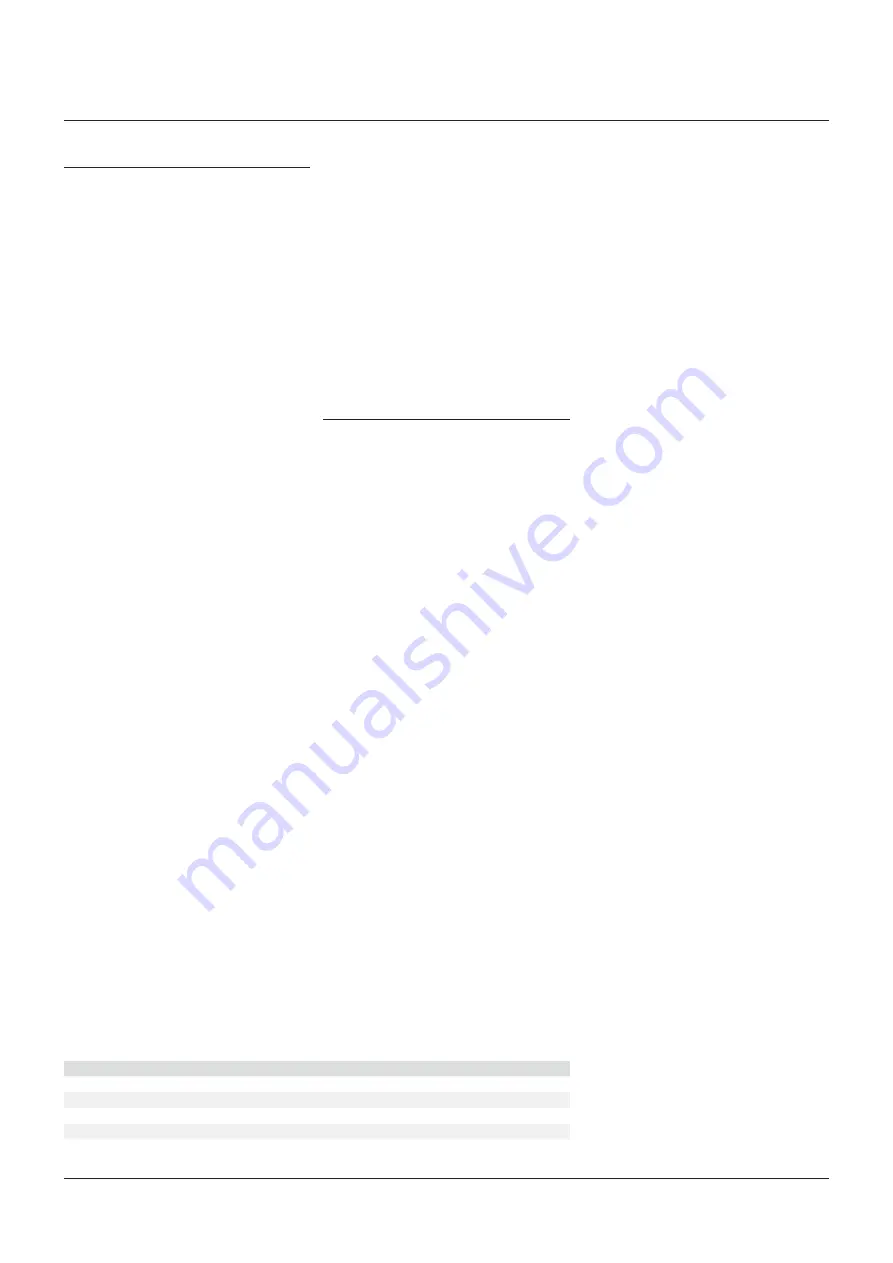
6
CROSBY
STYLE HSL SAFETY VALVES
INSTALLATION, MAINTENANCE AND ADJUSTMENT INSTRUCTIONS
9 SET PRESSURE TESTING
Although each HSL has been set and tested at
the factory or the certified assembler location,
sometimes it is necessary or desirable to test
the valve prior to installation in order to meet
local jurisdictional requirements. The valve
may be tested either in a steam test facility
with the capacity to over pressure the valve,
or on site by using an in-line test device or by
over-pressuring the boiler on which the valve
will be installed. If the valve will be tested on the
boiler by over-pressuring the system it may be
necessary to gag any other pressure relief valves
mounted on the same boiler.
NOTE
Use of an in-line test device may require dimensional
information specific to the type and size valve being
tested. Contact your local Emerson sales or service
office for this information.
The HSL is designed to open with a sharp
pop at the nameplate set pressure (within the
tolerances shown in Table 1) and remain open,
relieving full capacity at 3% overpressure.
As pressure decays below the popping pressure,
the valve will remain open until the blowdown
pressure is reached. The valve will then reseat.
When testing a valve on a steam test stand or
on the end user’s boiler without using a in-line
test device, the pressure should be increased
slowly until the valve opens, but no higher than
3% above the nameplate set point of the valve.
To ensure the valve is adjusted accurately at least
two test cycles shall be observed with the valve
opening within the tolerances shown in Table 1.
If the valve opens outside the tolerance shown in
Table 1, or fails to open by 3% over nameplate set
point, the valve may require adjustment.
WARNING
Steam under pressure can be extremely
hazardous to personnel and can cause serious
injuries including burns and scalds from the
high temperatures of the steam. Care should be
taken to protect testing personnel to prevent any
exposure to released steam from the discharge
or spring chamber of the valve. Appropriate safety
equipment, including hearing protection, should be
worn at all times when servicing a steam pressure
relief valve.
TABLE 1 - TORQUE VALUES FOR VALVE ASSEMBLY
Set pressure, psi (MPa)
Tolerance - plus or minus from set pressure
≤ 70 (0.5)
2 psi (15 kPa)
> 70 (0.5) and ≤ 300 (2.1)
3% of set pressure
> 300 (2.1) and ≤ 1.000 (7.0)
10 psi (70 kPa)
> 1.000 (7.0)
1% of set pressure
Seat tightness testing
After the set pressure has been determined by
testing and any final adjustments are made,
the valve should be tested to assure it meets
acceptable seat tightness levels. In order
to perform this test it is suggested the test
pressure be raised and held at 93% of set point
and the valve observed for signs of any 'visible
leakage'. This is accomplished most easily by
viewing the discharge flange of the valve from
the side against a dark background in order to
see any steam leakage. In most cases, if the
valve leaks by the seat, this can be remedied by
re-lapping of the seating surfaces of the nozzle
and disc.
10 VALVE ADJUSTMENTS
Set pressure adjustment
Set pressure adjustment should not be
necessary on a new valve but if the valve is
tested and does not test within the required
set point tolerances, it may be necessary to
adjust the spring compression by tightening
the adjusting bolt (see instructions below).
For parts identification see Figure 1 and 2.
Before making any adjustments, reduce the
system pressure under the valve 10% - 20%
below the set pressure stamped on the valve.
This will prevent damage to internal parts and
minimize the chance of an inadvertent valve
opening.
A. Remove the cap and lifting lever device
following the instruction on page 7.
B. Loosen the adjusting bolt nut (16/19).
C. Turn the adjusting bolt (15/18) clockwise to
increase set pressure or counterclockwise
to reduce set pressure.
D. Retighten the adjusting bolt nut (16/19)
following each adjustment.
E. Repeat the testing process to determine
if the valve will open within the tolerance
shown in Table 1 for at least two test cycles.
F. Continue to adjust the valve until it is
observed to open within tolerance for at
least two test cycles.
G. Once the set pressure has been established,
replace the cap and lifting lever device
following the instruction on page 11 and
install a new seal and wire.