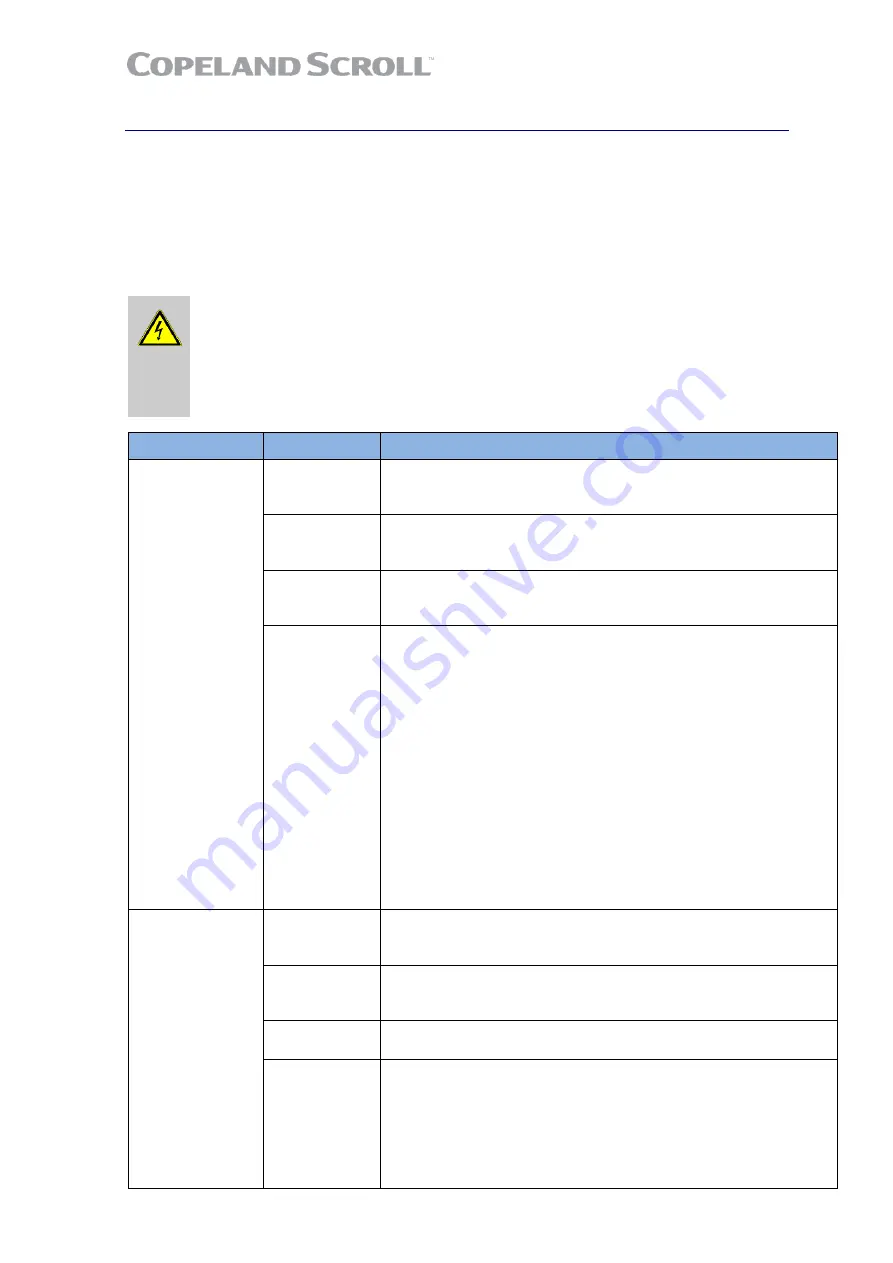
30
AGL_HP_ST_YHK1E_E_Rev02
7
Troubleshooting
Most in-warranty electrical failures are a result of mechanical problems (particles in the oil, liquid
refrigerant in the oil, etc.) and most mechanical problems are a result of system problems. Unless
the reason for the failure is found, replacing the compressor will probably lead to another compressor
failure.
If the compressor fails to start and run properly, it is important that the compressor be tested to
determine its condition. It is possible that electrical components may be defective, the protector may
be open, or a safety device may have tripped. Here is a list of the most common compressor
problems encountered in the field.
WARNING
Electrical cables! Electrical shock!
Before attempting any electrical
troubleshooting, make sure all grounds are connected and secure and there
is ground continuity throughout the compressor system. Also ensure the
compressor system is correctly grounded to the power supply. If you are not
a qualified service person familiar with electrical troubleshooting techniques,
DO NOT PROCEED until a qualified service person is available.
Condition
Cause
Corrective action
The scroll
compressor does
not run, instead a
buzz sound can be
heard
Wired
incorrectly
Check the power supply on the compressor terminals if there is
voltage measured. Trace the wiring diagram to see where the
circuit is interrupted.
Low supply
voltage
If the voltage falls below 90 % of the nameplate voltage, the motor
may develop insufficient torque. Make sure the compressor is
supplied with rated nominal voltage.
Shorted or
grounded motor
windings
Check the motor for ground by means of a continuity check
between the terminals. If grounded replace compressor.
Internal
compressor
mechanical
damage
Refrigeration migration: When the compressor is switched off for a
long period, refrigerant can condense in the crankcase. If the
compressor body is colder than the evaporator, refrigerant will
move from the evaporator to the compressor crankcase.
Refrigerant migration normally occurs when the compressor is
installed in a cold area. A crankcase heater and/or a pumpdown
cycle provide good protection against refrigerant migration.
Acid formation: Acid forms in the presence of moisture, oxygen,
metal, salts, metal oxides and/or high discharge temperatures. The
chemical reactions are accelerated at higher temperatures. Oil and
acid react with each other. Acid formation leads to damage of the
moving parts and in extreme cases to motor burnout. Several
different test methods can be used to test for acid formation. If acid
is present a complete oil change (including the oil in the oil
separator) will help. A suction filter which removes acid should also
be fitted. Check filter-drier condition.
The scroll
compressor does
not run, no buzz
sound can be
heard
Compressor
motor
protector open
Check if there is continuity on the compressor external protector.
If the compressor is warm, it may require considerable time to
cool down.
Defective
system control
components
Check if the pressure control or thermostat works properly or if the
controls are open.
Power circuit
open
Check the fuse for a tripped circuit breaker or for an open
disconnected switch.
Burned motor
winding
If motor burnout is due to undersized contactors, one will observe
that the contacts are welded together. Complete motor burnout on
all three phases despite the presence of a functioning protection
system can be the result. For sizing information please check the
contactor manufacturer data sheet. If the application of the
compressor is changed the contactor sizing should be rechecked.
Check for unbalanced voltage.
Содержание Copeland Scroll YH16K1E
Страница 1: ...Copeland Scroll Compressors for Heat Pump Applications YH04K1E to YH16K1E Application Guidelines ...
Страница 4: ...AGL_HP_ST_YHK1E_E_Rev02 9 References 33 DISCLAIMER 33 ...
Страница 5: ......
Страница 39: ...34 AGL_HP_ST_YHK1E_E_Rev02 ...