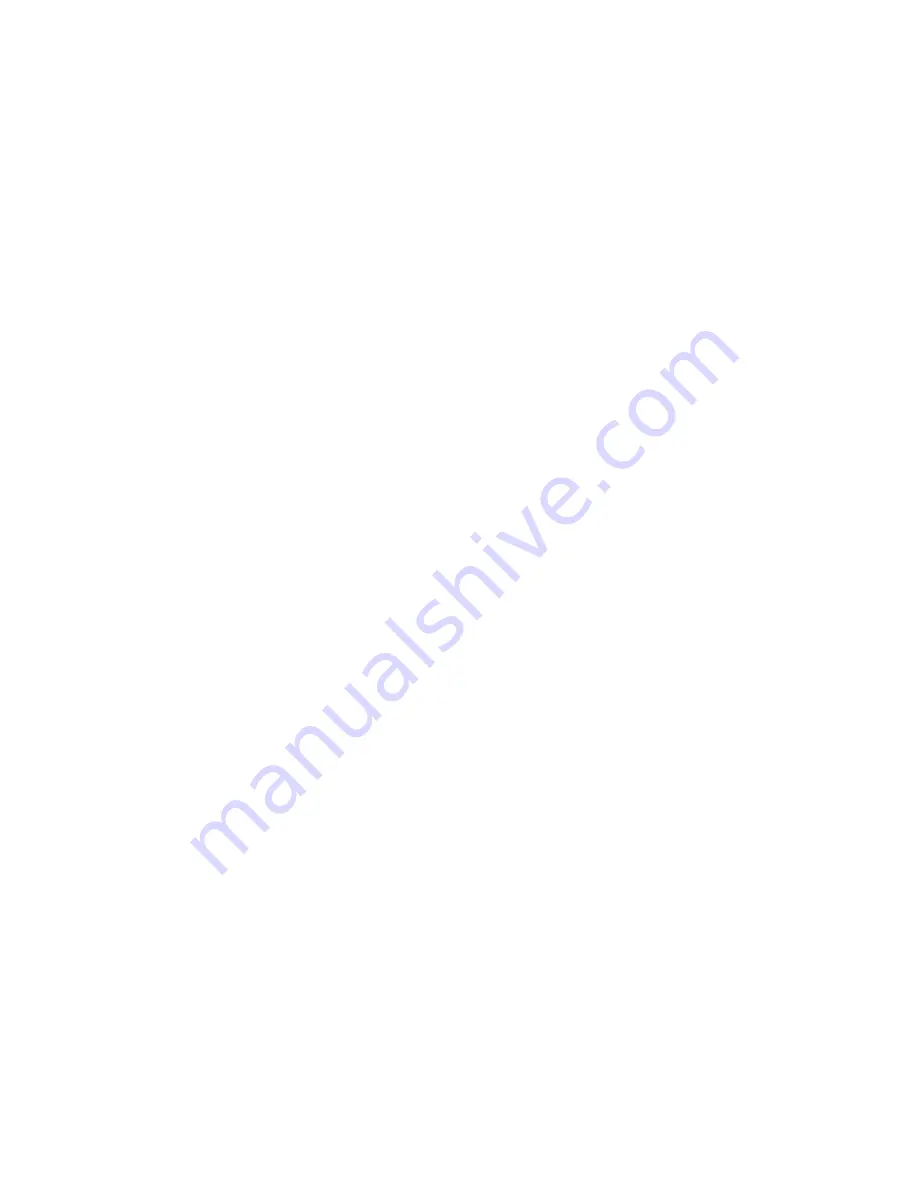
EmersonClimate.com/FlowControls
Technical Support: 1-866-625-8416
PA-00376 R1 (10/14) Emerson is a trademark of Emerson Electric Co. ©2014 Emerson Climate Technologies, Inc. All rights reserved.
•
If the piping results in excessive stress to the joints of the
oil separator, the pipes must be supported by suitable
mounting bracket(s).
Leak Test
• After completion of installation, a pressure test must be
carried out as follows:
- According to EN378 for systems which must comply with
European pressure equipment directive 971231EC.
- To maximum working pressure of systems for others
applications.
Warning
1) Failure to perform a leakage test could result in loss of
refrigerant and personal injury.
• In case of leakage around the flange of the oil separator
(flanged type), check the gasket and the tightness of bolts
with 35 Nm torque. A spare gasket is supplied with each
flanged type oil separator.
• After leakage test, the unused spare gasket should be
saved for future service.
Operation
• After leakage test, start system. The oil level in the
compressor crankcase and in the oil reservoir must be
observed after start-up, the first few hours of operation
and a couple days later. The new refrigerant will mix with
some oil. There may be a small portion of oil trapped in
the system.
• The oil separator removes the excess oil, but this may not
be returned to the compressor crankcase immediately.
In normal operation, the oil return line to the compressor
crankcase or to the oil reservoir will be alternately hot
and cold. This is caused by opening and closing of the
needle valve via lifting and lowering the float mechanism.
• In some outdoor installations, the oil separator may be
subject to low ambient temperature conditions. In this
case, it must be insulated to prevent the condensation
of any refrigerant it passes. If condensed, the liquid
refrigerant could be passed through the return line into the
compressor crankcase, foaming the oil which could result
in lubrication issues.
• Oil separators perform best when operating at or near
the compressor discharge temperature. It is advisable to
insulate the oil separator shell.
Warning
During operation of the system, the shells have a high surface
temperature.
Service Tips
• Oil separator F Types are equipped with a flange and can be
opened for cleaning. Always use a new gasket and tighten
the bolts to 35 Nm. torque.
• The external surface of the shells are coated with epoxy
paint for optimum protection against corrosion. The external
surface of the shell should be checked as per EN-378
during routine inspection and service.