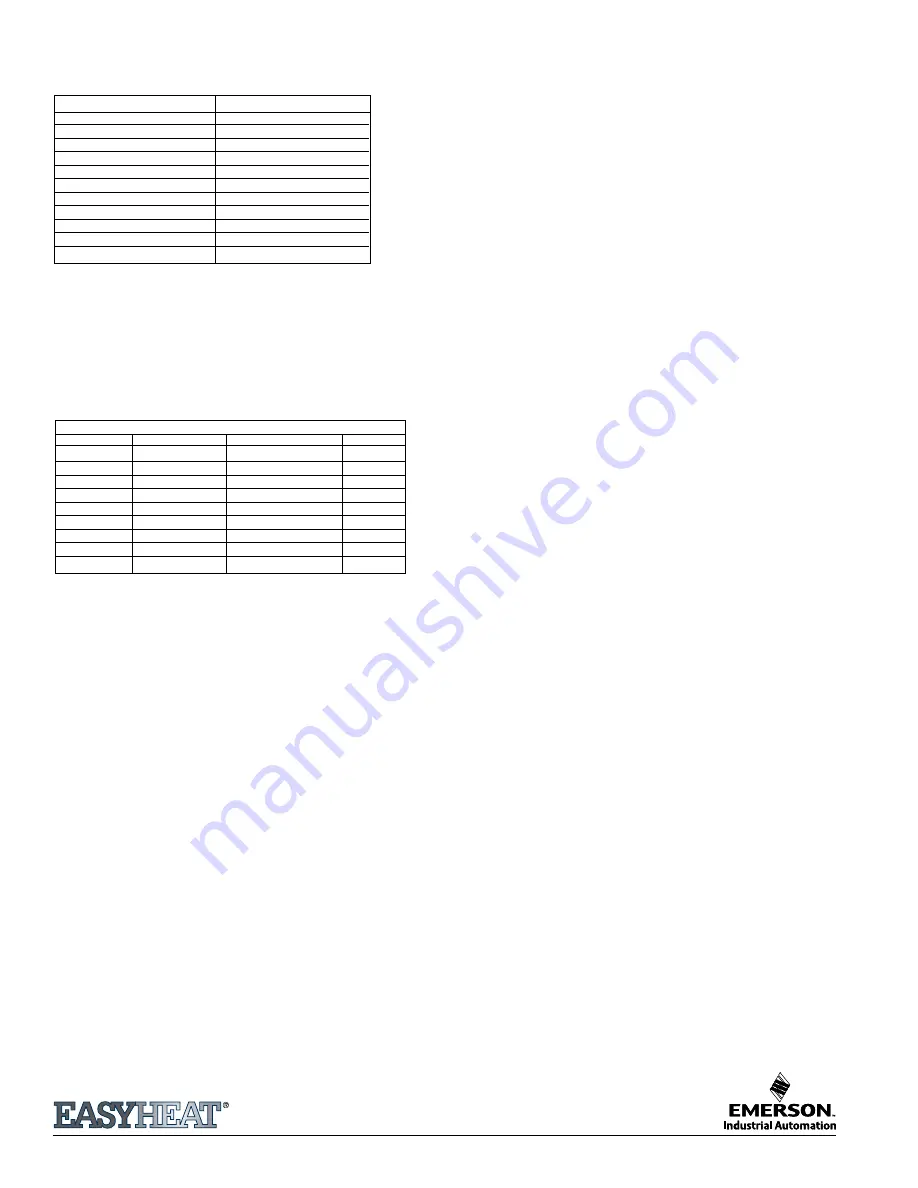
6. DETERMINE CABLE LENgTH
Cable length = pipe length × N + heat sink adjustments × N + slack × N
Slack = power supply (2') + tees (2' per tee) + tails (2' per tail)
N = number of traces
7. CABLE CONTROL
It is recommended that heating cables be controlled by a
thermostat to minimize energy consumption and provide appro-
priate temperature regulation of the pipe contents. Easy Heat
provides a full range of temperature control options, as follows:
ORDINARY AREAS
T4XA, Ambient sensing thermostat
– energizes cables when ambi
-
ent temperature falls below setting. Setting is adjustable from 15
to 140°F (-9.4 to 60°C). NeMA 4X enclosure. use for freeze
protection applications.
C4XC Line sensing thermostat
– energizes cables when line
(pipe) temperature falls below falls below 40°F (4°C). NeMA 4X
enclosure. Use for freeze protection and fuel line temperature
maintenance.
T4XC, Line sensing thermostat
– eenergizes cables when line
(pipe) temperature falls below setting. Setting is adjustable
from 25 to 325°F (-4 to 163°C). NeMA 4X enclosure. use for proc
-
ess control application, including grease lines.
HAzARDOUS LOCATIONS (CII, DIV. 2)
T9EA, Ambient sensing thermostat
– energizes cables when ambi
-
ent temperature falls below setting. Setting is adjustable from 15
to 140°F (-9.4 to 60°C). NeMA 4, 7 and 9 enclosure. use for freeze
protection applications.
T9EC, Line sensing thermostat
– energizes cables when line (pipe)
temperature falls below setting.
Setting is adjustable from 25 to 325°F (-4 to 163°C). NEmA 4, 7
and 9 enclosure. use for process control applications.
EXAMPLE
•
Straight water line (105') to be maintained at 50°F.
•
Minimum ambient temperature is -10°F.
•
Pipe is three-inch diameter steel.
•
Insulation is one inch thick mineral fiber.
•
Three valves
1. CALCULATE TEMPERATURE DIFFERENTIAL
∆T = TF-TA
∆T = 50-(-10)°F
∆T = 60°F
2. HEAT LOSS
Use
Table 1
to find heat loss. Where the desired temperature dif
-
ferential falls between two values, use interpolation:From
Table 1
:
@ 50°F Q = 4.4 w/ft.
@ 100°F Q = 9.2 w/ft.
QF = 4.4 w/ft + 10/50 × (9.2 - 4.4 w/ft.)
QF = 4.4 + .96 = 5.4 w/ft.
3. ADJUSTMENT TO HEAT LOSS
Adjust the heat loss for mineral fiber. From
Table 2
, the adjusment
factor is 1.2.
QM = QF × 1.2
QM = 5.4 w/ft. × 1.2
QM = 6.5 w/ft.
Since the piping is outdoors, no adjustment is necessary for the
absence of wind.
4. DETERMINE CABLE POWER
Select 8 w/ft cable. Apply single cable straight along the pipe.
5. ADJUSTMENT FOR HEAT SINKS
From
Table 3
, an additional 3 feet of cable is required at each
valve.
6. DETERMINE CABLE LENgTH
Length = 105 × 1 + 3 × 3 + Slack
Slack = 2 + 0 × 2 + 1 × 2 = 4
Total Length = 114 + 4 = 116'
7. SELECT ACCESSORIES
•
use line sensing control T4X6 with adjustable setting
set to 50°F.
•
Power connection kit adjustable setting set to 50°F.
•
Power connection kit
Table 2 – Insulation Factors
Insulation Type
Correction Factor
Glass Fiber
1.00
Calcium Silicate
1.72
Cellular Glass
1.84
Rigid Urethane
0.76
Foamed Elastomer
1.16
mineral Fiber
1.20
expanded Perlite
1.42
mineral Wool
1.04
Polystyrene
1.04
Flexible elastomer
1.16
Polyisocyanarate
0.68
5. ADJUSTMENTS FOR HEAT SINKS
Any thermally conductive item that protrudes through the insulation
will require extra heat to be applied to the pipe. The footage shown
in
Table 3
should be added to the required heater cable length
to compensate for these extra heat losses. When multiple-tracing
or spiraling cable, increase the cable adders proportionately.
Table 3 – Heat Loss Adder
Additional Heater Feet for Various Heat Sinks
Pipe Size
Flange
Pipe Support (1) Valve
.50
.5
1.0
1.0
.75
.5
1.5
1.5
1.00
.5
1.5
2.0
1.50
.5
1.5
2.5
2.00
.5
2.0
2.5
3.00
.75
2.0
3.0
4.00
.75
2.5
4.0
6.00
1.0
2.5
5.0
8.00
1.0
2.5
7.0
©2009 Easy Heat
www.easyheat.com