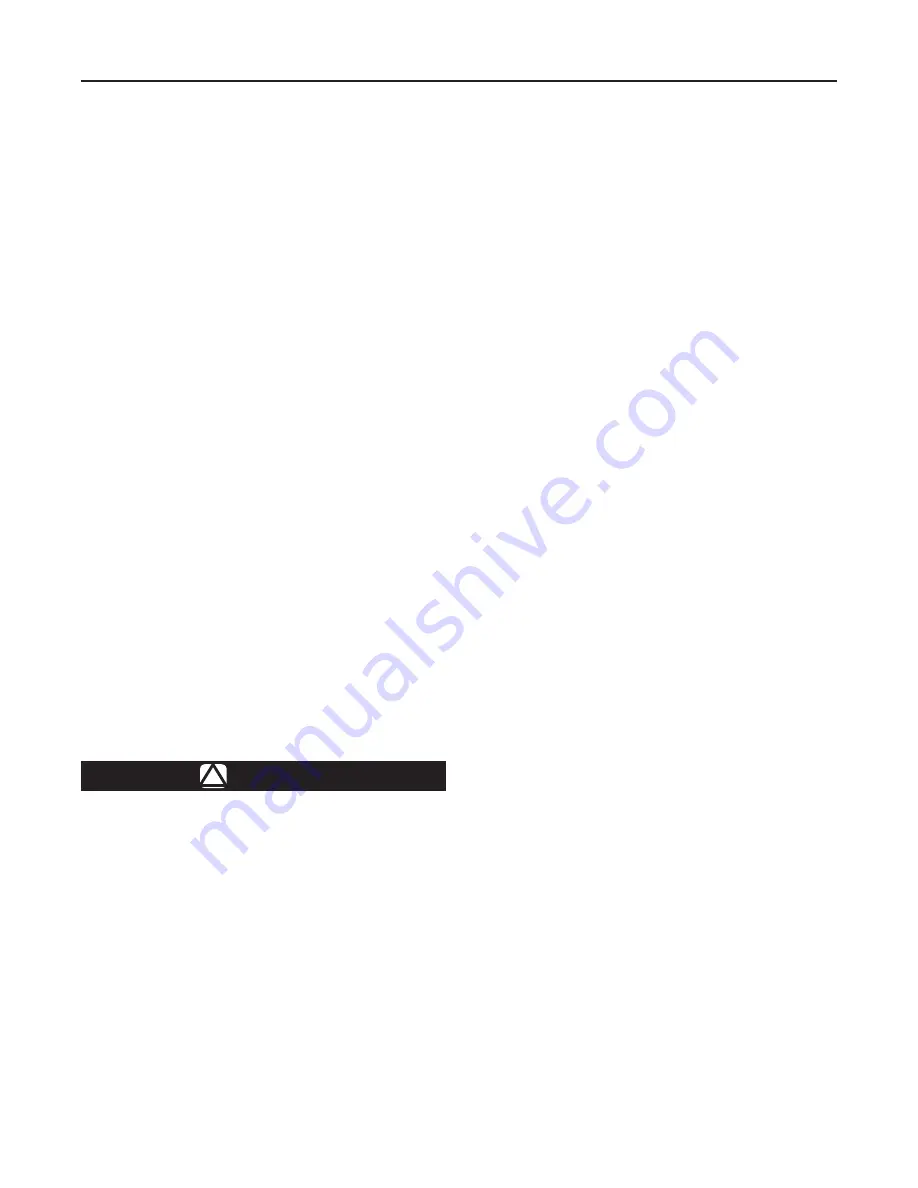
The arrestor should be positioned such that the entire
arrestor is accessible for removal. Install the unit
such that the flow arrow located on the unit points in
the direction travelling with the product flow. Models
that have drain plugs are designed for horizontal
installation and should be installed with the drain plugs
aligned at the bottom of the unit. Models that have
pressure taps are designed to allow pressure gauges
to be installed on both sides of the flame cell assembly
to determine blockage. The pressure taps should
be aligned at the top to allow easy viewing of the
gauges. Units that are equipped with optional internal
cleaning systems should be connected to a source of
cleaning media such as water, steam or other suitable
solvent. Observe recommended installation practice as
detailed bends and/or flow obstruction section.
Flow Direction
The Enardo DFA Series is not bi-directional when
temperature sensors are required unless a sensor
is installed on both sides of the arrestor element
assembly. However, detonation arrestors are rated
for stabilized burning and bi-directional. All arrestors
covered in this manual can be installed either vertically
or horizontally. Consideration should be given to non-
symmetrical assemblies that include features such
as clean-out ports, temperature monitoring device or
other options that might have a preferred installation
direction to suit the needs of the customer.
Piping Expansions and
reductions Adjacent to Detonation
Flame Arrestor
WArninG
!
no instrument, tubing or other device
whatsoever shall circumvent the
detonation flame arrestor in such a
manner to allow a flame path to exist
around the flame element of the arrestor.
When instrumentation is installed in
such a manner that it creates a path
circumventing the flame element of an
arrestor, measures must be taken to
prevent passage of flame through the
instrumentation device and/or system.
instrumentation must be capable
of withstanding the maximum and
minimum pressures and temperatures to
which the device may be exposed and at
a minimum be capable of withstanding
a hydrostatic pressure test of 350 psig /
24 bar.
The Enardo DFA Series detonation flame arrestor may
be installed in any vapor control line that is smaller
than or equal to the nominal pipe diameter of the
arrestor’s connection flanges.
When it is necessary to
increase the diameter of the piping on the downstream
side (unprotected) of the detonation flame arrestor,
a length of pipe at least 120 pipe diameters must be
installed between the detonation flame arrestor and
the expansion. A pipe diameter is considered as the
inside diameter of pipe having a nominal size equal to
the detonation flame arrestor’s connecting flanges.
Maintenance
Detonation Flame Arrestor Element
Assembly Cleaning
1.
Keep the element openings clean to prevent
loss of efficiency in absorbing heat. Remove the
element assembly and clean the elements to
prevent the clogging of particulates and other
contaminants on the openings. Clean the element
with a suitable cleaning media (solvent, soap,
water or steam) then blow dry using compressed
air. Be careful not to damage or dent the cell
openings as this would hamper the effectiveness
of the unit. Do not clean the arrestor elements by
rodding with wire or other hard objects to remove
blockages. Cleaning the elements with wire or
other hard objects could damage the elements and
seriously impair the arrestor’s performance. If the
arrestor element cannot be cleaned satisfactorily,
replace it.
2.
For best cleaning results, use a high pressure
sprayer with spray wand (1500 psig to 3000 psig /
103 to 207 bar) to clean the entire element
surface. Hold the spray nozzle perpendicular
to the surface being cleaned to maximize spray
media penetration into the element. Alternately
spray each side of the element surface until clean.
3. The cleaning interval should be governed by the
amount and type of particulate in the system to
which it is installed and must be determined by
the user. To determine the maintenance interval,
the user should check the element in the first few
months of operation to find how quickly particulate
accumulates in the cells.
7
Enardo DFA Series
Outside North
America Only