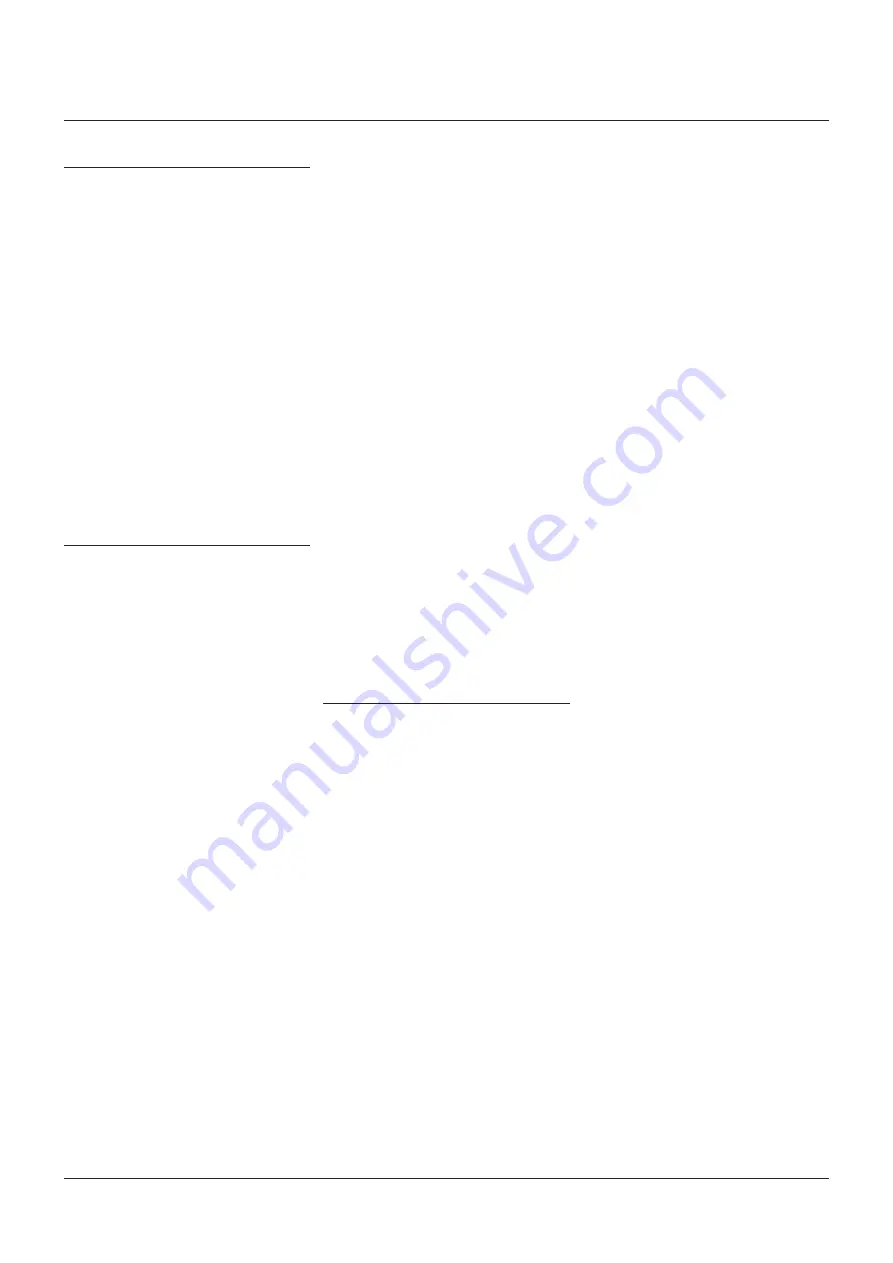
4
KTM
PNEUMATIC ACTUATORS - AW, AWN SERIES
INSTALLATION AND OPERATION MANUAL
SECTION 7 - MOUNTING OF ACTUATOR TO VALVE
Ensure the following items before mounting the
actuator to the ball valve.
1. Cleanse flanges of actuator and valve of
dust and foreign substances.
2. When mounting, make sure that the valve
opening (fully open or fully closed) coincides
with the indicator position of the actuator.
Caution
Mismatching between indication of actuator and
valve opening may result in operation trouble,
which will cause accidents. Check the indication
matching once more.
3. Use the following bolts for connection,
which should be fastened in “criss-cross”
pattern.
Stainless steel: JIS: SUS304 (AISI 304) with
strength class more than 70
Carbon steel: JIS: S45C (AISI 1045) with
strength class more than 8.8
SECTION 8 - ADJUSTMENT OF VALVE OPENING
After mounting the actuator to the valve, adjust
fully open and fully closed position according to
the following manner.
CAUTION
Since the adjusting procedure is performed
during supplying compressed air, do not touch the
moving parts of the actuator. Doing so may cause
injury.
For supplying the compressed air, refer to
Section 9 “Piping and Installation”.
The procedure explained below applies to
the combination of actuator and valve, when
turning the stem clockwise operates the valve
to closed position.
8.1 Procedure for Double Acting Actuator
1. Supply compressed air to inlet port to open
the valve and check fully open position of the
valve.
2. If the position is not correct, exhaust the
compressed air and perform steps 4 and 5.
3. Loosen hexagon nut for locking stopper
bolt on open side, turn the stopper bolt
in respective direction by using hexagon
bar wrench. Clockwise turning of the bolt
reduces travel angle of the actuator, and
counterclockwise turning widens the range
of the travel angle.
4. After ensuring correct position of the valve
by supplying compressed air to the actuator,
tighten the locking nut of the stopper bolt.
5. Supply compressed air to inlet port to close
the valve and check the fully closed position.
6. If the position is not correct, perform the
above described procedure for closed side
stopper bolt.
8.2 Procedure for Single Acting Actuator
(including the model with manual operator “HW”)
1. Supply compressed air to the inlet port to
the valve open and check fully open position
of the valve.
2. If the position is not correct, exhaust the
compressed air letting the valve to close the
valve. Then perform the following steps 3
and 4.
3. Loosen hexagon nut for locking open
side stopper bolt, turn the stopper bolt
in respective direction by using hexagon
bar wrench. Clockwise turning of the bolt
reduces travel angle of the actuator, and
counterclockwise turning widen the range of
the travel angle.
4. After ensuring correct position of the valve
by supplying compressed air to the actuator,
tighten the locking nut of the stopper bolt.
5. With no compressed air in the actuator,
check the fully closed position of the valve.
6. If the position is not correct, loosen the
hexagon nut for locking stopper bolt on
closed side, then perform the following
procedures 7 and 8.
7. Turn the stopper bolt in the respective
direction by using hexagon bar wrench.
Clockwise turning of the bolt reduces travel
angle of the actuator, and counterclockwise
turning widen the range of the angle.
8. After ensuring the correct position of the
valve, tighten the locking nut of the stopper
bolt.
SECTION 9 - PIPING AND INSTALLATION
When operating actuator in piping work, please
pay attention to the following points.
1. Avoid installing the actuators in a place
where they are exposed to seawater,
chemicals, and high- and/or low-
temperature (above 80ºC, under -20ºC).
If it is inevitable, protect the actuators by
appropriate covering, or protect sufficiently
with anticorrosive painting.
2. Usually, copper tubes are used for
connecting attachments. When the joints
loosen by intensive vibrations, air leakage
may occur. Additional tightening will be
necessary accordingly. In vibrational
environments, use Nylon tubing.
3. Since accessories have been adjusted
already in the factory, further adjustments
are not necessary.
4. For air piping of accessories, use Φ8 xΦ6
tube or larger for AWN13~AW20, and
Φ10 xΦ8 tube or larger for AW28. If quick
operation is required, use large size tube
according to the desired speed.
5. For air piping from compressor or air tank
to supply port of actuator (or inlet port of
attachment device, if equipped), use steel
pipe of size not smaller than the air supply
port of the actuator.
CAUTION
In piping work, care should be taken for
fragments of the sealing tape not to enter in
the pipe. Foreign matters in the tube will cause
malfunctions of accessories.
WARNING
Never climb on the actuator or accessories in field
working, which will cause failure in adjustment or
human injury.