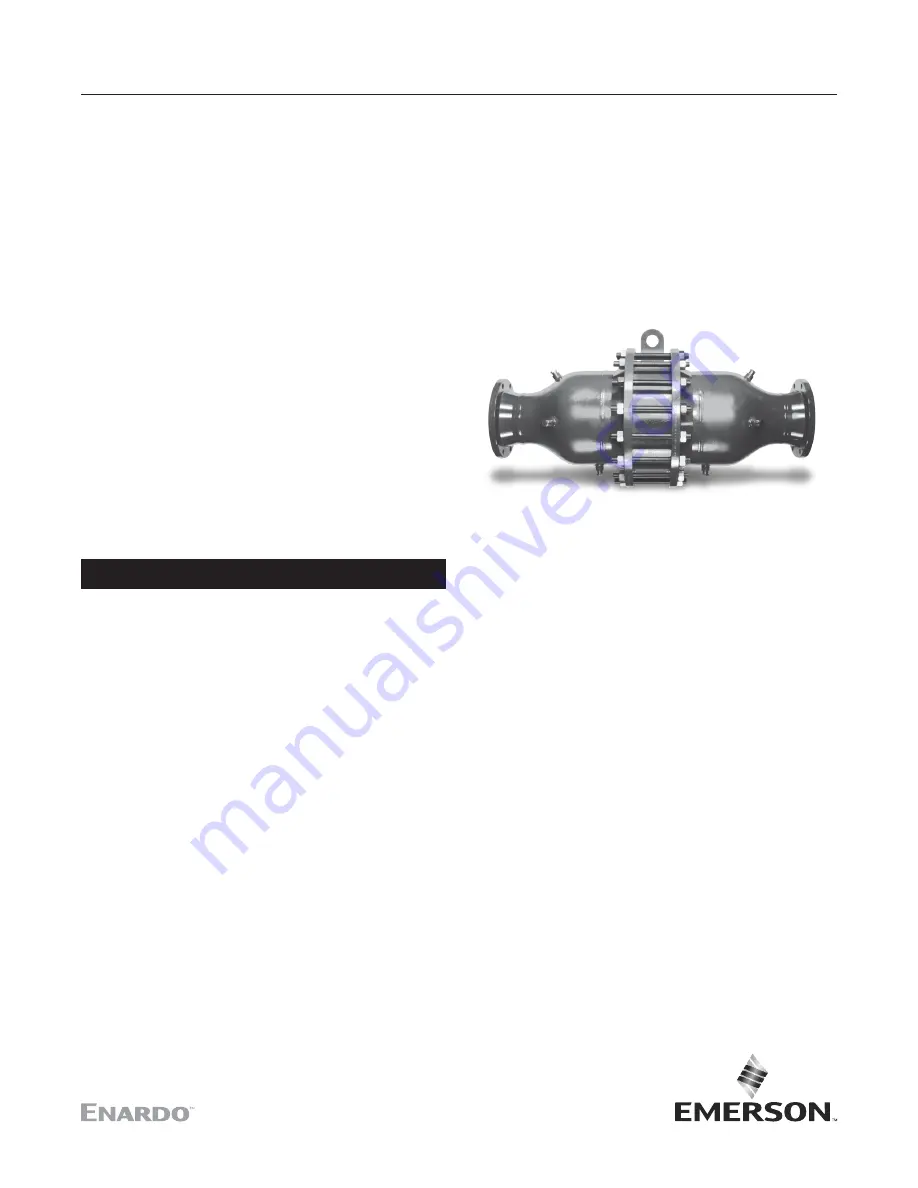
▲
WARNING
Failure to follow these instructions or
to properly install and maintain this
equipment could result in an explosion,
fire and/or chemical contamination
causing property damage and personal
injury or death.
Enardo™ detonation flame arrestor must
be installed, operated and maintained
in accordance with federal, state and
local codes, rules and regulations
and Emerson Process Management
Regulator Technologies Tulsa,
(Emerson) LLC instructions.
Failure to correct trouble could result in
a hazardous condition. Call a qualified
service person to service the unit.
Installation, operation and maintenance
procedures performed by unqualified
person may result in improper adjustment
and unsafe operation. Either condition may
result in equipment damage or personal
injury. Only a qualified person must install
or service the detonation flame arrestor.
EN-DFA Series
North America
Only
Table of Contents
Introduction ..................................................................1
Product Description ....................................................2
Specifications ..............................................................2
Principle of Operation ..................................................3
Factors Affecting Flame Arrestor Performance ............5
Installation ...................................................................8
Maintenance ..............................................................10
Recommended Spare Parts ......................................12
Parts Ordering ...........................................................12
EN-DFA Series Detonation Flame Arrestor
(EN ISO 16852 Certified)
February 2021
Instruction Manual
D103585X012
Introduction
Scope of the Manual
This Instruction Manual provides instructions for
installation, startup, maintenance and parts ordering
information for the EN-DFA Series detonation
flame arrestor.
Flame Arrestor Classification
The flame arrestors within the scope of this
document have been tested and certified as unstable
detonation flame arrestors and are therefore suitable
for deflagrations, stable detonations and unstable
detonations, as defined by EN ISO 16852:2016,
propagating along pipe into connecting pipework.
This is the highest performance rating available for a
detonation arrestor and it exceeds the performance
rating of an arrestor certified for stable detonations and
deflagrations only.
Detonation flame arrestors may be used for open and
closed pipe work on the unprotected (“hot”) side.
Figure 1.
Typical EN-DFA Series Detonation Flame Arrestor